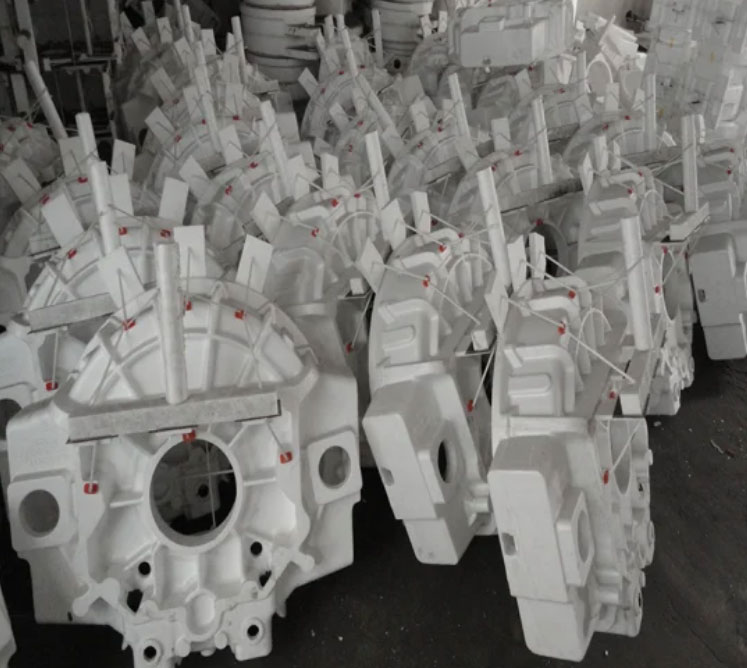
Lost foam casting offers numerous advantages, but like any manufacturing process, it comes with its own set of challenges. Overcoming these challenges is essential to ensure successful and high-quality castings. Here are some tips and best practices to overcome common challenges in lost foam casting:
1. Foam Pattern Design:
- Optimize the foam pattern design to achieve the desired complexity and precision. Use appropriate foam densities and ensure uniform thickness throughout the pattern to prevent distortion during casting.
2. Pattern Handling and Storage:
- Handle foam patterns with care to avoid damage or deformation. Proper storage in a controlled environment is essential to maintain pattern integrity.
3. Foam Pattern Coating:
- Apply a refractory coating to the foam pattern to improve surface finish, reduce foam degradation during casting, and prevent metal penetration into the foam.
4. Gating and Riser Design:
- Optimize gating and riser design to ensure proper metal flow and minimize turbulence. Proper gating and riser placement help prevent defects like shrinkage and porosity.
5. Metal Pouring and Cooling:
- Control the pouring and cooling processes to avoid defects such as cold shuts and surface imperfections. Monitor metal temperature and control the cooling rate to prevent thermal stresses.
6. Mold Quality and Venting:
- Ensure mold quality to achieve accurate casting dimensions and surface finish. Proper venting is crucial to allow gases to escape during casting and prevent porosity.
7. Mold Filling Rate and Pressure:
- Achieve a controlled and uniform filling rate to prevent erosion and metal splash. Proper pressure during casting helps avoid incomplete filling and defects.
8. Foam Pattern Removal:
- Implement gentle and precise foam pattern removal techniques to avoid damaging the mold. Any debris left behind can lead to defects in the casting.
9. Quality Control and Inspection:
- Implement robust quality control measures throughout the process to identify and rectify issues early on. Perform visual inspections and non-destructive testing to ensure casting integrity.
10. Operator Training and Expertise:
- Ensure that operators are properly trained and have sufficient expertise in lost foam casting techniques. Skilled operators can troubleshoot issues and optimize the process for better results.
11. Collaboration with Foundries:
- Collaborate closely with foundries experienced in lost foam casting to leverage their expertise and gain valuable insights into optimizing the process for specific applications.
12. Continuous Improvement:
- Emphasize continuous improvement and learning from each casting to refine the process and overcome challenges effectively.
By following these tips and best practices, manufacturers can overcome common challenges in lost foam casting and produce high-quality, intricate, and near net shape castings with precision and consistency. Proper process control, skilled craftsmanship, and stringent quality control measures are essential to ensure the success of the lost foam casting process.