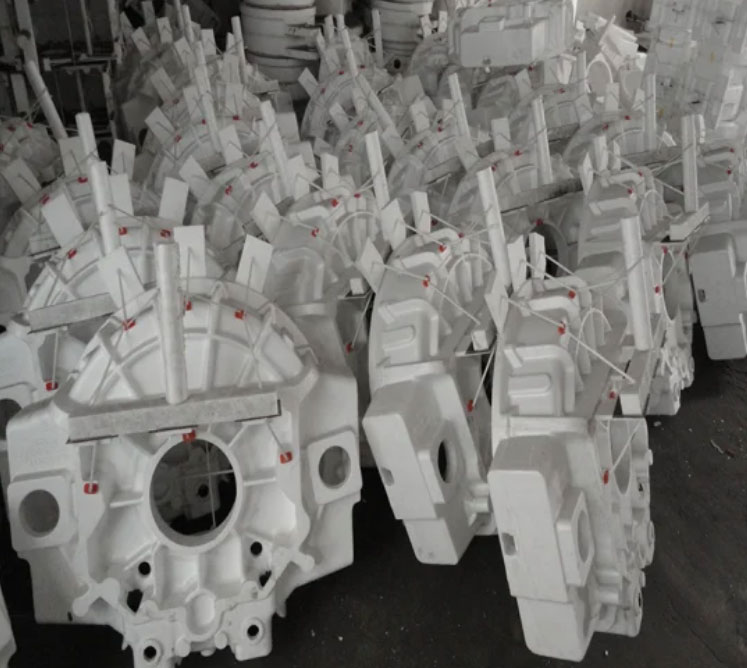
Lost foam technology offers several ways to enhance casting quality and efficiency, making it a valuable and competitive option in modern foundries. By leveraging the benefits of this innovative casting method, manufacturers can improve product quality, reduce defects, and optimize the casting process. Here are some key ways in which lost foam technology enhances casting quality and efficiency:
1. Design Flexibility:
- Lost foam casting allows for intricate and complex designs, providing greater design freedom compared to traditional casting methods. This enables the production of components with intricate geometries, reducing the need for complex assemblies and improving overall product performance.
2. Near Net Shape Casting:
- Lost foam casting produces near net shape castings, which means that the final casting closely resembles the desired shape with minimal machining or finishing required. This reduces material waste, machining costs, and overall lead times.
3. Dimensional Accuracy:
- Lost foam casting offers high dimensional accuracy, as the foam patterns maintain their shape during the casting process. This results in precise and consistent castings, reducing the need for additional dimensional corrections.
4. Smooth Surface Finish:
- Lost foam castings typically have a smooth surface finish, reducing the need for additional surface treatments or polishing. This enhances the aesthetics of the castings and reduces post-casting finishing time.
5. Complex Assemblies Consolidation:
- Lost foam casting allows for the integration of multiple components into a single casting, reducing the need for separate parts and assembly processes. This simplifies the overall manufacturing process and improves product integrity.
6. Improved Gating and Riser Design:
- Lost foam casting enables the optimization of gating and riser design to promote better metal flow, reduce turbulence, and minimize defects like porosity and shrinkage.
7. Reduced Defects:
- Lost foam technology minimizes the risk of defects like sand inclusions, mold shift, and core mismatches, as there are no sand molds or cores to introduce contaminants.
8. Efficient Use of Energy:
- Lost foam casting requires less energy compared to some other casting processes, as it eliminates the need for pattern removal and cleaning steps.
9. Rapid Prototyping:
- The ease of creating foam patterns allows for rapid prototyping and iteration of designs. This enables faster development cycles and reduces time-to-market for new products.
10. Sustainable Practices:
- Lost foam technology promotes sustainable practices through reduced material waste, energy efficiency, and the ability to recycle or reuse foam patterns.
By optimizing the design, gating, and casting parameters, foundries can achieve improved casting quality and productivity with lost foam technology. Proper process control, skilled craftsmanship, and stringent quality control measures are essential to maximize the benefits of lost foam casting and ensure the production of high-quality, cost-effective castings.