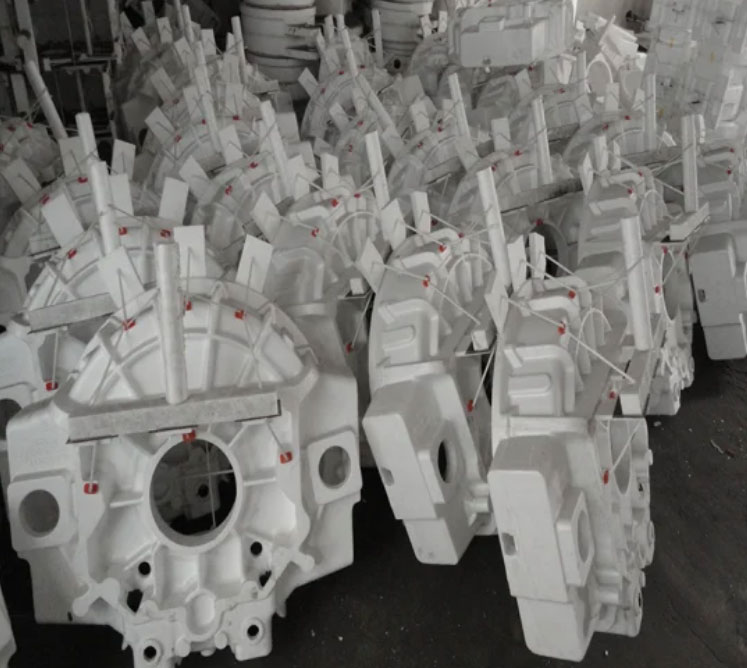
Innovations in lost foam casting (LFC) are continuously shaping the future of metal casting. As technology advances and industry demands evolve, researchers and manufacturers are exploring various ways to enhance the process and expand its capabilities. Here are some key innovations in lost foam casting that represent the future of metal casting:
1. Advanced Materials and Alloys:
The use of advanced materials and alloys in lost foam casting is an ongoing area of innovation. Researchers are investigating the use of high-performance materials and composites to produce lightweight and high-strength components for aerospace, automotive, and other industries. These materials offer improved mechanical properties and resistance to extreme conditions, opening up new possibilities for application-specific castings.
2. Additive Manufacturing Integration:
The integration of additive manufacturing (3D printing) with lost foam casting holds significant potential for complex part production. By 3D printing precise foam patterns directly or producing intricate sand molds for the casting process, foundries can further expand design freedom, reduce tooling costs, and accelerate prototyping and production cycles.
3. Digital Design and Simulation:
Digital design and simulation tools are advancing to optimize lost foam casting processes. Finite element analysis (FEA) and computational fluid dynamics (CFD) simulations aid in predicting casting defects, optimizing gating and risering systems, and ensuring the integrity of castings. Virtual prototyping allows for design validation before physical casting, reducing the number of iterations required.
4. Sustainable Casting Practices:
Environmental concerns are driving innovations toward more sustainable lost foam casting practices. Research is focused on reducing energy consumption, developing eco-friendly binders and refractory coatings, and exploring greener disposal methods for used foam patterns. These efforts aim to minimize the environmental impact of the casting process.
5. Real-Time Process Monitoring:
Advancements in sensor technology enable real-time process monitoring during lost foam casting. Implementing sensors for temperature, pressure, and other critical parameters allows for immediate feedback and adaptive control, leading to higher process reliability and consistent casting quality.
6. Automation and Robotics:
Automation and robotics are being integrated into lost foam casting operations to enhance productivity and reduce manual labor. Automated pouring systems, robotic handling of foam patterns and castings, and smart manufacturing approaches streamline production, decrease cycle times, and improve safety.
7. Industry 4.0 and Data Analytics:
Lost foam casting foundries are embracing Industry 4.0 principles, adopting data-driven decision-making through the collection and analysis of production data. Data analytics helps optimize processes, predict maintenance needs, and maximize overall efficiency.
8. Multi-Material Castings:
Advancements in casting techniques allow for the production of multi-material castings through lost foam casting. This innovation enables the creation of hybrid components with varying properties in different regions, further enhancing design possibilities.
In conclusion, innovations in lost foam casting are transforming the metal casting landscape and shaping the future of the industry. Through the integration of advanced materials, additive manufacturing, digital design, and sustainable practices, lost foam casting is becoming more versatile, efficient, and environmentally friendly. The continued development of automation, real-time monitoring, and data-driven approaches will further optimize production processes and lead to enhanced casting quality and cost-effectiveness. As technology continues to evolve, lost foam casting will remain a crucial method for manufacturing intricate and lightweight components across various industries.