Enhancing efficiency in sand casting parts production involves streamlining various processes to minimize time, cost, and resource wastage. Here are some strategies to consider for improving efficiency:
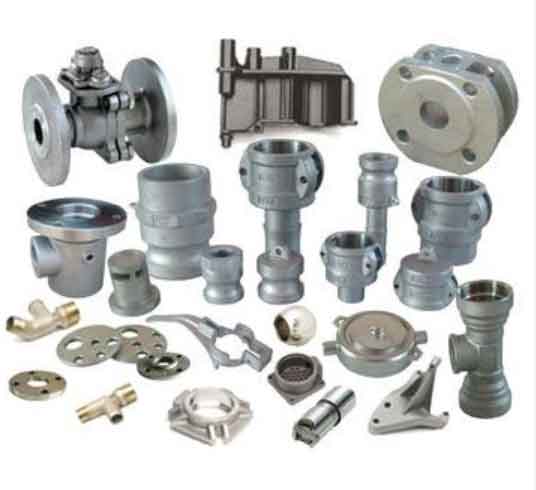
- Design optimization: Collaborate closely with design engineers to optimize part designs for manufacturability. Design for sand casting principles, such as minimizing undercuts and avoiding complex geometries, can help reduce the need for additional processes and improve overall efficiency.
- Mold and core production: Invest in high-quality molds and cores to ensure accurate and consistent casting dimensions. Utilize automated or semi-automated molding processes to improve productivity and reduce labor requirements. Implement efficient mold and core handling systems to minimize downtime between casting cycles.
- Pattern making: Employ computer-aided design and manufacturing (CAD/CAM) technologies for pattern making to enhance accuracy, speed up the process, and minimize pattern rework. Consider using additive manufacturing (3D printing) for producing patterns, which can reduce lead times and enable rapid design iterations.
- Material handling and preparation: Optimize material handling processes, such as sand mixing and conditioning, to ensure consistent and high-quality molds. Implement automated sand delivery systems and advanced sand conditioning techniques to reduce manual labor and improve consistency.
- Melting and pouring: Invest in efficient and well-maintained melting and pouring equipment to ensure accurate temperature control and minimize metal wastage. Utilize computerized systems for controlling pouring parameters to improve repeatability and reduce defects.
- Quality control: Implement robust quality control processes throughout the production cycle to detect defects early and minimize rework or scrap. Utilize advanced inspection technologies, such as non-destructive testing methods, to ensure casting integrity and reduce the need for manual inspections.
- Process automation: Explore automation opportunities within the sand casting process, such as automated mold handling, robotic pouring, and post-casting operations. Automation can increase production speed, reduce manual labor, improve consistency, and enhance overall efficiency.
- Continuous improvement: Foster a culture of continuous improvement within the organization. Encourage employees to identify and suggest process enhancements, implement lean manufacturing principles, and regularly review production workflows to identify bottlenecks and opportunities for optimization.
- Supply chain management: Optimize supply chain processes by maintaining strong relationships with suppliers and ensuring timely delivery of raw materials. Implement just-in-time inventory management practices to minimize inventory holding costs and reduce waste.
- Data analysis and monitoring: Utilize data analytics and real-time monitoring systems to track key performance indicators, identify inefficiencies, and make data-driven decisions for process optimization.
By implementing these strategies and continuously evaluating and refining production processes, manufacturers can enhance the efficiency of sand casting parts production, reduce lead times, improve productivity, and deliver high-quality castings to meet customer requirements.