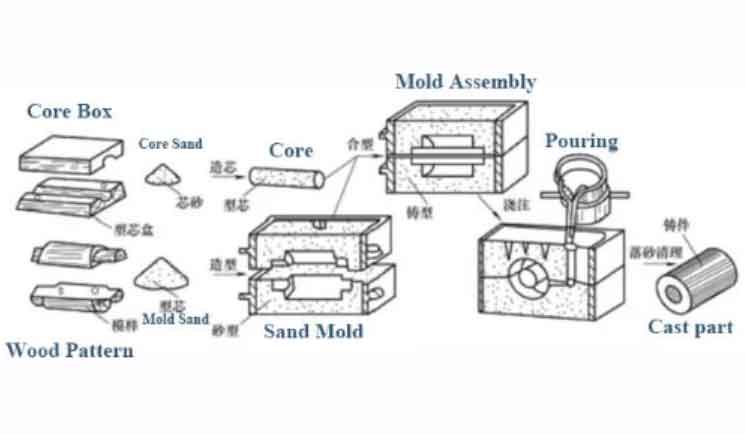
Sand casting is a widely used method for producing metal parts. It involves creating a mold made of compacted sand and pouring molten metal into it. The metal solidifies and takes the shape of the mold, resulting in the desired part. To enhance production efficiency in sand casting, there are several strategies and techniques that can be employed. Here are some key considerations:
Design for Manufacturability:
Optimize part designs to simplify the casting process. Avoid complex geometries and intricate features that may lead to difficulties during mold creation or metal flow. Incorporate fillets and radii to facilitate the removal of the part from the mold.
Mold Design and Material:
Develop efficient mold designs that minimize material waste and promote ease of use. Utilize high-quality molding sand with suitable additives and binders to enhance mold strength, surface finish, and dimensional accuracy. Consider using reusable molds for mass production to reduce material and labor costs.
Pattern Making:
Create accurate patterns or models that replicate the final part design. CNC machining, 3D printing, or manual techniques can be employed for pattern fabrication. Ensure the pattern is dimensionally stable to maintain the desired part tolerances.
Gating and Riser Design:
Optimize gating and riser systems to improve metal flow, reduce turbulence, and minimize defects like porosity and shrinkage. Well-designed gating systems promote uniform filling of the mold cavity, resulting in consistent part quality. Proper riser placement aids in providing a continuous supply of molten metal, reducing the chances of defects.
Melting and Pouring:
Optimize the melting and pouring processes to achieve efficient metal flow and minimize defects. Use appropriate melting furnaces and control systems to maintain precise temperature control. Employ methods like tilt pouring or vacuum-assisted pouring to reduce turbulence and gas entrapment.
Quality Control and Inspection:
Implement robust quality control measures throughout the casting process to detect defects early. Conduct inspections of molds, patterns, and castings to identify issues and make necessary adjustments promptly. Non-destructive testing techniques, such as X-ray or ultrasonic testing, can be employed to ensure part integrity.
Process Automation:
Explore opportunities for automation in various stages of sand casting. Automated systems for mold creation, pouring, and post-casting operations can enhance production efficiency, reduce labor costs, and improve consistency.
Material Selection:
Choose suitable casting materials based on part requirements and cost considerations. Opt for alloys that exhibit good casting properties, such as fluidity, solidification characteristics, and mechanical properties. Consult with material suppliers or metallurgical experts to determine the most appropriate alloy for your specific application.
Process Optimization:
Continuously analyze and optimize the sand casting process by collecting data, monitoring key parameters, and implementing improvements. Use techniques like simulation software to predict and optimize casting outcomes before physical production, reducing trial and error iterations.
By implementing these strategies and continuously refining the sand casting process, you can maximize efficiency, improve part quality, and increase production throughput.