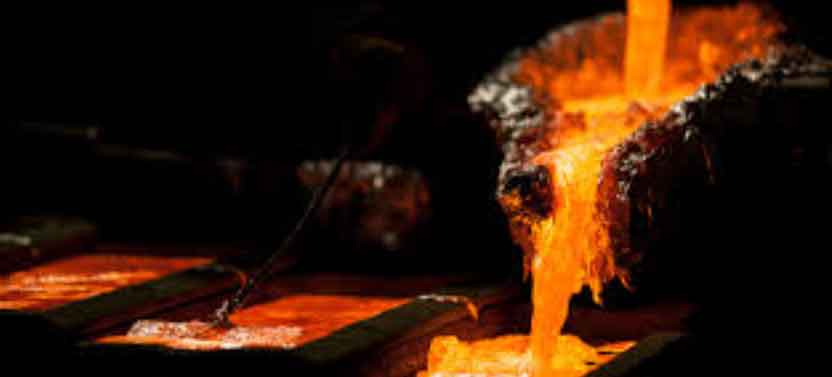
Sand casting is a widely used method for producing metal castings. It involves creating a mold from a mixture of sand and a binding agent, and then pouring molten metal into the mold cavity. To ensure precision and consistency in sand casting, several key factors need to be considered and controlled throughout the process. Here are some important aspects to focus on:
1.Mold Design and Preparation:
The mold design should be carefully engineered to accommodate shrinkage, venting, and other factors that can affect the final casting quality. Proper gating and risering systems should be incorporated to facilitate metal flow and minimize defects. Additionally, the sand mixture used for creating molds should have consistent properties, such as grain size, moisture content, and compaction.
2.Pattern and Core Making:
Patterns are used to create the mold cavities, while cores are used to create internal features. Patterns should be precisely made to the desired dimensions and surface finish. Cores should be accurately positioned and adequately supported within the mold to avoid shifting or distortion during casting.
3.Sand Control:
Consistency in sand properties is crucial for achieving quality castings. The sand mixture should be properly controlled for factors like moisture content, compactability, permeability, and compatibility with the metal being cast. Regular testing and adjustments should be performed to maintain the desired sand characteristics.
4.Melting and Metal Treatment:
The quality of the molten metal used for casting greatly influences the final product. Proper melting techniques, temperature control, and appropriate alloying elements are essential for achieving the desired mechanical and chemical properties in the castings. Metal treatment processes like degassing and refining should be carried out to remove impurities and enhance the metal quality.
5.Pouring and Solidification:
The pouring process should be controlled to ensure a consistent flow of molten metal into the mold cavity. Proper gating and risering systems should be designed to minimize turbulence, avoid entrapped gases, and promote directional solidification. Monitoring and controlling the cooling rate during solidification can help prevent defects like shrinkage, porosity, and hot tears.
6.Shakeout and Cleaning:
After solidification, the castings are removed from the mold through a shakeout process. Care should be taken to prevent damage or distortion during this stage. The castings should then be properly cleaned to remove any residual sand or other contaminants. Shot blasting, grinding, or other cleaning methods can be employed as necessary.
7.Inspection and Quality Control:
Regular inspection throughout the casting process is essential to identify and rectify any issues promptly. Various non-destructive testing techniques, such as visual inspection, radiography, ultrasonic testing, or magnetic particle inspection, can be employed to detect defects. Dimensional inspections, mechanical testing, and metallurgical analysis should also be conducted to ensure compliance with the required specifications and standards.
8.Documentation and Traceability:
Keeping detailed records of the entire sand casting process is important for traceability and quality assurance. This includes documenting the materials used, process parameters, inspection results, and any deviations or corrective actions taken. Such records can help identify trends, improve process efficiency, and ensure consistent quality in future casting productions.
By paying close attention to these aspects and implementing stringent quality control measures, sand casting can consistently produce precise and high-quality metal castings. Regular process monitoring, continuous improvement initiatives, and a commitment to excellence are vital for achieving the desired level of precision and consistency in sand casting operations.