Ductile iron casting, also known as nodular iron casting or spheroidal graphite iron casting, possesses a unique set of properties that make it well-suited for a wide range of engineering applications. Let’s explore the key properties of ductile iron casting:
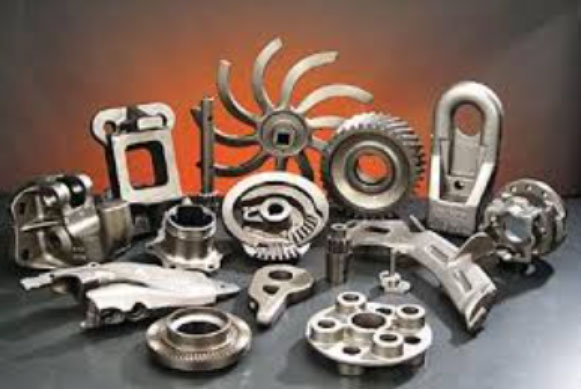
1. Strength and Toughness: Ductile iron casting exhibits excellent strength and toughness, making it capable of withstanding high loads and impacts. It has a higher tensile strength and yield strength compared to grey cast iron, allowing it to handle heavy-duty applications and resist deformation or breakage under load.
2. Ductility and Flexibility: Unlike other cast irons, ductile iron has high ductility, meaning it can undergo significant plastic deformation before fracturing. This property allows for easy forming, bending, and shaping of components, making it versatile and adaptable to various engineering designs and requirements.
3. Impact Resistance: Ductile iron casting offers exceptional impact resistance, thanks to its nodular graphite structure. It can absorb and dissipate energy when subjected to sudden shocks or impacts, making it suitable for applications where components may experience dynamic or repetitive loading.
4. Corrosion Resistance: Ductile iron exhibits good corrosion resistance, particularly in environments where it is exposed to water, chemicals, or other corrosive substances. However, it may require protective coatings or surface treatments for enhanced corrosion resistance in more aggressive environments.
5. Wear Resistance: Ductile iron casting demonstrates excellent wear resistance, making it suitable for applications that involve sliding or abrasive wear. It can withstand the abrasive action of particles, providing longer service life and reduced maintenance requirements in components exposed to wear, such as pumps, valves, and machinery parts.
6. Machinability: Ductile iron is known for its good machinability, enabling ease of machining and fabrication. It can be cut, drilled, threaded, and shaped using standard machining tools and techniques, allowing for efficient production of complex components and precise tolerances.
7. Heat Resistance: Ductile iron exhibits good heat resistance, enabling it to maintain its structural integrity and mechanical properties at elevated temperatures. It can withstand thermal cycling and operate in high-temperature environments without significant loss of strength or dimensional stability.
8. Sound and Vibration Damping: Ductile iron has inherent sound and vibration damping properties. It can absorb and dissipate vibrations, reducing noise levels and enhancing the overall performance and comfort of machinery and equipment.
9. Cost-Effectiveness: Ductile iron casting offers a cost-effective solution for many engineering applications. It has a lower material cost compared to some alternative materials, such as steel, while still providing comparable strength, durability, and performance. Additionally, its long service life and low maintenance requirements contribute to cost savings over time.
Ductile iron casting’s combination of strength, toughness, ductility, impact resistance, and other favorable properties make it a preferred choice in various engineering applications. It is widely used in industries such as automotive, machinery, construction, infrastructure, and power generation, where reliable and durable components are essential for efficient and safe operation.