1. Effect of cooling rate on microstructure
Figure 1 shows the microstructure of the coarse-grained zone in steel castings produced by sand casting manufacturers at different cooling rates. When sand casting manufacturers produce steel castings with a cooling rate of 0 At 2, 0.5, 1, and 5 ℃/s, the transformation products are mainly ferrite, pearlite, and strip like bainite. Sand casting manufacturers produce steel castings with a cooling rate of 0 At 2 ℃/s, there is a large amount of plate-like ferrite and a small amount of plate-like bainite and pearlite in the tissue, and the size of plate-like bainite is relatively small; Increase the cooling speed to 0 At 5 ℃/s, the content of strip like bainite significantly increases, and it is surrounded by pre eutectoid ferrite at grain boundaries. As the cooling rate increases, ferrite and pearlite gradually decrease, while strip like bainite gradually increases and grows into the grains. The orientation of strip like bainite within each grain is different. When the cooling rate of steel castings produced by sand casting manufacturers is 5 ℃/s, an increase in undercooling will cause an increase in the nucleation points of strip like bainite, so the strip like bainite at this time is denser than that at low cooling rates. Within this cooling rate range, the decrease in ferrite and pearlite is mainly due to the diffusion type phase transition of both ferrite and pearlite. Atomic diffusion is gradually suppressed with the increase of cooling rate, making their transformation gradually difficult, while bainite transformation is promoted. In addition, within the cooling rate range of steel castings produced by sand casting manufacturers, the content of pearlite is always relatively low. This is mainly because the base material contains more strong carbides such as Cr and Mo, which inhibit the nucleation and growth of pearlite; Mo is the element with the strongest inhibition of pearlite transformation, but it has little effect on ferrite and bainite.
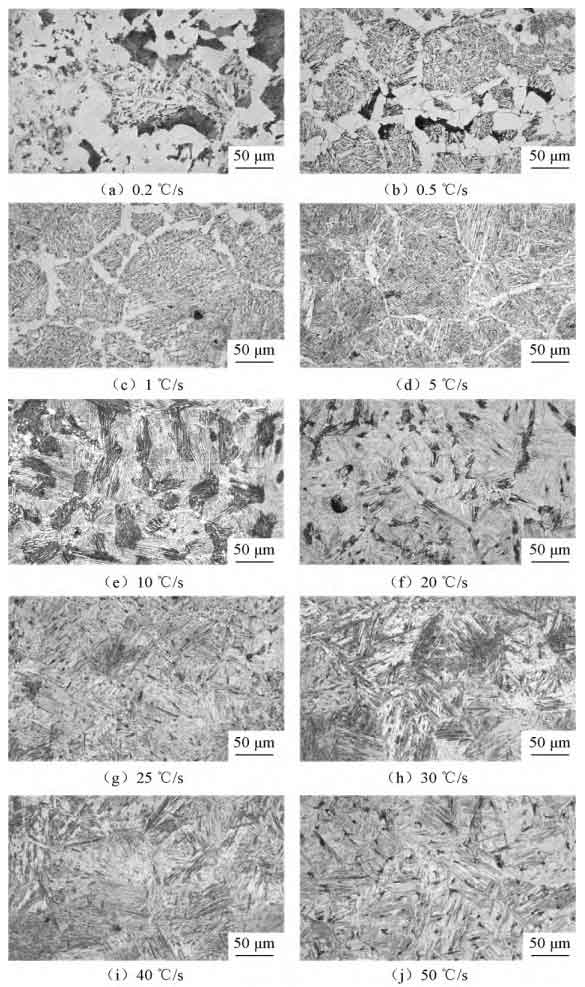
When the cooling rate of steel castings produced by sand casting manufacturers is 10 ℃/s, as shown in Figure 1e, there are more Flat noodles martensite and lath bainite in the structure; When the cooling rate is 20~50 ℃/s, the structure is as shown in Fig. 1f~1j. At this time, the cooling rate of steel castings produced by sand casting manufacturers is fast. Due to the role of alloy elements, the hardenability of the steel is enhanced, and the diffusion transformation stops. At this time, the structure is mainly Flat noodles martensite and acicular martensite. In addition, as the cooling rate of steel castings produced by sand casting manufacturers increases, the Flat noodles martensite tends to decrease, and the acicular martensite tends to increase. At the same time, the Flat noodles group diameter and the beam width in the same direction of Flat noodles martensite decrease, so increasing the cooling rate can play a role in refining the Flat noodles martensite structure. The main reason is that as the cooling rate of steel castings produced by sand casting manufacturers continues to increase, the degree of supercooling gradually increases, The diffusion ability of atoms is limited.
C | Mn | Si | P | S | Cr | Ni | Mo | Cu | V | W |
0.23 | 0.63 | 0.51 | 0.01 | 0.011 | 0.49 | 0.54 | 0.24 | 0.08 | 0.01 | 0.01 |
2. Effect of cooling rate on Vickers hardness
Table 2 shows the Vickers hardness values of steel castings produced by sand casting manufacturers at different cooling rates. Figure 2 shows the effect of cooling rate on hardness of steel castings produced by sand casting manufacturers.
Cooling rate/(℃ · s^-1) | Vickers hardness HV | Average Vickers hardness HV |
0.2 | 203 197 201 | 200 |
0.5 | 220 223 219 | 221 |
1 | 238 241 236 | 238 |
5 | 266 281 273 | 273 |
10 | 313 310 300 | 308 |
20 | 417 406 420 | 414 |
25 | 416 414 413 | 414 |
30 | 450 487 484 | 473 |
40 | 474 450 479 | 468 |
50 | 484 470 455 | 470 |
The cooling rate of steel castings produced by sand casting manufacturers is 0 At 2 ℃/s, the hardness values of flaky ferrite, pearlite, and a small amount of strip like bainite are lower, with an average Vickers hardness of only HV200; With the increase of cooling rate, the amount of strip like bainite increases, and the hardness value increases. At a cooling rate of 5 ℃/s, the content of strip like bainite is the highest, and the hardness also increases significantly. The average Vickers hardness reaches HV273; When the cooling rate is greater than 10 ℃/s, the structure is mainly composed of Flat noodles martensite and acicular martensite. Due to the high hardness and strength of martensite, the Vickers hardness is significantly increased, and the highest average Vickers hardness reaches HV473. From this, it can be seen that sand casting manufacturers produce steel castings with severe hardening. When the cooling rate is high, it is easy to cause severe embrittlement in the heat affected zone and cold cracks. Therefore, in welding applications, small wire energy should be used, and process measures such as preheating before welding and slow cooling after welding should be adopted.
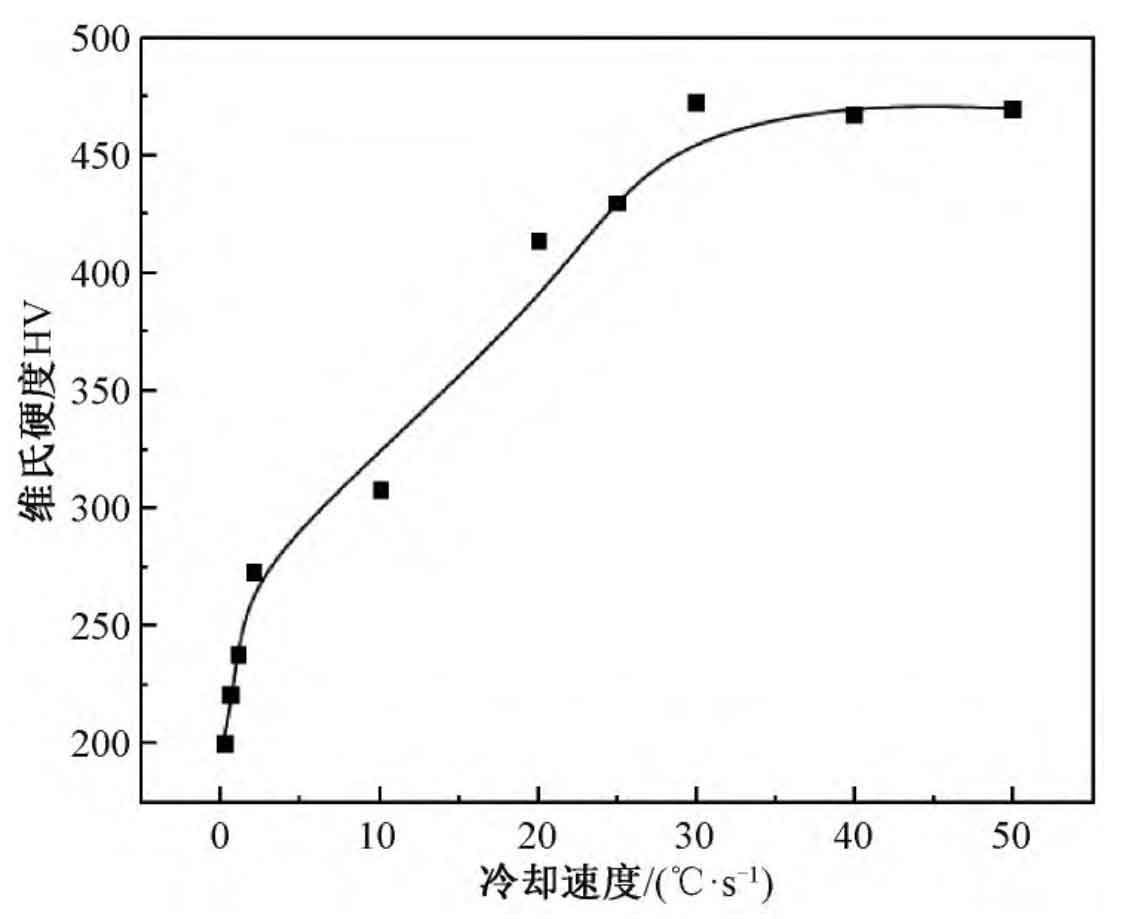
3. CCT curve
According to the thermal expansion curves of steel castings produced by sand casting manufacturers at different cooling rates, the phase transition temperatures of steel castings produced by sand casting manufacturers at different cooling rates are shown in Table 3. Combined with the metallographic structure mentioned earlier, the CCT curve in Figure 3 is obtained. The critical point of phase transition after thermal deformation is Ac1=747 ℃, Ac3=875 ℃, and Ms=422 ℃. From the CCT curve, it can be seen that the phase transformation products of undercooled austenite mainly include ferrite, pearlite, bainite, and martensite.
Cold speed/(°C^-1) | Fs/°C | Ps/°C | Bs/°C | Bf/°C | Ms/°C |
0.2 | 747 | 684 | 649 | 600 | — |
0.5 | 732 | 676 | 595 | 496 | — |
1 | 719 | 673 | 600 | 497 | — |
5 | 710 | 668 | 644 | 526 | — |
10 | — | — | 555 | 465 | 380 |
20 | — | — | — | — | 406 |
25 | — | — | — | — | 406 |
30 | — | — | — | — | 415 |
50 | — | — | — | — | 416 |
50 | — | — | — | — | 422 |
The cooling rate of steel castings produced by sand casting manufacturers is 0 At 2-5 ℃/s, the cooling rate is relatively slow, and the generated microstructure is mainly plate-like ferrite, pearlite, and strip like bainite. The transformation temperature of plate-like ferrite also varies with the different cooling rates. This is because ferrite transformation belongs to diffusion type transformation. The increase in cooling rate in sand casting manufacturers makes it difficult for atomic diffusion in steel castings. If phase transformation occurs, the degree of undercooling must be increased, This leads to a decrease in the temperature of the ferrite transformation phase transition point, and the phase transition zone expands towards the low-temperature zone.
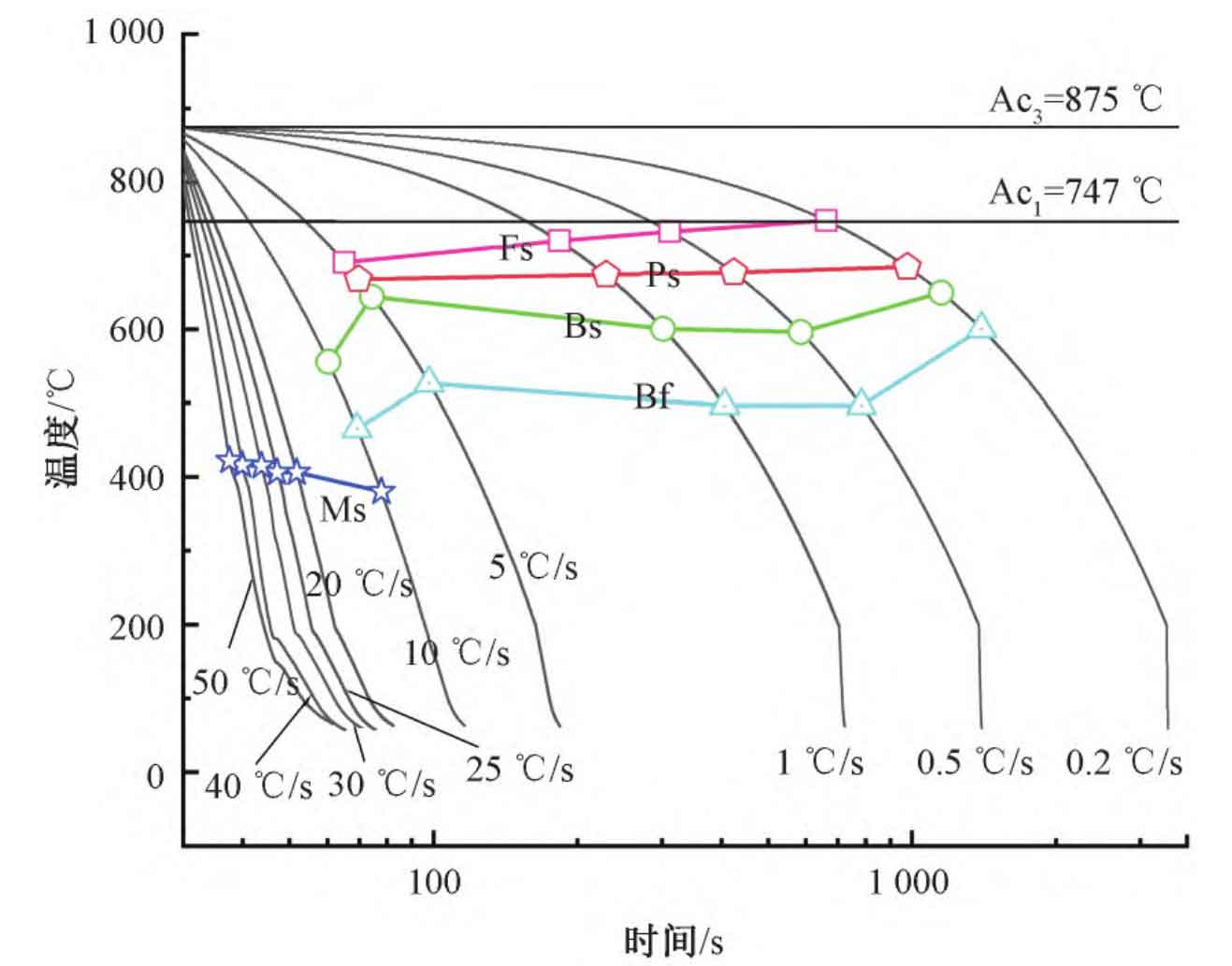
When the cooling rate is 10 ℃/s, the cooling rate of steel castings produced by sand casting manufacturers is faster, and the microstructure generated is mainly lamellar bainite and Flat noodles martensite; When the cooling rate is 20~50 ℃/s, the cooling rate of steel castings produced by sand casting manufacturers is faster, and the generated structures are mainly Flat noodles martensite and acicular martensite. With the increase of cooling rate, the martensitic transformation temperature shows a slight increase trend. This is mainly because when the cooling rate of sand casting manufacturers produces steel castings is low, the bainite transformation and the precipitation of pre eutectoid ferrite cause the enrichment of surrounding carbon, resulting in a decrease in martensitic transformation temperature.