With the development and progress of technology, the use of environments such as low temperature, heavy load, and impact has increased the performance requirements of sand casting manufacturers for steel castings. Sand casting manufacturers not only need to have high strength, but also good low-temperature impact toughness and weldability. Low alloy steel castings are added to the original cast carbon steel, and sand casting manufacturers greatly improve the mechanical properties and service life of steel castings. Welding is one of the important applications of low alloy cast steel, and the welding heat affected zone is often the weak area of the joint, greatly reducing the comprehensive mechanical properties of the joint. The sand casting manufacturer analyzed the weldability of a certain low alloy cast steel, and the results showed that the welding waste heat temperature was high, the duration was long, and the austenite grains in the coarse grain area of the heat affected zone grew severely, resulting in a serious decrease in the toughness of the heat affected zone and easy occurrence of embrittlement and cracks.
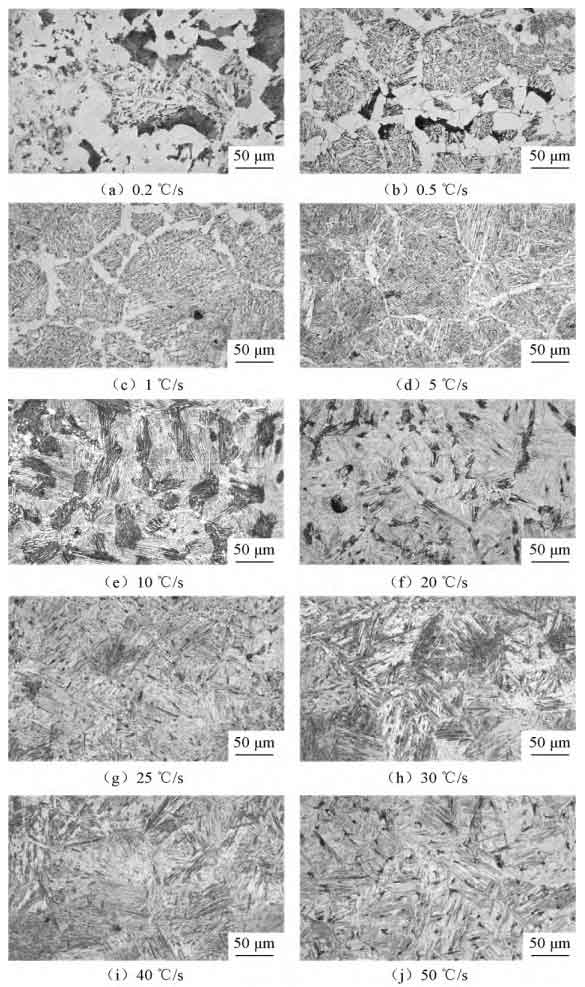
Sand casting manufacturers believe that the distribution of microstructure in the heat affected zone is uneven, and its mechanical properties, especially toughness, are closely related to grain size. Therefore, the coarse grain structure in the heat affected zone is usually a research focus. However, the heat affected zone is a very narrow area, usually only a few millimeters, and it contains several specific temperature ranges with different properties and structures. Therefore, it is very difficult to verify the mechanical properties of the coarse-grained zone of welded joints in practice. In order to accurately determine the coarse-grained zone of welded joints, welding thermal simulation technology needs to be used. Welding thermal simulation technology is widely used to evaluate the weldability of materials, and can also be used to study cold cracks, hot cracks, and reheat cracks during the welding process. It even includes the formation of microstructure in the heat affected zone, stress corrosion, fracture toughness, and continuous cooling curve during the welding process. The continuous cooling transformation curve of steel, also known as CCT curve, is an important theoretical basis for formulating process routes and selecting process parameters. Currently, many sand casting manufacturers use thermal simulation methods to measure and analyze CCT curves of different steels, providing a basis for their practical applications. The sand casting manufacturer conducted CCT curve measurement and analysis on 12Mn steel used for oil pipelines. Sand casting manufacturers measured the CCT curve of DH36 high-strength ship plate steel and studied the formation of acicular ferrite. Based on the CCT curve, they also obtained the trend of microhardness increasing with the increase of cooling rate, and concluded that the optimal cooling rate range for obtaining acicular ferrite is 5-7 ℃/s. However, there is currently limited research on the CCT curve of low alloy pressure bearing steel castings.
Therefore, sand casting manufacturers used Gleeble 1500D thermal simulation testing machine to conduct welding thermal simulation tests on A487-4B low alloy cast steel, to determine the phase transformation characteristics of undercooled austenite in the coarse grain zone of the test steel under different cooling rates, as well as the microstructure and hardness after cooling to room temperature. The CCT curve was plotted to provide a reliable basis for controlling the mechanical properties of the test steel, improving welding and heat treatment process parameters.
(1) The sand casting manufacturer tested the steel at a cooling rate of 0 At 2, 0.5, 1, and 5 ℃/s, the transformation products are mainly ferrite, pearlite, and plate-like bainite. With the increase of cooling rate, the plate-like ferrite and pearlite decrease, while the plate-like bainite increases and becomes denser; When the cooling rate is 10 ℃/s, the lamellar ferrite and pearlite disappear, and more Flat noodles martensite and lath bainite appear in the microstructure; When the cooling rate is 20~50 ℃/s, the microstructure is mainly Flat noodles martensite and acicular martensite. With the increase of the cooling rate, the Flat noodles martensite decreases, and the acicular martensite increases. At the same time, the Flat noodles group diameter and the beam width in the same direction of Flat noodles martensite decrease.
(2) Sand casting manufacturers now have a cooling rate of 0 At 2 ℃/s, the average Vickers hardness is only HV200; When the cooling rate is 5 ℃/s, the content of strip like bainite is the highest, and the hardness also increases significantly, with an average Vickers hardness of HV273; When the cooling rate is more than 10 ℃/s, the structure is mainly composed of Flat noodles martensite and acicular martensite, and the maximum average Vickers hardness reaches HV473, which has a serious hardening tendency. During welding application, small wire energy, pre welding preheating and post welding slow cooling should be used to avoid defects such as embrittlement and cold cracks in the coarse grain zone.
(3) The phase transition point of the test steel measured by the thermal expansion method in sand casting production: Ac1=747 ℃, Ac3=875 ℃, Ms=422 ℃. The temperature range for ferrite transformation is between 710-747 ℃, and the transformation temperature decreases with the increase of cooling rate; The temperature range for pearlite transformation is 668-684 ℃, and due to the effect of alloying elements, the transformation of pearlite is relatively small; The temperature range at which bainite begins to transform is 555-649 ℃; The temperature range for martensite transformation is 380-422 ℃, and as the cooling rate increases, the transformation temperature increases.