The future of ductile iron casting is poised for transformative changes, driven by emerging technologies and process enhancements. These advancements aim to increase efficiency, reduce environmental impact, and enhance the properties of the final products. Here’s an exploration into what the future may hold:
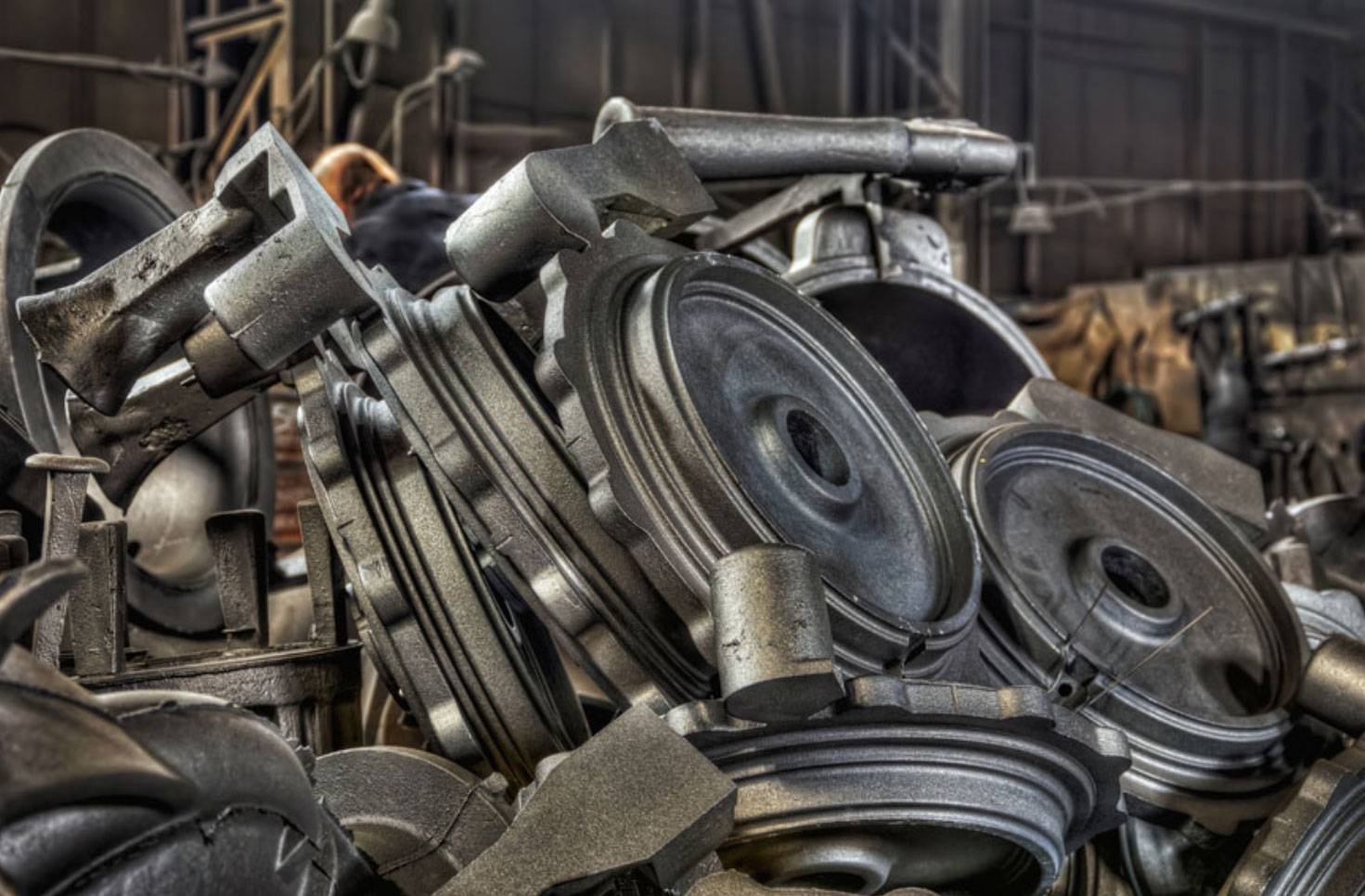
1. Digital Integration and Smart Foundries
- Industry 4.0 Technologies: Incorporation of IoT (Internet of Things), AI (Artificial Intelligence), and machine learning for real-time monitoring and control of casting processes.
- Predictive Maintenance: Using data analytics for predictive maintenance of equipment to reduce downtime and increase efficiency.
2. Advanced Materials Research
- New Alloy Development: Experimentation with new alloying elements to create ductile iron with superior properties like higher strength, better wear resistance, and improved corrosion resistance.
- Nano-technology: Integrating nano-materials to modify the microstructure of ductile iron, enhancing its mechanical and physical properties.
3. Enhanced Molding and Casting Techniques
- 3D Printing for Molds and Cores: Further adoption of 3D printing to create more complex and precise molds, reducing waste and speeding up the production process.
- Automated Molding Lines: Advancements in automation for molding processes to improve precision and consistency in casting.
4. Environmental Sustainability
- Energy-efficient Furnaces: Development of more energy-efficient melting technologies to reduce carbon footprint.
- Recycling Initiatives: Enhanced methods for recycling scrap metal and foundry sand, aiming for more sustainable production cycles.
- Emission Control: Implementation of stricter emission control technologies to minimize environmental pollution.
5. Process Optimization through Simulation
- Advanced Computer Simulations: Utilizing sophisticated software to simulate and optimize the casting process, reducing trial and error and improving quality.
- Virtual Prototyping: Creating digital twins of casting processes to test and refine different scenarios without physical trials.
6. Quality Control Innovations
- Automated Inspection Systems: Employing advanced robotic and imaging technologies for non-destructive testing of castings.
- In-line Quality Monitoring: Real-time monitoring of casting parameters to ensure consistent quality and immediate correction of process deviations.
7. Customization and Flexibility
- Small-batch Production: Adapting processes to efficiently handle small-batch, customized production runs without sacrificing quality or cost-effectiveness.
- Flexible Manufacturing Systems: Developing flexible systems that can easily adapt to changing product designs and specifications.
8. Heat Treatment Advancements
- Targeted Heat Treatments: New techniques for localized heat treatment to achieve specific properties in different regions of a single casting.
- Rapid Cooling Methods: Exploring rapid cooling technologies post-heat treatment to enhance certain mechanical properties.
9. Collaborations and Partnerships
- Academic-Industry Collaboration: Strengthening ties between foundries and academic institutions for research and development.
- Global Standardization: Working towards global standards in ductile iron casting processes and materials for consistency and quality across borders.
10. Addressing Skilled Labor Shortage
- Training and Education: Focusing on training programs and apprenticeships to equip the new generation with the necessary skills for advanced casting techniques.
- Attracting Talent: Initiating programs to attract young talent to the foundry industry, highlighting technological advancements and innovation opportunities.
The future of ductile iron casting is dynamic and evolving, with a strong emphasis on technological integration, environmental sustainability, and material advancements. These innovations not only aim to improve the efficiency and quality of the casting process but also seek to meet the growing demands for more sustainable and high-performance materials in various industries.