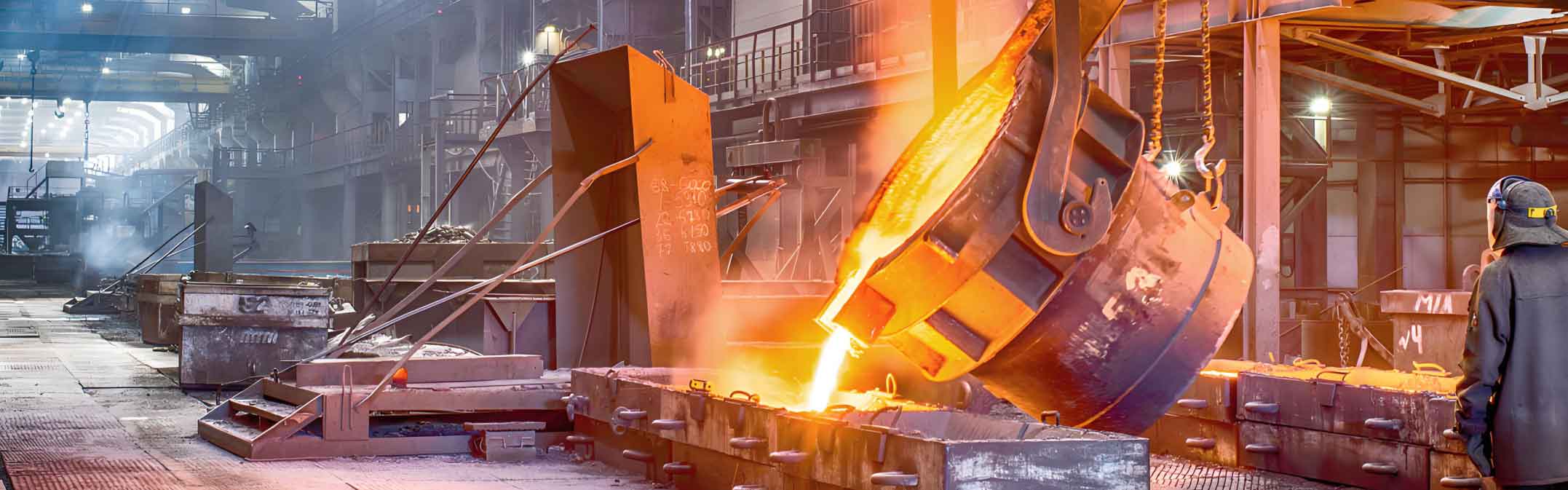
Casting is a fundamental manufacturing process used to create complex metal components by pouring molten metal into molds. Two widely used casting techniques are lost foam casting and sand casting. Both methods have distinct processes, advantages, disadvantages, and applications. This article provides a comprehensive comparative analysis of lost foam casting and sand casting, highlighting their respective features, benefits, and limitations.
Lost Foam Casting
Lost foam casting is a modern and innovative casting technique that uses a foam pattern to create metal components. The foam pattern is coated with a refractory material and placed in a sand mold. When molten metal is poured into the mold, the foam pattern vaporizes, leaving behind a metal casting that replicates the original foam pattern.
Process of Lost Foam Casting
- Foam Pattern Creation:
- A foam model is created using polystyrene foam, either by machining or molding.
- Pattern Assembly:
- The foam pattern is assembled with a gating system if needed.
- Coating:
- The foam pattern is coated with a refractory material to form a thin shell.
- Mold Preparation:
- The coated foam pattern is placed in a sand mold, and sand is packed around it.
- Metal Pouring:
- Molten metal is poured into the mold, causing the foam pattern to vaporize and be replaced by the metal.
- Mold Breakout:
- Once the metal has solidified, the sand mold is broken away to reveal the metal casting.
- Finishing:
- The casting is cleaned, and any excess material is removed to achieve the final product.
Advantages of Lost Foam Casting
- Cost-Effective: Lower tooling costs and reduced labor requirements.
- Simplified Process: Eliminates the need for core making and wax removal steps.
- Flexibility in Design: Allows for complex shapes and thin-walled sections.
- Environmental Benefits: Reduces waste and emissions compared to traditional casting methods.
Disadvantages of Lost Foam Casting
- Surface Finish: May produce rougher surfaces compared to other casting methods.
- Pattern Fragility: Foam patterns can be delicate and prone to damage.
- Material Limitations: Less suitable for certain high-temperature alloys.
- Dimensional Accuracy: Can be less precise than other casting methods.
Applications of Lost Foam Casting
- Automotive: Production of engine blocks, cylinder heads, and other complex components.
- Marine: Manufacturing of propellers and other intricate parts.
- Industrial Machinery: Creating components with complex geometries.
- Consumer Goods: Producing decorative items and hardware.
Advantages of Lost Foam Casting | Disadvantages of Lost Foam Casting |
---|---|
Cost-effective | Rougher surface finish |
Simplified process | Fragility of foam patterns |
Flexibility in design | Material limitations |
Environmental benefits | Less precise dimensional accuracy |
Sand Casting
Sand casting is one of the oldest and most widely used casting techniques. It involves creating a mold from a sand mixture and pouring molten metal into the cavity formed by the pattern. The sand mold is then broken away to reveal the metal casting.
Process of Sand Casting
- Pattern Creation:
- A pattern of the desired component is created using wood, metal, or plastic.
- Mold Preparation:
- The pattern is placed in a sand mold, and sand is packed around it to create the mold cavity.
- Core Making (if needed):
- Cores are made from sand and placed in the mold to create internal features in the casting.
- Mold Assembly:
- The mold is assembled, and the pattern is removed, leaving a cavity in the shape of the component.
- Metal Pouring:
- Molten metal is poured into the mold cavity.
- Cooling:
- The metal is allowed to cool and solidify.
- Mold Breakout:
- The sand mold is broken away to reveal the metal casting.
- Finishing:
- The casting is cleaned, and any excess material is removed to achieve the final product.
Advantages of Sand Casting
- Versatility: Suitable for a wide range of metals and alloys.
- Cost-Effective for Large Parts: Economical for producing large and heavy components.
- Design Flexibility: Allows for a wide range of shapes and sizes.
- Reusability of Sand: Sand can be recycled and reused multiple times.
Disadvantages of Sand Casting
- Surface Finish: Typically produces a rough surface that requires additional finishing.
- Dimensional Accuracy: Less precise than other casting methods, leading to potential variations in dimensions.
- Complexity of Cores: Creating and placing cores can be labor-intensive and time-consuming.
- Environmental Impact: Disposal of used sand can be environmentally challenging.
Applications of Sand Casting
- Automotive: Production of engine blocks, transmission housings, and other large components.
- Aerospace: Manufacturing of large structural components.
- Construction: Creating parts for heavy machinery and equipment.
- Industrial Equipment: Producing large and durable parts for various industrial applications.
Advantages of Sand Casting | Disadvantages of Sand Casting |
---|---|
Versatility | Rough surface finish |
Cost-effective for large parts | Less precise dimensional accuracy |
Design flexibility | Complexity of cores |
Reusability of sand | Environmental impact |
Comparative Analysis
Process Complexity
- Lost Foam Casting: Simplified process with fewer steps, as it eliminates the need for core making and wax removal. The foam pattern vaporizes, simplifying mold preparation and reducing labor.
- Sand Casting: More complex due to the need for pattern creation, core making, and precise mold assembly. Requires more labor and time, especially for intricate designs.
Precision and Surface Finish
- Lost Foam Casting: Provides good flexibility in design but may result in rougher surfaces and less precise dimensional accuracy compared to other casting methods.
- Sand Casting: Typically produces rougher surfaces that require additional finishing. Dimensional accuracy can vary, leading to potential deviations in the final product.
Cost and Efficiency
- Lost Foam Casting: Generally more cost-effective for complex and intricate components due to lower tooling and labor costs. The process is faster and suitable for smaller to medium-sized parts.
- Sand Casting: More economical for large and heavy components, but can be labor-intensive and time-consuming, especially for parts with complex geometries.
Material and Design Flexibility
- Lost Foam Casting: Allows for complex shapes and thin-walled sections, but is less suitable for high-temperature alloys.
- Sand Casting: Highly versatile, accommodating a wide range of metals and alloys. Suitable for producing large and heavy parts with varied shapes and sizes.
Environmental Impact
- Lost Foam Casting: Environmentally friendly, with reduced waste and emissions. The foam patterns vaporize during the process, leaving minimal residues.
- Sand Casting: Disposal of used sand can pose environmental challenges, but sand can be recycled and reused multiple times, reducing overall waste.
Aspect | Lost Foam Casting | Sand Casting |
---|---|---|
Process Complexity | Simplified process | More complex, labor-intensive |
Precision and Surface Finish | Good flexibility, rougher surface finish | Rough surface finish, variable accuracy |
Cost and Efficiency | Cost-effective for intricate components | Economical for large parts, labor-intensive |
Material and Design Flexibility | Allows complex shapes, less suitable for high-temp alloys | Versatile, suitable for large and heavy parts |
Environmental Impact | Reduced waste and emissions | Sand recycling reduces waste, disposal challenges |
Conclusion
Both lost foam casting and sand casting offer unique advantages and are suited to different applications based on their respective processes, precision, cost, and environmental impact. Lost foam casting is ideal for producing complex and intricate components with good design flexibility, making it suitable for automotive, marine, and industrial machinery applications. Sand casting, on the other hand, is more economical for large and heavy parts, with a wide range of metals and alloys, commonly used in automotive, aerospace, construction, and industrial equipment sectors.
Understanding the strengths and limitations of each technique allows manufacturers to choose the most appropriate casting method for their specific needs, ensuring optimal performance and efficiency in their production processes.