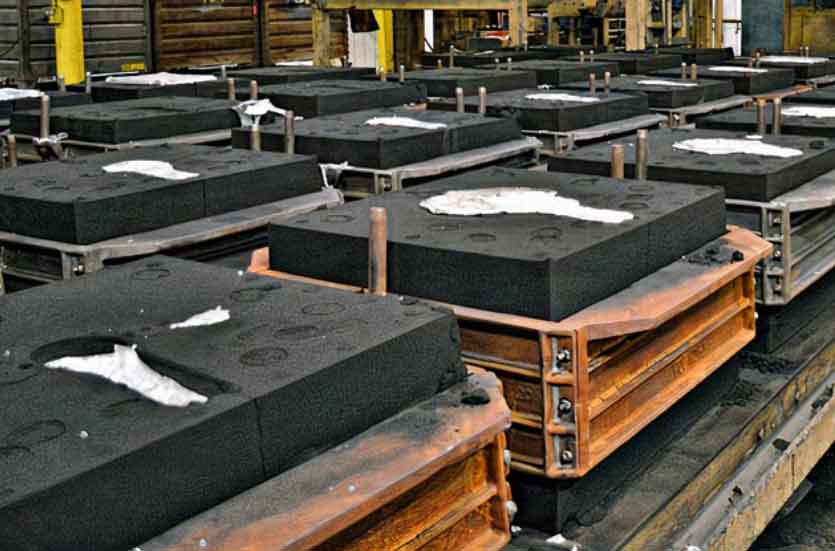
Additives play a significant role in enhancing the performance of resin sand casting by improving mold properties, reducing defects, and optimizing the casting process. These additives are mixed with the sand and resin binder to impart specific characteristics and functionalities to the molds. Let’s explore some common additives and their roles in enhancing resin sand casting performance:
- Catalysts: Catalysts are additives that accelerate the curing process of the resin binder. They help to reduce curing time, improve mold strength, and increase productivity by shortening the time required for the sand molds to set and solidify.
- Hardeners: Hardeners are additives used in combination with resin binders to increase the overall strength and durability of the molds. They contribute to better mold stability during handling and pouring.
- Release Agents: Release agents are applied to the pattern surface to facilitate easy pattern removal from the mold without damaging the mold cavity. They prevent the pattern from sticking to the sand and resin, ensuring a smooth release.
- Anti-veining Agents: These additives reduce the occurrence of veining defects in the casting, which are caused by the penetration of metal into the mold cavities. Anti-veining agents create a barrier that minimizes metal penetration and ensures a cleaner casting surface.
- Flow Aids: Flow aids are used to improve the flowability and moldability of the sand-resin mixture, especially in complex molds with intricate shapes. They help ensure even and uniform sand distribution around the pattern.
- Anti-scabbing Agents: These additives prevent scab defects, which occur when the resin binder on the mold surface reacts with the molten metal, resulting in surface imperfections on the casting.
- Anti-oxidants: Anti-oxidants are used to minimize oxidation of the molten metal during pouring, which can lead to the formation of defects like metal inclusions and porosity in the castings.
- Fillers: Fillers are added to the resin-sand mixture to modify the properties of the molds. Common fillers include silica flour, zircon flour, and ceramic materials, which can enhance mold strength, thermal stability, and surface finish.
- Graphite: Graphite is sometimes used as an additive to improve the mold’s thermal conductivity, allowing for better heat dissipation during casting.
- Binders with Different Properties: By blending different types of resin binders, such as furan and urethane, manufacturers can tailor the mold’s properties to suit specific casting requirements, combining the advantages of each binder type.
By carefully selecting and using additives in resin sand casting, manufacturers can optimize mold performance, reduce defects, and improve overall casting quality. It is essential to consider the specific casting requirements and tailor the additive selection accordingly. Proper control and understanding of the additive’s effects ensure the best results in resin sand casting processes.