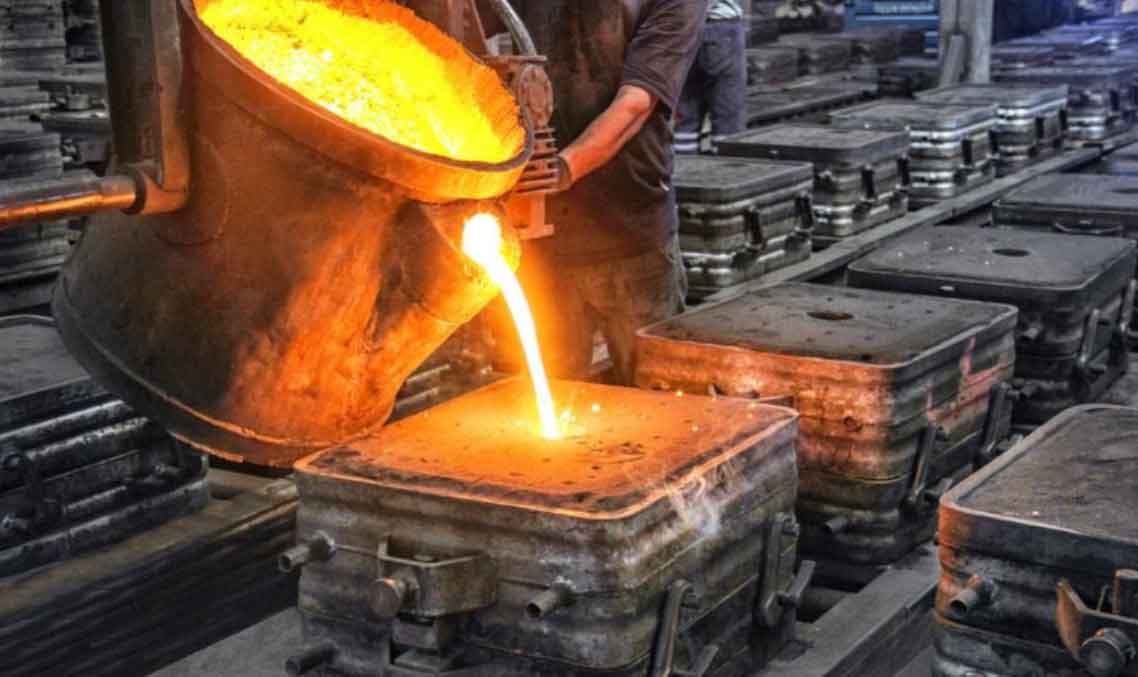
Sustainable practices in sand casting manufacturing aim to balance efficiency and environmental impact by minimizing resource consumption, reducing waste generation, and adopting eco-friendly technologies. By implementing sustainable practices, foundries can contribute to environmental preservation while remaining economically viable. Here are some key sustainable practices in sand casting manufacturing:
1. Material Recycling and Reclamation:
- Implementing systems for recycling and reusing sand and molding materials reduces the need for fresh resources and minimizes waste generation. Sand reclamation systems and recycling programs are essential components of sustainable sand casting.
2. Eco-Friendly Binders and Additives:
- Traditional chemical binders used in sand casting can have environmental impacts. Switching to eco-friendly binders and additives, such as water-based or organic binders, can help reduce emissions and improve the environmental footprint of the casting process.
3. Energy Efficiency:
- Foundries can optimize their energy consumption through measures such as energy-efficient equipment, process automation, and better process control. Reducing energy consumption not only lowers costs but also reduces the overall environmental impact.
4. Waste Reduction and Management:
- Minimizing waste generation and adopting proper waste management practices, including recycling and responsible disposal, are crucial for sustainable sand casting manufacturing.
5. Sustainable Packaging:
- Using eco-friendly and recyclable packaging materials for shipping and transportation of castings helps reduce the environmental impact of the entire supply chain.
6. Environmental Compliance:
- Ensuring compliance with environmental regulations and obtaining necessary permits demonstrates the foundry’s commitment to environmental responsibility.
7. Green Sand Additives:
- Opting for green sand additives that have minimal environmental impact, such as organic or biodegradable additives, contributes to sustainability in sand casting.
8. Green Sand Stabilization:
- Foundries can explore methods for green sand stabilization, which reduces the release of emissions during mold preparation and casting.
9. Water Conservation:
- Implementing water-saving practices and water recycling systems helps conserve this valuable resource in sand casting operations.
10. Investment in Green Technologies:
- Investing in cleaner technologies, such as electric induction melting furnaces or energy-efficient equipment, can significantly reduce the carbon footprint of the casting process.
11. Sustainable Supplier Selection:
- Collaborating with suppliers that follow sustainable practices, use eco-friendly materials, and prioritize environmental responsibility contributes to an overall sustainable supply chain.
12. Environmental Training and Awareness:
- Educating employees about the importance of sustainability and their role in reducing the environmental impact of sand casting operations fosters a culture of environmental responsibility within the foundry.
By implementing these sustainable practices, sand casting manufacturers can strike a balance between efficiency and environmental impact, ensuring long-term viability while minimizing their contribution to environmental degradation. Embracing sustainability not only benefits the planet but can also lead to cost savings, increased competitiveness, and improved reputation in the market.