The sand casting process involves several steps and techniques to produce metal components. Here is a breakdown of the main steps involved in sand casting:
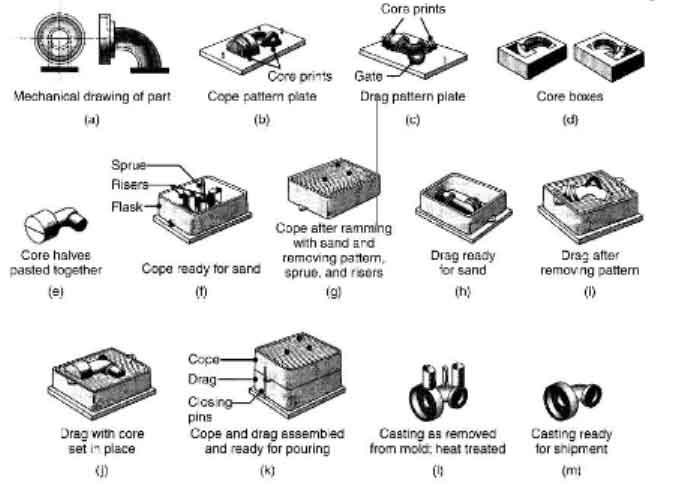
- Pattern Creation: A pattern is created, which is a replica of the desired metal component. The pattern is typically made from wood, plastic, or metal and includes the shape and features of the final part.
- Pattern Assembly: The pattern may consist of multiple pieces, especially for complex components. These pieces are assembled to form the complete pattern, ensuring proper alignment and fit.
- Mold Box Preparation: A mold box, also known as a flask, is prepared. It consists of two halves, the drag (bottom) and the cope (top). The pattern is placed in one half of the mold box.
- Mold Material Preparation: The molding material, typically a mixture of silica sand and a binder, is prepared. The sand is mixed with the binder to provide cohesion and stability during the molding process.
- Mold Packing: The first half of the mold box is filled with the sand mixture and compacted around the pattern. This process, known as ramming, ensures proper mold density and detail reproduction.
- Core Placement: If the component requires internal features or cavities, cores made of sand or other materials are placed in the mold. Cores are designed to create hollow sections or intricate shapes within the final casting.
- Parting Line Creation: The parting line is determined, which is the separation line between the two halves of the mold. It allows for easy removal of the pattern and access to the mold cavity.
- Mold Closure: The second half of the mold box is placed on top of the first half, and the two halves are securely clamped together. The parting line is carefully aligned to ensure proper mold closure.
- Gating and Venting: Channels called gates and vents are created in the mold to allow the molten metal to flow into the mold cavity and gases to escape during pouring.
- Mold Curing: The mold is left undisturbed to allow the binder to set and cure, ensuring the mold’s stability and strength.
- Pattern Removal: Once the mold has cured, the mold box is opened, and the pattern is removed from the sand. This leaves behind a cavity that represents the shape of the final casting.
- Mold Assembly: The mold halves are reassembled, ensuring proper alignment and fit. The gating and venting system is also checked and adjusted if necessary.
- Melting and Pouring: The desired metal alloy is melted in a furnace to its liquid state. Once the metal reaches the proper temperature, it is poured into the mold cavity through the gating system.
- Solidification and Cooling: The molten metal solidifies inside the mold, taking the shape of the cavity. The cooling time varies depending on the size and complexity of the casting. Proper cooling rate control is important to achieve desired casting properties.
- Casting Removal: After the metal has solidified, the mold is opened, and the casting is removed. The casting may still have some attached sand, which is removed through various methods such as shaking, vibrating, or sandblasting.
- Finishing: The casting may undergo additional finishing processes to remove any remaining gating and venting material, clean the surface, and achieve the desired dimensional accuracy and surface finish. Finishing processes can include grinding, machining, polishing, or coating.
- Quality Control: The casting is inspected for any defects, such as porosity, shrinkage, or surface imperfections. Non-destructive testing methods may be employed, including visual inspection, X-ray, or ultrasound, to ensure the integrity of the casting.
The sand casting process offers flexibility, cost-effectiveness, and the ability to produce complex and large-scale components. It is widely used in industries such as automotive, aerospace, machinery, and more. The specific techniques and variations of the process may vary depending on factors such as the complexity of the part, the desired surface finish, and the specific requirements of the casting application.