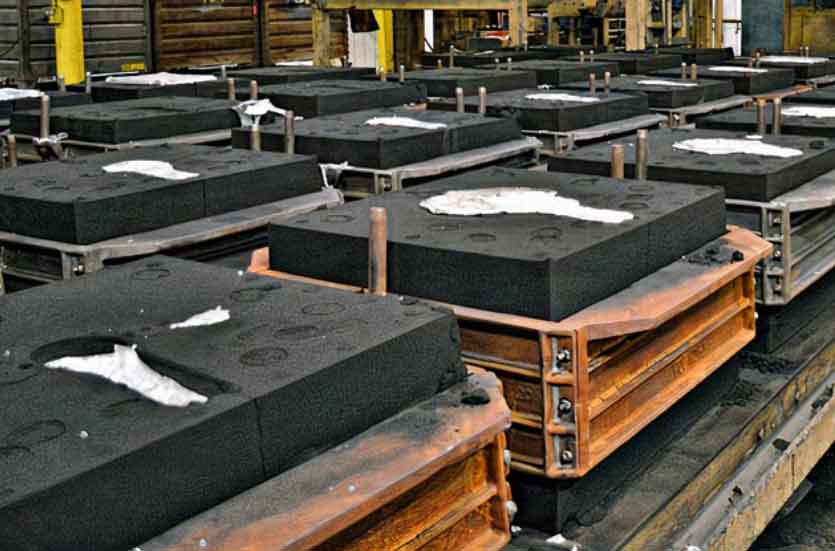
Resin sand casting is a versatile casting process that offers flexibility, precision, and cost-effectiveness in producing metal components. In this comprehensive guide, we will explore the various aspects of resin sand casting, including its process, applications, benefits, and considerations.
What is Resin Sand Casting?
Resin sand casting, also known as self-hardening sand casting or air-set sand casting, is a type of sand casting process where a mixture of sand and resin is used as the mold material. The resin, typically a thermosetting resin, binds the sand particles together to create a solid mold. Resin sand casting is widely used in the production of complex metal components.
The Resin Sand Casting Process:
The resin sand casting process involves several steps:
- Pattern Creation: A pattern is first created, typically made of wood, plastic, or metal, that represents the final shape of the desired component.
- Pattern Assembly: The pattern is then attached to a gating system, which includes channels and gates that allow the molten metal to flow into the mold cavity.
- Mold Preparation: A mixture of sand and resin is prepared. The sand is typically a fine-grain silica sand, and the resin acts as a binder to hold the sand particles together. The sand-resin mixture is then compacted around the pattern and gating system to create the mold.
- Curing: The mold is allowed to cure, or harden, either through natural air drying or by applying heat, depending on the type of resin used. The curing process solidifies the mold and prepares it for metal pouring.
- Metal Pouring: Once the mold is fully cured, it is placed in a flask, and molten metal is poured into the mold cavity through the gating system. The metal fills the cavity, taking the shape of the pattern.
- Solidification and Cooling: The poured metal solidifies within the mold, and the casting is allowed to cool. After cooling, the mold is broken away, revealing the solidified metal component.
- Finishing Operations: The casting may undergo various finishing operations such as trimming, grinding, machining, and surface treatments to achieve the desired final shape, dimensions, and surface finish.
Benefits of Resin Sand Casting:
Resin sand casting offers several advantages, making it a popular choice in various industries:
- Design Flexibility: Resin sand casting allows for the production of complex shapes, intricate details, and thin-walled components that may be challenging to achieve with other casting processes.
- Cost-Effectiveness: Resin sand casting is a cost-effective casting method, especially for small to medium-sized production runs. It does not require expensive tooling or complex equipment, reducing upfront costs.
- Surface Finish: Resin sand casting produces castings with good surface finish and dimensional accuracy, reducing the need for extensive post-casting machining or surface treatments.
- Versatility in Materials: Resin sand casting supports a wide range of metal alloys, including ferrous and non-ferrous metals, providing flexibility in material selection to meet specific application requirements.
- Short Lead Times: The relatively simple and efficient resin sand casting process allows for shorter lead times compared to other casting methods, making it suitable for rapid production cycles.
Considerations and Limitations:
While resin sand casting offers numerous advantages, there are a few considerations and limitations to keep in mind:
- Size and Weight: Resin sand casting is most suitable for small to medium-sized components. Large and heavy parts may pose challenges in mold handling, pouring, and solidification.
- Mold Preparation Time: The preparation and curing time of the mold can be relatively longer compared to other casting processes. Thiscan extend the overall production time, particularly for larger or more intricate molds.
- Mold Fragility: Resin sand molds can be more fragile compared to molds made with other casting processes. Care must be taken during handling and transportation to avoid mold breakage.
- Environmental Considerations: The use of resin in the sand casting process may generate emissions during the curing process. It is important to ensure proper ventilation and implement appropriate measures for resin waste management.
- Pattern Wear and Maintenance: The pattern used in resin sand casting may experience wear and degradation over time due to repeated use. Regular maintenance and pattern repair or replacement may be necessary to maintain casting quality.
Applications of Resin Sand Casting:
Resin sand casting finds application in a wide range of industries, including:
- Automotive: Resin sand casting is used in the production of automotive components such as engine blocks, cylinder heads, transmission cases, and intake manifolds.
- Aerospace: The aerospace industry utilizes resin sand casting for manufacturing aircraft engine components, turbine blades, and structural parts.
- Energy and Power Generation: Resin sand casting is employed to produce components used in power generation equipment, such as turbine parts, heat exchangers, and pump housings.
- Industrial Machinery: Resin sand casting is utilized in the production of various industrial machinery components, including gears, valves, pump bodies, and machine tool parts.
- Pumps and Valves: Resin sand casting is commonly used to manufacture pump and valve components for applications in industries like oil and gas, water treatment, and chemical processing.
- Art and Sculpture: The versatility of resin sand casting allows for the creation of intricate art pieces, sculptures, and decorative components.
Resin sand casting offers a balance of cost-effectiveness, design flexibility, and high-quality castings, making it a versatile casting method for a wide range of applications. With ongoing advancements in materials, equipment, and process control, resin sand casting continues to evolve and find new applications in modern manufacturing industries.