Quality control is a critical aspect of the sand casting process to ensure precision, reliability, and consistency in the produced castings. Here are key steps and practices involved in quality control for sand casting:
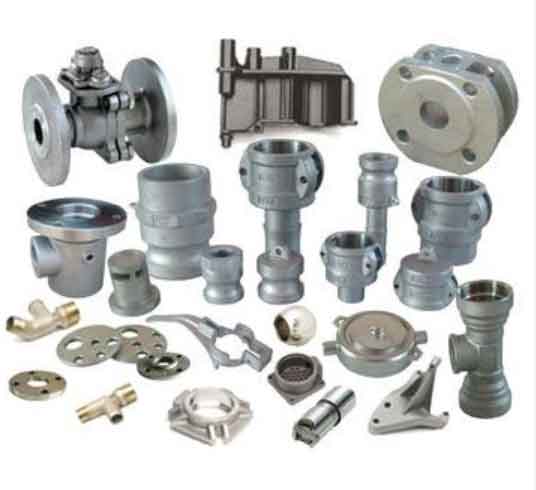
- Incoming Material Inspection: Raw materials, such as sand, additives, binders, and alloys, should undergo thorough inspection to ensure they meet the required specifications and quality standards. This includes checking the physical properties, chemical composition, and any certifications or test reports.
- Pattern and Mold Inspection: Patterns and molds should be inspected for dimensional accuracy, proper gating and riser design, and any defects or damage. This ensures that the molds will produce accurate and defect-free castings.
- Mold and Core Quality Control: Prior to casting, the molds and cores should be inspected for proper assembly, surface defects, core alignment, and dimensional accuracy. This helps to avoid issues such as misruns, cold shuts, or dimensional variations.
- Melting and Pouring Control: During the melting and pouring process, strict control measures should be implemented to maintain the correct temperature, ensure proper alloy composition, and minimize impurities. Regular metal samples should be taken and analyzed to verify compliance with the required specifications.
- Solidification and Cooling Monitoring: The solidification and cooling process of the castings should be closely monitored to prevent defects such as shrinkage, porosity, or warpage. Temperature monitoring, time-lapse recordings, and thermal analysis can be employed to ensure proper solidification and cooling rates.
- Visual Inspection: Visual inspection is performed on the finished castings to detect any visible defects such as surface irregularities, cracks, or incomplete filling. Skilled inspectors examine the castings using various techniques, including visual examination, magnification, or dye penetrant testing.
- Non-Destructive Testing (NDT): Non-destructive testing methods, such as X-ray, ultrasound, magnetic particle testing, or liquid penetrant testing, can be employed to detect internal defects such as porosity, inclusions, or cracks without damaging the castings. NDT techniques help ensure the integrity and quality of the castings.
- Dimensional Inspection: Dimensional inspection is carried out to verify the accuracy and conformity of the castings to the required specifications. This involves using precision measuring tools and techniques such as coordinate measuring machines (CMM), gauges, or optical measurement systems.
- Documentation and Traceability: Proper documentation of quality control processes, inspection results, and traceability of materials and production parameters is essential. This ensures that the castings can be traced back to their specific production details and provides a reference for future quality analysis and improvement.
- Process Audits and Continuous Improvement: Regular process audits and quality reviews help identify areas for improvement and ensure adherence to quality standards. By analyzing quality data, identifying root causes of defects, and implementing corrective actions, the sand casting process can be continuously improved.
By implementing robust quality control measures, manufacturers can ensure that the sand casting process consistently produces castings with the required precision, reliability, and quality. This helps to minimize scrap, rework, and customer dissatisfaction while improving overall productivity and customer satisfaction.