Sand casting is a casting method in which the metal liquid fills the mold cavity under the action of gravity. Steel and many alloy materials in our life can be produced by sand casting. Sand casting has many advantages:
(1) It can produce various large and complex blank parts such as box, frame and bed;
(2) It can cast several grams of objects or hundreds of tons of objects;
(3) The source of materials used is wide and the cost is low;
(4) High casting precision can reduce the allowance of finishing.
Therefore, sand casting has been widely used in the foundry industry. At present, the sand casting process is also constantly improving and improving. For example, the mold filling process of sand casting is simulated by casting simulation software. The casting model of machine tool bed is established. Combining with the process characteristics and theory, the gating system and casting process are designed. The process of casting filling is simulated. The process parameters of simulation curve are obtained. The parameters are optimized, which can be used to predict the surface defects of castings and improve the casting efficiency. In reference [6,7], the casting process of machine bed is optimized by simulation software. According to the calculation results of the software, the influence of process parameters on the casting deformation is obtained. The simulation results show that the best filling temperature, filling speed and thickness of the casting are obtained. After optimization, shrinkage cavity can be avoided, which meets the needs of practical casting. However, in the past few people used to study the sand casting control method of machine tool bed. If the filling speed of liquid metal is not properly controlled, it will lead to uneven distribution of thermal stress in the process of filling, and finally affect the surface quality of castings. In this paper, the sand casting process flow of machine tool bed is studied, the sand casting process flow chart is given, the calculation model of sand casting filling speed is constructed, PLC is used to control the filling speed of sand casting, and the error simulation of filling speed is carried out through MAT-LAB software. At the same time, compared with the simulation results of traditional PI control filling speed error, it provides a reference for the control of filling speed in sand casting of machine tool bed.
The machine bed is usually made by sand casting, and its technological process mainly includes the following steps:
(1) Drawing, drawing casting drawing of machine tool bed on computer;
(2) Making core, putting resin sand into the mold, thus forming the internal cavity of the casting;
(3) Forming, pouring molten metal liquid in the mold;
(4) Open the sand box, remove the molding sand and clean the casting;
(5) Inspect whether the casting is qualified.
The design basis of sand casting gating system is based on the principle of fluid mechanics. When the liquid metal is used to fill the cavity below the inner sprue, the pressure head acting on the fluid will not change. When the liquid metal is used to fill the cavity above the inner sprue, the pressure head acting on the fluid will change. It is assumed that one end of the metal liquid is the metal level of the sprue cup, and the other end is the outlet of the metal liquid
Where: H is the height of the sprue; V is the velocity of the outflow of the metal liquid internal sprue; G is the acceleration of gravity; Δ h is the height of the loss of the head of the metal liquid.
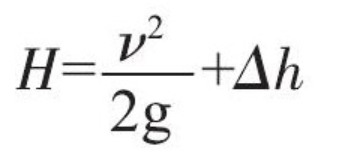
Δ h is expressed as:
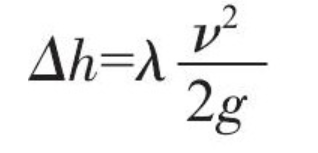
Where λ is the local damping coefficient of the gating system.
Substituting formula (2) into formula (1) can obtain:
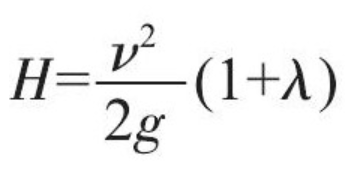
The velocity equation of the sprue outlet is as follows:
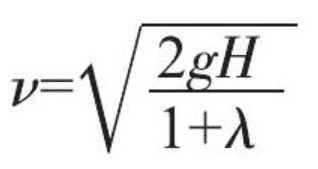
When the metal liquid is used to fill the following cavities of the internal sprue, the weight calculation equation of the metal liquid through the internal sprue is as follows:
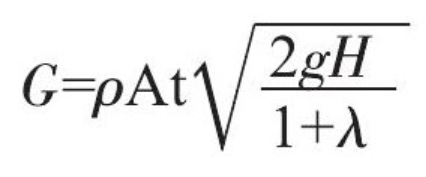
Where: G is the weight of the metal liquid flowing in the cavity below the sprue; ρ is the density of the metal liquid; a is the sectional area of the sprue pipe; t is the time to fill the cavity below the sprue.