1. Introduction
In the field of coal mining machinery, hydraulic supports play a crucial role in ensuring the safety and efficiency of underground operations. The column socket, as a key component of the hydraulic support, is subjected to significant forces and stresses during the mining process. Therefore, the quality and performance of the column socket are of utmost importance.
1.1 Background
The ZY10000/17/35D hydraulic support is widely used in modern coal mines. The column socket of this hydraulic support is typically made of ZG28NiCrMo, a material known for its excellent mechanical properties. The chemical composition and mechanical properties of ZG28NiCrMo are presented in Tables 1 and 2, respectively. These properties ensure that the column socket can withstand the harsh operating conditions in the mine.
1.2 Importance of Column Socket Quality
The hydraulic support is constantly exposed to various forces, including vertical pressure, overturning moments, and horizontal forces. The majority of these forces are transmitted to the column socket through the columns. Any casting defects in the column socket can lead to cracks or fractures during long-term use underground, which not only affects the support strength of the hydraulic support but also poses a serious threat to the safety and efficiency of coal mining operations.
1.3 Role of Numerical Simulation
Numerical simulation has emerged as a powerful tool in the field of casting. By using software like ProCAST, engineers can predict potential casting defects before the actual production process. This allows for timely adjustments and optimizations, ultimately improving the quality and reliability of the castings.
2. Hydraulic Support Column Socket Materials and Casting Process
2.1 Material Properties
As mentioned earlier, the column socket is made of ZG28NiCrMo. This alloy steel offers a combination of high tensile strength, good yield strength, and sufficient elongation and impact absorption capabilities. The specific values of these properties are shown in Table 2. These characteristics make ZG28NiCrMo suitable for withstanding the complex loading conditions experienced by the column socket.
2.2 Casting Process Flow
The casting process of the column socket involves several sequential steps:
2.2.1 Production Process Preparation
This stage includes the preparation of production process plans, process documents, and casting process drawings. These documents serve as the guiding principles for the entire casting process, ensuring that all operations are carried out in a systematic and controlled manner.
2.2.2 Production Preparation
The necessary materials for melting, such as core boxes and sandboxes, are assembled. The quality and proper functioning of these equipment have a direct impact on the final quality of the casting.
2.2.3 Molding and Core Making
During molding, special attention is paid to achieving the appropriate compactness of the sand mold. After the mold is formed, nitrogen is uniformly injected into all parts of the mold. A vertical runner nest is left at the bottom of the vertical runner, and after the mold is assembled, loose sand in the cavity is removed using a hose.
2.2.4 Melting and Pouring
This is a critical step where the molten metal is prepared and poured into the mold. The temperature and flow rate of the molten metal need to be carefully controlled to ensure proper filling of the mold cavity.
2.2.5 Sand Removal, Cleaning, and Casting Inspection
Once the casting has solidified, the sand is removed, and the casting undergoes a series of cleaning processes to remove any surface defects or impurities. Finally, a comprehensive inspection is carried out to ensure that the casting meets the required quality standards.
3. Finite Element Simulation
3.1 Optimization Before Simulation
3.1.1 Model Building
The Pro/E software is used to create a three-dimensional solid model of the column socket. The dimensions of the column socket are 550 mm in length and 440 mm in width. The material is set as ZG28NiCrMo, with a heat treatment of quenching and tempering to achieve a hardness of 240 – 280 HB. The mass of the column socket is 182.09 kg. The model is then imported into the ProCAST software for further analysis.
3.1.2 Meshing
A mesh with 248,226 elements and 50,926 nodes is generated for the model. The average wall thickness of the sand mold is 30 mm, and a shrinkage rate of 5.5% is considered. This detailed meshing allows for accurate simulation of the casting process.
3.1.3 Pouring System Design
The pouring system is designed based on the principles of casting steel parts. The dimensions of the various components are as follows: the diameter of the sprue is φ55 mm, with a height of 360 mm and a sprue well of 40 mm; the length of the runner is 385 mm, with a trapezoidal cross-section having a bottom width of 40 mm, a top width of 30 mm, and a height of 40 mm; the length of the ingate is 140 mm, with a trapezoidal cross-section having a bottom width of 40 mm, a top width of 36 mm, and a height of 20 mm.
3.1.4 Simulation Parameter Settings
The casting method is set as conventional gravity casting. The pouring temperature is 1580 °C, and the initial environmental temperature is 25 °C. Appropriate heat transfer coefficients are selected for different interfaces: metal – metal (1100 – 5100 W/(m²·K)), metal – sand (300 – 1000 W/(m²·K)), sand – sand (210 – 310 W/(m²·K)), solid – air (4 – 9 W/(m²·K)), and solid – cold air (150 – 1100 W/(m²·K)). Velocity and temperature boundary conditions are applied to the corresponding nodes in the model.
3.1.5 Simulation Results Analysis
The simulation results provide valuable insights into the casting process:
3.1.5.1 Filling Time
The filling time of the column socket casting is shown in Figure 2. It can be observed that due to the location of the ingate at the top of the model, a part of the front area of the column socket is filled later. This uneven filling may lead to potential defects such as air entrapment or incomplete filling in certain areas.
3.1.5.2 Solidification Time
Figure 3 illustrates the solidification time of the casting. The bottom of the column socket, the cross ribs, and the riser are the last to solidify. This sequence of solidification is important as it affects the feeding behavior and the potential for shrinkage defects.
3.1.5.3 Shrinkage Hole Location
As shown in Figure 4, shrinkage holes are found at the bottom of the cross ribs and at the gate and riser. The presence of a large shrinkage hole at the middle cross rib of the column socket bottom is a significant defect that can compromise the structural integrity of the casting.
3.2 Casting Process Optimization and Simulation
3.2.1 Problem Analysis
The analysis of the traditional casting process reveals that the main cause of casting defects in the column socket is the difference in shrinkage rates between the liquid and solid states, combined with a wide crystallization temperature range, which leads to a volumetric solidification mode. This results in insufficient feeding from the riser.
3.2.2 Optimization Measures
To address these issues, the following optimization measures are implemented:
3.2.2.1 Insulation Riser
A 20-mm-thick insulation sleeve is added to the riser. This insulation sleeve reduces the heat transfer rate from the riser, thereby increasing its solidification time and improving its feeding efficiency.
3.2.2.2 Riser Size Increase
The size of the riser is increased to 290 mm in length, 130 mm in width, and 300 mm in height. This larger riser provides a greater volume of molten metal for feeding, reducing the likelihood of shrinkage defects.
3.2.3 Simulation Results After Optimization
After implementing the optimization measures, the simulation is repeated to evaluate the effectiveness of the changes:
3.2.3.1 Shrinkage Hole Location
As shown in Figure 5, the optimized process significantly improves the location and likelihood of shrinkage holes. The shrinkage holes are now mainly concentrated at the riser, and the large shrinkage hole at the middle cross rib of the column socket bottom has been eliminated.
3.2.3.2 Filling Time
Figure 6 indicates that the filling time remains relatively unchanged after optimization. This means that the production efficiency is not significantly affected by the process changes.
3.2.3.3 Solidification Time
The solidification time, as shown in Figure 7, is noticeably extended, and the last unfrozen point is raised. This extended solidification time provides more time for the riser to feed the casting, thereby improving the overall quality of the casting.
4. Conclusion
4.1 Summary of Findings
Through numerical simulation and production verification, the following conclusions can be drawn:
4.1.1 Riser Optimization
Increasing the size and adding insulation to the riser effectively reduces heat transfer, resulting in a more uniform temperature distribution within the casting. This helps to minimize thermal stresses and reduces the occurrence of defects.
4.1.2 Process Performance
The filling time remains relatively stable, while the solidification time is extended by 410 s. This extended solidification time significantly enhances the feeding effect of the riser, ensuring better quality of the casting.
4.1.3 Defect Reduction
The volume of shrinkage holes is noticeably reduced, and they are mainly located at the riser. This effectively reduces the occurrence of shrinkage holes, cracks, and other casting defects within the casting, improving the overall quality and reliability of the column socket.
4.2 Significance of the Study
This research demonstrates the importance and effectiveness of using numerical simulation in optimizing the casting process of hydraulic support column sockets. By identifying and addressing potential casting defects in the design stage, the production of high-quality column sockets can be achieved, thereby enhancing the performance and safety of hydraulic supports in coal mining operations.
4.3 Future Research Directions
Future research can focus on further optimizing the casting process by exploring different materials, insulation materials, and process parameters. Additionally, the integration of simulation and real-time monitoring technologies during the casting process can provide more accurate control and improve the quality of castings.
4.4 Industrial Application and Impact
The findings of this study have significant implications for the industrial production of hydraulic support column sockets. By implementing the optimized casting process, manufacturers can expect to improve the quality and reliability of their products, leading to enhanced performance and safety in coal mining operations. The reduced occurrence of casting defects, such as shrinkage holes and cracks, translates into longer service life and lower maintenance costs for the hydraulic supports.
In the manufacturing environment, the optimized process can also result in increased production efficiency. The relatively unchanged filling time, combined with the improved quality, allows for a more streamlined production line with fewer rejects and rework. This not only saves time and resources but also enables manufacturers to meet the growing demand for high-quality hydraulic support components in a timely manner.
Moreover, the use of numerical simulation as a design and optimization tool can significantly reduce the need for trial-and-error in the casting process. This leads to shorter product development cycles and lower costs associated with prototyping and experimentation. Manufacturers can now make more informed decisions about the casting process parameters and design modifications, based on the insights gained from the simulation results.
4.5 Comparison with Other Casting Technologies
While the focus of this study has been on the optimization of the traditional sand casting process for hydraulic support column sockets, it is worth comparing this approach with other casting technologies. For example, investment casting offers the potential for producing complex geometries with high dimensional accuracy and excellent surface finish. However, investment casting is generally more expensive and time-consuming compared to sand casting, due to the need for intricate wax patterns and multiple processing steps.
Another alternative is die casting, which is known for its high production rates and ability to produce parts with thin walls and tight tolerances. However, die casting is typically limited to non-ferrous metals and alloys, and the initial tooling costs can be prohibitive for small to medium production runs. In contrast, sand casting is a versatile and cost-effective method that can handle a wide range of materials and part sizes, making it a popular choice for the production of large and heavy-duty components like hydraulic support column sockets.
4.6 Environmental Considerations
In addition to the technical and economic aspects, environmental considerations are becoming increasingly important in the manufacturing industry. The casting process can have a significant environmental impact, mainly due to the consumption of energy and the generation of waste materials. Therefore, future research and process optimization should also take into account the environmental footprint of the casting process.
One possible approach is to explore the use of recycled materials in the casting process. By incorporating recycled metal scrap into the melt, the consumption of virgin raw materials can be reduced, along with the associated energy and environmental costs. Additionally, the development of more energy-efficient melting and casting techniques, such as induction melting and vacuum casting, could help to lower the overall energy consumption of the process.
The proper management and disposal of waste materials, such as used sand and slag, is also crucial. Recycling and reusing these waste materials can not only reduce the amount of waste sent to landfills but also contribute to the conservation of natural resources. For example, the spent sand from the casting process can be regenerated and reused in subsequent casting operations, after appropriate treatment to remove any contaminants.
4.7 Quality Control and Inspection
To ensure the consistent quality of the cast hydraulic support column sockets, a comprehensive quality control and inspection system is essential. In addition to the numerical simulation and process optimization, non-destructive testing methods can be employed to detect any internal and surface defects in the castings.
Ultrasonic testing is a commonly used non-destructive testing technique that can detect internal flaws, such as cracks and porosity, by sending high-frequency sound waves through the casting. X-ray inspection is another powerful tool that can provide detailed images of the internal structure of the casting, allowing for the detection of even small defects. Visual inspection and dimensional measurement are also important steps in the quality control process, to ensure that the castings meet the required geometric tolerances and surface finish standards.
By implementing a robust quality control and inspection system, manufacturers can identify and address any quality issues at an early stage, preventing defective products from reaching the market. This not only protects the reputation of the manufacturer but also ensures the safety and reliability of the hydraulic support systems in which the column sockets are used.
4.8 Training and Education
The successful implementation of the optimized casting process and the use of advanced technologies, such as numerical simulation and non-destructive testing, require a skilled and knowledgeable workforce. Therefore, training and education programs should be developed to enhance the capabilities of the employees involved in the casting process.
These programs could include theoretical and practical training on casting principles, process optimization, simulation software usage, and quality control techniques. Hands-on experience with the latest equipment and technologies can help employees to better understand and apply the concepts learned in the classroom. Additionally, continuous education and professional development opportunities should be provided to keep employees updated with the latest advancements in the field of casting technology.
By investing in the training and education of their employees, manufacturers can build a competent and innovative workforce that is capable of driving continuous improvement in the casting process and ensuring the long-term success of the company.
4.9 Global Trends and Market Outlook
The global demand for coal and other minerals continues to drive the growth of the mining industry, which in turn fuels the demand for hydraulic support systems and their components, including column sockets. As mining operations become more mechanized and automated, the requirements for high-quality and reliable hydraulic support equipment are expected to increase.
In response to these market trends, manufacturers are constantly striving to improve the performance and efficiency of their products. The use of advanced materials, manufacturing processes, and quality control techniques will be key to meeting the evolving needs of the industry. Additionally, the globalization of the manufacturing industry has led to increased competition, forcing companies to seek cost-effective solutions without compromising on quality.
The future of the hydraulic support column socket casting industry will also be influenced by technological advancements in other related fields, such as materials science, robotics, and artificial intelligence. For example, the development of new materials with enhanced properties could enable the production of lighter and stronger column sockets, while the integration of robotics and automation in the casting process could improve productivity and quality consistency.
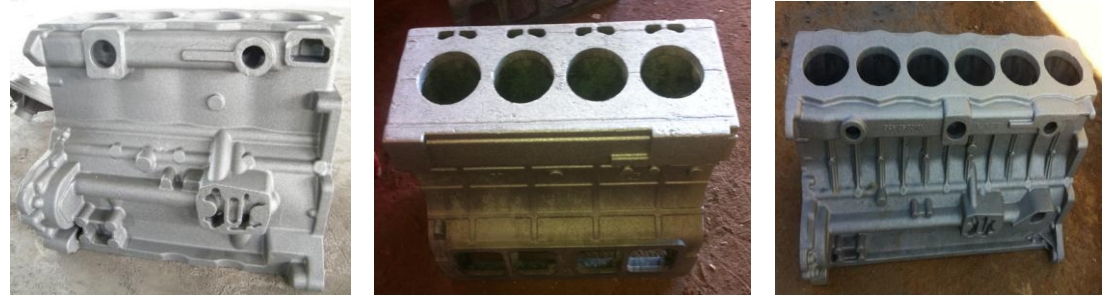