Introduction
Impact Crushers are widely used in various industries for crushing materials such as minerals, aggregates, and recycling materials. A critical component in these crushers is the blow bar, which plays a significant role in the crushing process. Proper management and selection of blow bar can greatly influence the overall efficiency of an Impact Crusher, particularly in terms of reducing downtime. This article explores the importance of blow bar in minimizing downtime in Impact Crusher operations, discussing materials, design considerations, maintenance practices, and their impact on operational efficiency.
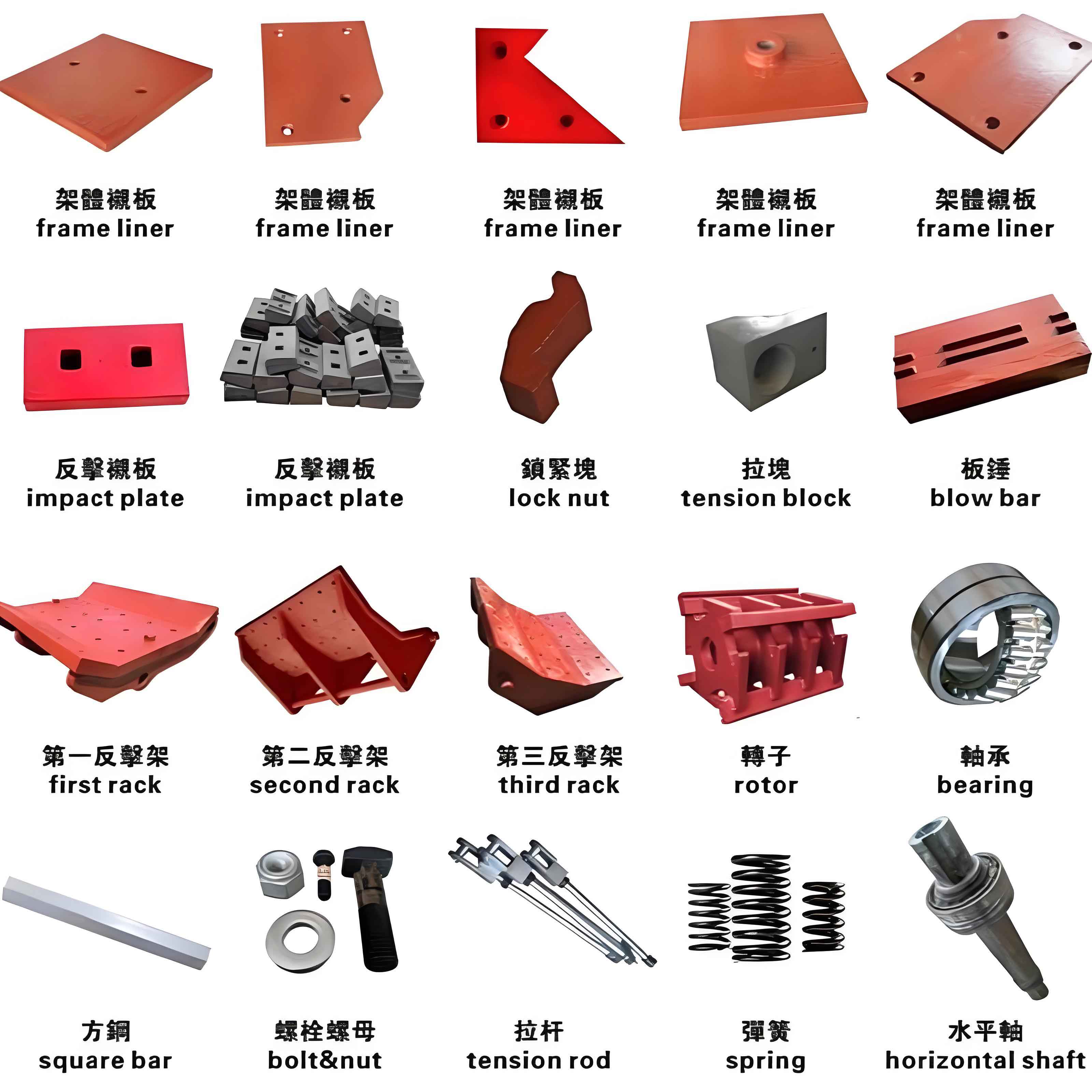
Importance of Blow Bar in Impact Crushers
Blow bar is mounted on the rotor of an Impact Crusher and are responsible for striking and crushing the material fed into the crusher. The performance, durability, and wear resistance of blow bar directly affect the efficiency and reliability of the crusher.
Key Functions of Blow Bar:
- Crushing Efficiency:
- Blow bar generate the impact force needed to break down materials, determining the crushing efficiency of the Impact Crusher.
- Material Fragmentation:
- The repeated strikes by blow bar help fragment the material into smaller sizes, facilitating further processing or use.
- Wear Resistance:
- High-quality blow bar resist wear and tear, extending their lifespan and maintaining consistent crusher performance.
Materials Used in Blow Bar
Choosing the right material for blow bar is crucial for reducing downtime and ensuring the longevity of an Impact Crusher. Different materials offer varying degrees of wear resistance, impact strength, and suitability for different crushing applications.
Common Materials for Blow Bar:
- High Manganese Steel:
- Characteristics: High toughness and work-hardening properties, ideal for high-impact conditions.
- Applications: Suitable for crushing abrasive materials like granite and basalt.
- Advantages: Excellent impact resistance and durability.
- Disadvantages: Rapid wear when used with less abrasive materials.
- Martensitic Steel:
- Characteristics: Good wear resistance combined with moderate impact strength.
- Applications: Suitable for medium-hard materials such as limestone.
- Advantages: Balanced wear resistance and toughness.
- Disadvantages: Not suitable for highly abrasive materials.
- Chrome Steel:
- Characteristics: High hardness and superior wear resistance due to chromium content.
- Applications: Ideal for highly abrasive materials.
- Advantages: Long lifespan in abrasive conditions.
- Disadvantages: Brittle and prone to breakage under high-impact stress.
- Ceramic Inserts:
- Characteristics: Embedded ceramic inserts within a steel matrix to enhance wear resistance.
- Applications: Suitable for extremely abrasive materials like asphalt, concrete, and demolition debris.
- Advantages: Superior wear resistance and extended lifespan.
- Disadvantages: Higher cost and potential for breakage if not properly manufactured.
Material | Characteristics | Applications | Advantages | Disadvantages |
---|---|---|---|---|
High Manganese Steel | High toughness, work-hardening | Abrasive materials (granite, basalt) | Excellent impact resistance | Rapid wear with less abrasive materials |
Martensitic Steel | Wear resistance, impact strength | Medium-hard materials (limestone) | Balanced wear resistance, toughness | Not ideal for extremely abrasive materials |
Chrome Steel | High hardness, wear resistance | Highly abrasive materials | Long lifespan in abrasive conditions | Brittle, can break under high impact |
Ceramic Inserts | Enhanced wear resistance | Extremely abrasive materials (asphalt) | Superior wear resistance, extended lifespan | Higher cost, potential for breakage |
Design Considerations for Blow Bar
The design of blow bar can significantly influence their efficiency, wear resistance, and impact on reducing downtime. Important design aspects include shape, profile, and reinforcement.
Shape and Profile:
- Straight Blow Bar:
- Description: Flat and straight design.
- Advantages: Easy to manufacture and replace.
- Disadvantages: Less effective in distributing impact forces, leading to uneven wear.
- Curved Blow Bar:
- Description: Curved profile to improve impact distribution.
- Advantages: Better distribution of impact forces, reducing uneven wear.
- Disadvantages: More complex to manufacture and replace.
- Wing-Tip Blow Bar:
- Description: Extended tips to enhance material penetration.
- Advantages: Improved material penetration and crushing efficiency.
- Disadvantages: Higher wear at the tips, requiring more frequent replacement.
Reinforcement:
- Solid Blow Bar:
- Description: Solid construction for maximum strength.
- Advantages: High durability and resistance to breakage.
- Disadvantages: Heavier, causing increased stress on the Impact Crusher.
- Composite Blow Bar:
- Description: Combination of materials for enhanced performance.
- Advantages: Optimized wear resistance and impact strength.
- Disadvantages: Higher manufacturing cost and complexity.
Design Aspect | Description | Advantages | Disadvantages |
---|---|---|---|
Straight Blow Bar | Flat and straight design | Easy to manufacture, replace | Less effective in impact distribution, uneven wear |
Curved Blow Bar | Curved profile | Better impact distribution, reduced wear | Complex to manufacture, replace |
Wing-Tip Blow Bar | Extended tips | Improved penetration, efficiency | Higher wear at tips, frequent replacement |
Solid Blow Bar | Solid construction | High durability, breakage resistance | Heavier, increased stress on crusher |
Composite Blow Bar | Combination of materials | Optimized wear resistance, strength | Higher cost, manufacturing complexity |
Maintenance Practices for Blow Bar
Proper maintenance of blow bar is essential to minimize downtime and ensure the efficient operation of an Impact Crusher. Regular inspections, timely replacements, and using appropriate materials are key practices to enhance blow bar longevity and performance.
Maintenance Tips:
- Regular Inspections:
- Conduct routine inspections to check for signs of wear, cracks, or damage.
- Replace blow bar when wear reaches critical levels to prevent damage to the Impact Crusher.
- Proper Installation:
- Ensure blow bar is correctly installed and secured to avoid movement during operation.
- Follow manufacturer guidelines for installation and torque specifications.
- Material Selection:
- Select the appropriate material for blow bar based on the type of material being crushed and the specific crusher application.
- Use high-quality blow bar to ensure durability and performance.
- Balancing:
- Regularly balance the rotor to minimize vibration and uneven wear on blow bar.
- Ensure that all blow bar is of the same weight and dimensions to maintain balance.
Maintenance Practice | Description |
---|---|
Regular Inspections | Routine checks for wear, cracks, or damage |
Proper Installation | Ensure correct installation and securing |
Material Selection | Choose appropriate material for application |
Balancing | Balance rotor to minimize vibration |
Impact of Blow Bar on Reducing Downtime
Effective management and selection of blow bar can significantly reduce downtime in Impact Crusher operations, leading to increased productivity and lower operational costs. Key factors include:
- Enhanced Durability:
- Using high-quality materials and designs that resist wear and breakage prolongs the lifespan of blow bar, reducing the frequency of replacements.
- Improved Efficiency:
- Optimally designed blow bar enhance crushing efficiency, reducing the time required to process materials and increasing overall throughput.
- Reduced Maintenance Intervals:
- Regular maintenance and timely replacements prevent unexpected breakdowns, ensuring continuous operation of the Impact Crusher.
- Cost Savings:
- Minimizing downtime through effective blow bar management reduces maintenance costs and increases the return on investment for crushing operations.
Benefit | Description |
---|---|
Enhanced Durability | Longer lifespan, less frequent replacements |
Improved Efficiency | Faster processing, increased throughput |
Reduced Maintenance Intervals | Prevents unexpected breakdowns, ensures continuous operation |
Cost Savings | Lower maintenance costs, higher return on investment |
Conclusion
Blow bar is integral to the efficient operation of Impact Crushers, directly influencing the crushing process and overall productivity. By selecting the right materials, considering design aspects, and implementing regular maintenance practices, operators can significantly reduce downtime and enhance the performance of their Impact Crushers. Understanding the role of blow bar in generating impact forces, fragmenting materials, and resisting wear is crucial for optimizing crusher operations and achieving long-term reliability and cost-effectiveness.
4o