18PA6B sand mold casting crankcase is made of nodular cast iron, with a gross weight of about 13T. Resin sand casting forming process is adopted. The process flow mainly includes six parts: molding, core making, box matching, pouring, cleaning and heat treatment. Specifically, the resin sand is first transported to the sand mixer for sand mixing, and the curing agent is added in the process. After uniform mixing, the mixture is poured into the mold for molding, and the upper mold and the lower mold are manufactured. The cement core is made by hand and core shooting machine. After that, put the finished cement core into the lower mold and sand box for box distribution, and then dry the whole after completion. Then, the melting and pouring are carried out, and the raw materials are melted and the composition is adjusted. After the composition is qualified, the molten iron is injected into the mold cavity according to the process requirements. Conduct solidification, heat preservation and cooling in the mold, and clean the box after about 7 days. After rough cleaning, heat treatment shall be carried out on the sand casting crankcase, and shot peening and fine cleaning shall be carried out again.
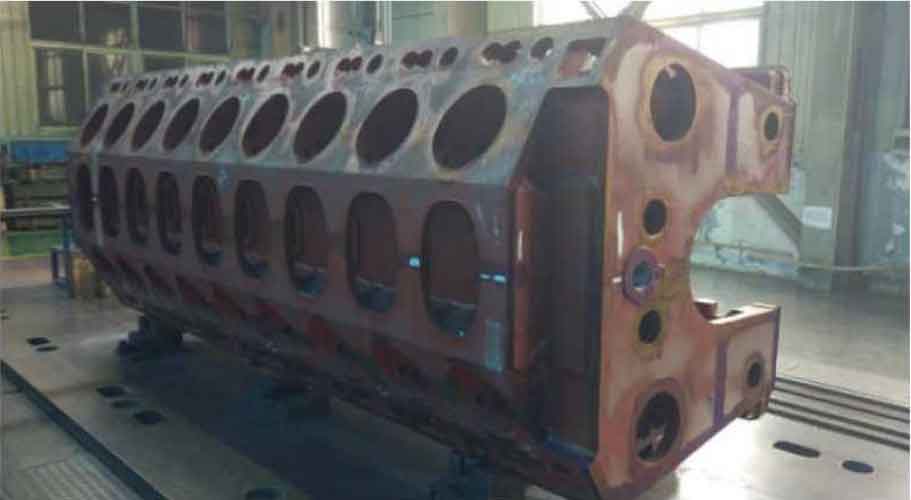
Six sets of 18PA6B sand mold casting crankcases of a project adopt this targeted manufacturing supervision method, and the first pass rate of the products is 100%. There was no scrapping of sand casting crankcase due to defects in key parts, which ensured product quality and promoted project implementation.
Due to the large tonnage and long casting cycle of sand casting crankcase, if the manufacturing process is not well controlled, defects are likely to occur, and the products will be scrapped in serious cases, which will cause a great waste of manpower and material resources to the manufacturer, and also have a great impact on the delivery of diesel engine equipment and project implementation. In addition to the characteristics of sand casting process itself, it is not easy to analyze the causes after problems occur, and it is difficult and costly to verify the causes. Therefore, sufficient preparation shall be made for the supervision of large sand casting parts. Pay attention to collecting all kinds of information, adopt risk thinking and strengthen process control in combination with previous project experience. To ensure the final qualification of products by process qualification, so as to improve product quality and ensure the effect of manufacturing supervision.