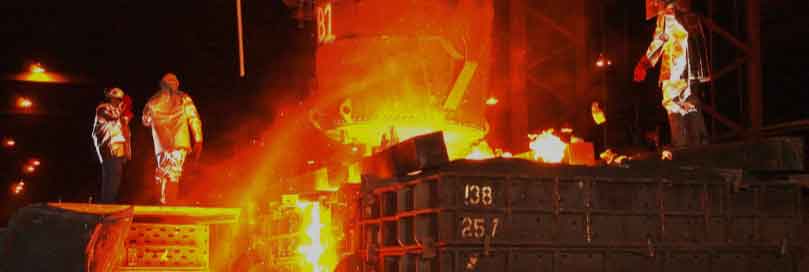
Foundry technology plays a crucial role in the manufacturing industry, particularly in metal casting processes. It involves the creation of complex metal components by pouring molten metal into molds and allowing it to solidify. Over the years, advancements in foundry technology have pushed the boundaries of metal casting, enabling the production of intricate and high-quality castings for various industries. Here are some key areas where foundry technology has made significant progress:
Advanced Mold Materials:
Traditional foundry molds were primarily made of sand or clay, which limited the complexity and precision of castings. However, the development of advanced mold materials, such as ceramic, silica, and investment casting molds, has revolutionized the industry. These materials offer better dimensional accuracy, surface finish, and heat resistance, allowing the creation of intricate castings with fine details.
Computer-Aided Design and Simulation:
The integration of computer-aided design (CAD) and simulation software has transformed the way castings are designed and produced. Engineers can now create virtual models of the desired casting and simulate the entire manufacturing process, including mold filling, solidification, and cooling. This enables the identification and mitigation of potential defects and optimization of the casting process before any physical molds are created.
Additive Manufacturing (3D Printing):
Additive manufacturing, commonly known as 3D printing, has emerged as a game-changer in the foundry industry. It allows the production of complex geometries that were previously impossible to achieve using traditional casting methods. 3D printing of molds and patterns reduces the time and cost associated with tooling, enables rapid prototyping, and offers design freedom for intricate shapes and internal structures.
Improved Casting Alloys:
The development of new and improved casting alloys has expanded the range of applications for metal castings. These alloys offer enhanced mechanical properties, improved corrosion resistance, and high-temperature stability, making them suitable for critical components in industries such as aerospace, automotive, and energy.
Process Automation and Robotics:
Automation and robotics have significantly improved the efficiency and consistency of metal casting processes. Robotic systems can handle tasks such as mold handling, pouring molten metal, and post-casting operations with precision and speed. Automated systems not only increase productivity but also ensure better process control and quality.
Environmental Considerations:
Foundry technology has also made progress in addressing environmental concerns. Efforts have been made to reduce energy consumption, minimize waste generation, and control emissions in metal casting processes. Technologies like electric induction melting furnaces, improved refractory materials, and optimized process parameters contribute to greener and more sustainable foundry operations.
The continuous advancements in foundry technology have pushed the boundaries of what is possible in metal casting. With improved materials, advanced design tools, additive manufacturing, automation, and environmental considerations, the industry can create complex, high-quality castings that meet the demands of modern applications across various sectors.