The friction and wear tests of nitrocarburizing samples were carried out on a friction and wear testing machine. The friction pairs were made of 45 ᦇ quenched steel with a diameter of 50 × 5 mm and a hardness of 60 HRC. The sample size was made into a 4 mm × 4 mm × 10 mm pin sample cuboid. The experimental parameters are load of 20 N, friction radius of 15 mm, friction time of 110 min and rotation speed of 397 R / min, respectively. The stroke can be calculated as 4.11 km. The friction coefficient was recorded automatically by the wear tester.
After cleaning and ultrasonic drying of the samples before and after abrasion, the mass of the samples before and after abrasion is weighed with an electronic balance (accuracy of 0.0001 g), which are recorded as M1 and M2 respectively. The mass difference (m1-m2) before and after wear is recorded as △ m and the volume wear rate of the material can also be obtained from the mass difference, as shown in the formula
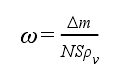
Where:
ω – Volume wear rate (mm3 / N ⋅ m);
△ m — the mass difference of the sample before and after wear (g);
N — experimental load (n);
S — experimental sliding distance, i.e. stroke (m);
ρ V — bulk density of sample (g / cm3).
The Archimedes drainage method is used to test the bulk density of the sample, and the calculation formula of the bulk density ρ V is as follows:
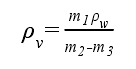
Where:
M1 — dry weight of sample (g);
M2 — mass in air of sample after saturated water absorption (g);
M3 — mass of water after saturated water absorption (g);
ρ w — density of water (1.0 g / cm3).