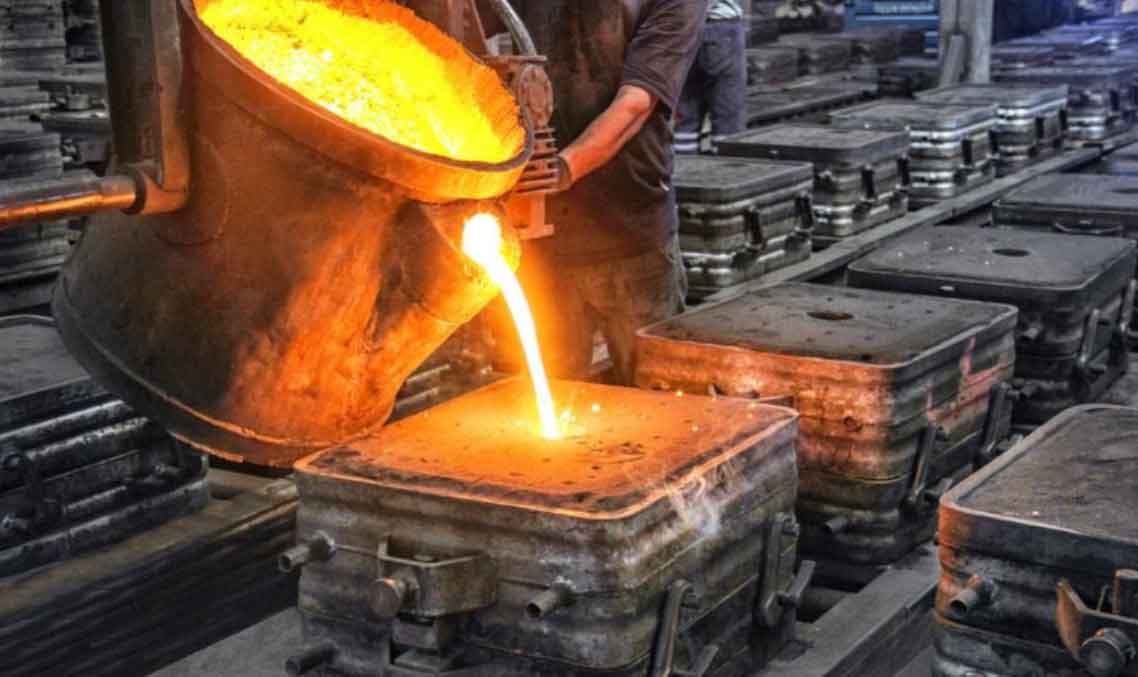
The collaborative process with sand casting manufacturers typically involves a series of steps from the initial design phase to the final delivery of the cast components. This process aims to ensure seamless communication, efficient production, and the successful realization of the customer’s casting requirements. Here’s a general overview of the collaborative process with sand casting manufacturers:
1. Design and Engineering Phase:
- Design Consultation: The collaboration begins with discussions between the customer and the sand casting manufacturer to understand the casting requirements, component specifications, and any specific design considerations.
- Pattern Design and Development: If the customer does not already have a pattern or CAD model, the sand casting manufacturer can provide pattern design services or assist in creating 3D CAD models of the component.
- Design for Manufacturability: The manufacturer reviews the design to identify any potential issues that might affect casting quality or production efficiency. They provide feedback and suggestions for design improvements if necessary.
- Casting Simulation: Using advanced casting simulation software, the manufacturer can simulate the casting process to predict potential defects, optimize gating and riser systems, and ensure optimal casting quality.
2. Pattern and Mold Production:
- Pattern Making: Once the design is finalized, the manufacturer proceeds with pattern making. Depending on the complexity of the component and the desired quantity, patterns can be 3D printed, machined, or created using traditional methods.
- Mold Making: The sand casting manufacturer prepares the molds based on the patterns. The molding process may involve preparing green sand molds, shell molds, or other types of molds depending on the casting requirements.
3. Casting Production:
- Metal Melting and Pouring: The sand casting manufacturer melts the chosen metal or alloy to the required temperature and pours it into the prepared mold.
- Cooling and Solidification: The molten metal is left to cool and solidify in the mold. Proper cooling rates and control over solidification are crucial to ensure sound castings.
4. Post-Casting Operations:
- Cleaning and Finishing: After the casting has cooled, the sand casting manufacturer removes the casting from the mold, cleans it, and removes any excess material or gating system.
- Inspection and Quality Assurance: The casting undergoes thorough inspection to ensure it meets the specified quality standards. Non-destructive testing, dimensional checks, and visual inspection are common quality assurance measures.
5. Delivery and Feedback:
- Delivery: Once the castings pass inspection, the sand casting manufacturer prepares the components for shipment and delivers them to the customer according to the agreed-upon schedule.
- Feedback and Continuous Improvement: A collaborative process includes an open channel of communication between the customer and the manufacturer. Any feedback or lessons learned from the project are shared to foster continuous improvement for future collaborations.
Throughout the collaborative process, effective communication, timely updates, and a mutual understanding of project goals are essential for a successful partnership between the sand casting manufacturer and the customer. By working together closely, the manufacturer can efficiently meet the customer’s requirements, optimize the casting process, and deliver high-quality cast components.