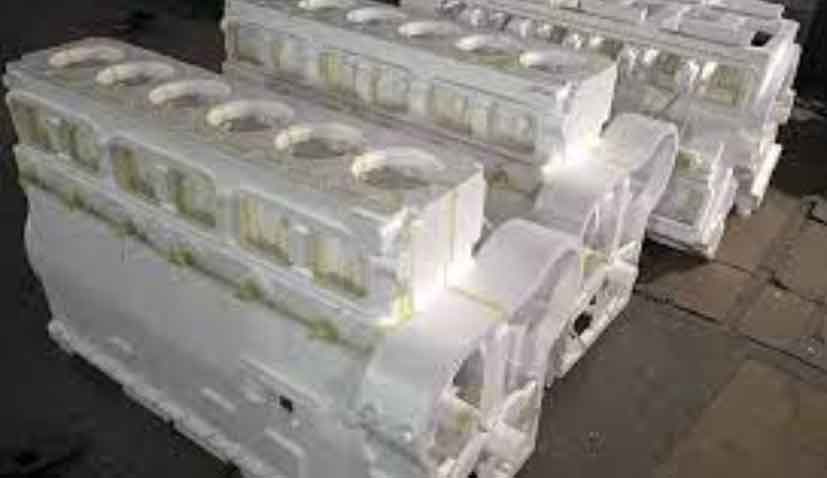
Lost foam casting offers several advantages in modern manufacturing processes, making it a preferred choice for certain applications. These advantages stem from its ability to produce complex, near net shape castings with high precision and efficiency. Here are some key advantages of lost foam casting in modern manufacturing:
1. Design Flexibility:
- Lost foam casting allows for intricate and complex designs that are challenging to achieve with other casting methods. The foam patterns can be easily shaped and manipulated, providing greater design freedom and enabling the production of parts with intricate geometries.
2. Near Net Shape Casting:
- Lost foam casting produces near net shape castings, which reduces the need for extensive post-casting machining and finishing operations. This results in significant material and cost savings.
3. Dimensional Accuracy:
- Lost foam casting offers high dimensional accuracy, as the foam pattern maintains its shape during the casting process. This results in precise and consistent castings, reducing the need for additional dimensional corrections.
4. Smooth Surface Finish:
- Lost foam castings typically have a smooth surface finish, reducing the need for additional surface treatments or polishing.
5. Reduction in Tooling Costs:
- Lost foam casting eliminates the need for complex and expensive dies or patterns used in other casting methods. This significantly reduces tooling costs, making it a cost-effective option for small to medium production runs.
6. Complexity of Assemblies:
- Lost foam casting allows for the integration of multiple components into a single casting, reducing the need for assembly processes and potential points of failure. This simplifies the overall assembly process and enhances product integrity.
7. Increased Productivity:
- Lost foam casting can be a more rapid and efficient process compared to traditional casting methods. The elimination of pattern removal and cleaning steps in the casting process reduces cycle times and increases productivity.
8. Material Savings and Environmental Benefits:
- The foam patterns used in lost foam casting are expendable and can be easily recycled or reused, minimizing material waste. This promotes sustainable practices and reduces the environmental impact of casting operations.
9. Versatility of Materials:
- Lost foam casting can be used with a wide range of materials, including various metals and alloys, providing versatility in material selection for different industrial applications.
10. Reduction in Part Weight:
- Lost foam casting can be used to produce lightweight parts with thinner walls, reducing overall part weight and making it suitable for applications where weight reduction is crucial, such as in automotive and aerospace industries.
Due to these advantages, lost foam casting is commonly used in industries like automotive, aerospace, marine, and general engineering, where complexity, precision, and cost-effectiveness are critical factors. As modern manufacturing continues to evolve, lost foam casting is expected to play an increasingly significant role in the production of intricate and high-quality castings.