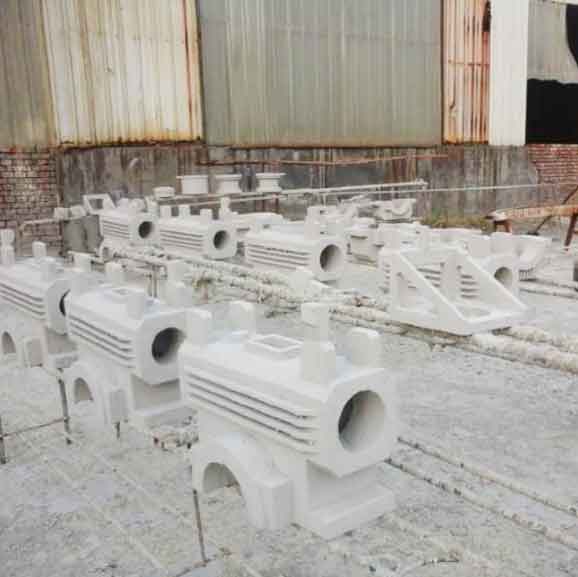
The lost foam casting process, also known as evaporative pattern casting, involves transforming foam patterns into metal parts. It is a unique and efficient method for producing complex and intricately shaped components. Let’s explore the steps involved in the lost foam casting process:
1. Pattern Creation:
The process begins with the creation of foam patterns. These patterns are made by shaping expandable polystyrene (EPS) foam blocks using various cutting and shaping techniques. The foam patterns replicate the shape and features of the desired final metal parts. Complex geometries, undercuts, and fine details can be easily achieved with foam patterns.
2. Cluster Assembly:
Multiple foam patterns, known as a cluster, are assembled together using a gating system. The gating system consists of sprue, runners, and gates that facilitate the flow of molten metal into the mold cavity. The foam patterns are connected to the gating system using foam or adhesive materials, ensuring proper alignment and stability during the casting process.
3. Pattern Coating:
The foam patterns are coated with a refractory material to enhance their heat resistance and create a barrier between the foam and the molten metal. The refractory material, typically a ceramic or silica-based slurry, is applied to the foam cluster through dipping, spraying, or brushing. The coating is dried and hardened to form a refractory shell around the foam patterns.
4. Molding:
The coated foam cluster is embedded in unbonded sand or a mixture of sand and binder, known as the mold. The mold provides support to the foam patterns during the casting process and forms the outer shape of the final metal part. The sand is compacted around the foam cluster, ensuring proper contact and minimizing movement during metal pouring.
5. Foam Removal:
The assembled mold with the foam cluster is subjected to preheating, which causes the foam patterns to vaporize. The heat from the molten metal poured into the mold later replaces the evaporated foam. As the foam evaporates, it leaves behind a cavity that corresponds to the desired shape of the final metal part. The mold is heated until the foam is completely removed, leaving only the mold cavity.
6. Metal Pouring:
Once the foam is removed, the mold is securely closed and prepared for metal pouring. Molten metal, usually aluminum, is poured into the mold at a controlled rate and temperature. The metal fills the cavity created by the foam patterns, ensuring that it completely replicates the desired shape and features. The molten metal displaces the air and fills the mold cavity, effectively taking the shape of the foam patterns.
7. Solidification and Cooling:
After metal pouring, the molten metal undergoes solidification and cooling within the mold. The metal solidifies, gradually taking on the final solid form of the component. The cooling process is carefully controlled to avoid defects and ensure proper metallurgical properties. The solidification time depends on the size and complexity of the component.
8. Shakeout and Finishing:
Once the metal has solidified and cooled, the mold is removed, and the casting is shaken out. Excess sand and any residual materials are removed from the casting through various cleaning methods, such as shot blasting or mechanical cleaning. The casting may undergo additional finishing processes like machining, grinding, heat treatment, and surface treatments to achieve the desired dimensional accuracy, surface quality, and mechanical properties.
The lost foam casting process allows for the efficient and precise production of complex metal components. It eliminates the need for traditional patterns, cores, and assembly operations, reducing production time, costs, and potential errors. The versatility of foam patterns and the ability to create intricate designs make lost foam casting suitable for a wide range of applications in industries such as automotive, aerospace, and machinery manufacturing.