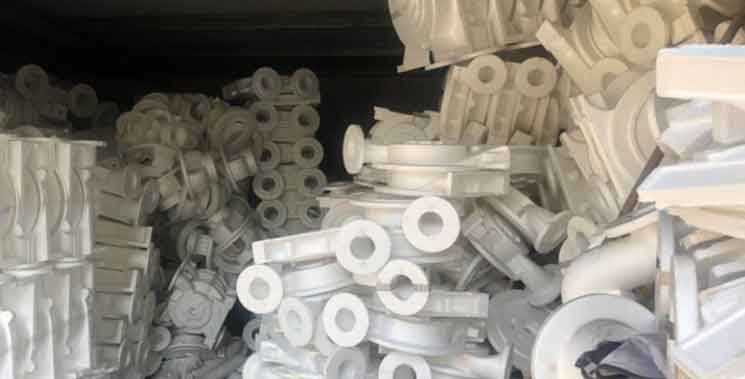
Lost foam casting is a unique and innovative casting process that involves the transformation of a foam pattern into a metal component. Here’s a step-by-step overview of the lost foam casting process:
- Pattern Creation: The process begins with the creation of a foam pattern that represents the desired shape and features of the final metal component. The foam pattern can be produced using various techniques, including CNC machining, 3D printing, or by manually shaping the foam material. The foam pattern is typically made from expandable polystyrene (EPS), which can be easily shaped and has excellent dimensional stability.
- Pattern Assembly: Once the foam pattern is created, it is assembled with other foam patterns if multiple components are required or with gating and riser systems. The foam patterns are securely attached to a sprue, which serves as the pathway for the molten metal to flow into the mold. The assembled foam patterns are then coated with a refractory material to create a shell.
- Mold Preparation: The coated foam pattern assembly is placed in a flask or a casting flask. The flask is filled with unbonded sand, which surrounds the coated foam pattern assembly and supports it during the casting process. The sand used in lost foam casting is typically a mixture of silica sand and a binder, which provides cohesion and allows for easy mold creation.
- Mold Compaction: Once the flask is filled with sand, it is compacted using vibration or other compaction methods. The compaction ensures that the sand is tightly packed around the foam pattern assembly, providing support and maintaining the shape of the mold.
- Foam Pattern Removal: The flask with the compacted sand is then inverted or turned upside down, allowing gravity to assist in the removal of the foam pattern. The heat from the molten metal will vaporize the foam pattern, leaving behind a cavity in the shape of the pattern within the compacted sand mold.
- Metal Pouring: The prepared mold is then preheated to remove any residual moisture and ensure that it can withstand the temperature of the molten metal. Once the mold is heated, the molten metal is poured into the mold through the sprue. The molten metal flows through the pathways created by the foam pattern and fills the cavity left by the vaporized foam pattern.
- Solidification and Cooling: After the metal is poured, it solidifies and cools within the mold. The solidification time depends on the type of metal being used and its specific solidification characteristics. Once the metal has fully solidified and cooled, the mold is opened, and the metal component is removed.
- Finishing Operations: Depending on the required specifications of the final component, various finishing operations may be performed. This can include removing excess material, surface cleaning, machining, heat treatment, and any necessary surface treatments or coatings.
The lost foam casting process offers several advantages, including the ability to produce complex shapes, near-net shape components, and the elimination of the need for complex molds and cores. It is widely used in industries such as automotive, aerospace, machinery, and art, where intricate designs and complex geometries are required.