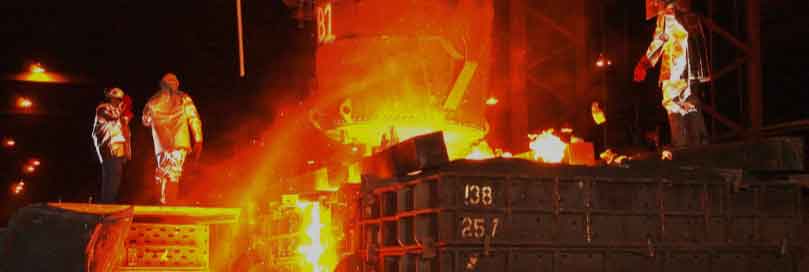
Sand casting is a fascinating blend of art and science, combining the artistic creation of patterns and molds with the scientific principles of material properties, solidification, and manufacturing processes. Let’s explore the art and science behind sand casting.
The Art of Sand Casting
- Pattern Design: The artistry of sand casting begins with pattern design. Skilled pattern makers create intricate patterns that replicate the desired final part, considering factors such as shrinkage allowances, draft angles, and gating systems. They combine technical expertise with artistic craftsmanship to produce patterns that capture the essence of the intended design.
- Mold Making: Creating the sand molds is another artistic aspect of sand casting. Mold makers pack special molding sand around the pattern to form the mold cavity. They carefully craft the molds, ensuring proper alignment, surface finish, and venting to facilitate the flow of molten metal and the escape of gases during casting.
- Pattern Removal: The process of removing the pattern from the sand mold requires finesse and attention to detail. Skilled craftsmen delicately extract the pattern, leaving behind a clean and precise mold cavity. This step requires craftsmanship to avoid damaging the mold and to achieve the desired surface finish and dimensional accuracy.
- Finishing: Sand castings often require post-casting finishing operations to refine the surface finish and achieve the desired appearance. This may involve grinding, sanding, polishing, or other techniques to remove any imperfections and create a visually appealing final product.
The Science of Sand Casting
- Material Selection: The science of sand casting begins with selecting the appropriate material for the casting. Factors such as mechanical properties, heat resistance, corrosion resistance, and cost are considered to ensure the chosen material meets the functional requirements of the part.
- Solidification: The solidification process of molten metal is a critical scientific aspect of sand casting. Understanding the solidification behavior of the chosen material is crucial to avoid defects such as shrinkage, porosity, or cracks. Proper gating and risering design, along with cooling techniques, are employed to control the solidification process and minimize the occurrence of defects.
- Material Behavior: Sand casting relies on an understanding of material behavior during casting and subsequent cooling. Knowledge of how the molten metal interacts with the sand mold, how it fills the cavity, and how it solidifies allows for the creation of high-quality castings with accurate dimensions, sound structure, and desirable properties.
- Process Control: Scientific principles guide process control in sand casting. Parameters such as pouring temperature, pouring rate, mold preheating, and cooling time are carefully controlled to ensure consistent results and minimize the risk of defects. The use of advanced techniques like computer simulations and modeling aids in optimizing the casting process and predicting potential issues.
- Quality Assurance: Science plays a vital role in quality assurance in sand casting. Non-destructive testing methods such as X-ray, ultrasonic testing, and visual inspection are employed to detect and analyze any defects or flaws in the castings. Material testing and analysis help verify the mechanical properties and ensure compliance with specifications.
The Art-Science Synergy
The successful implementation of sand casting relies on the seamless integration of artistry and scientific principles. Skilled artisans bring creative vision and craftsmanship to the pattern design and mold making, while scientific understanding guides material selection, solidification control, and quality assurance. The artistry brings life to the design, while the science ensures the reliability and functionality of the castings.
The collaboration between artists, engineers, metallurgists, and technicians brings out the best in both the art and science of sand casting, resulting in beautifully crafted and structurally sound metal parts. This harmonious blend is what makes sand casting a captivating and enduring process in the world of manufacturing.