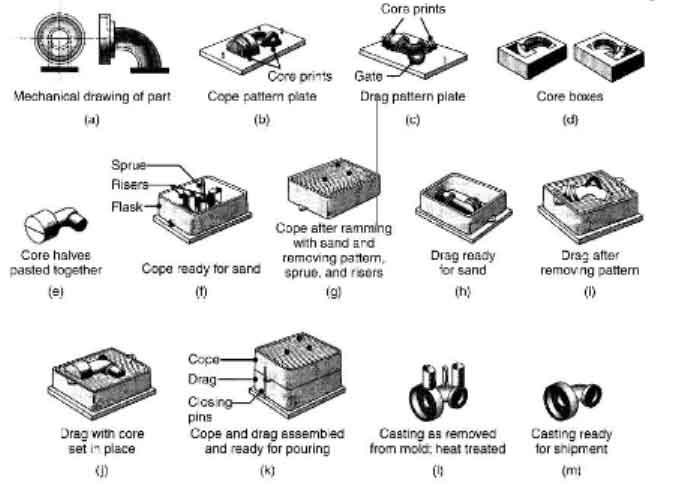
The sand casting process is a versatile and widely used method for producing metal components. It involves several distinct stages, each contributing to the creation of a solid metal part. Let’s explore the steps involved in the sand casting process:
Pattern Making:
The process begins with the creation of a pattern, which is a replica of the desired part. The pattern is typically made from wood, plastic, or metal and is designed to accommodate the necessary shrinkage and draft angles. Skilled pattern makers carefully craft the pattern to ensure it captures all the intricate details of the final part.
Mold Preparation:
The pattern is used to create a mold cavity in which the molten metal will be poured. Molding sand, which is typically a mixture of silica sand and additives, is packed around the pattern to form the mold. The molding sand is compacted and shaped using various tools and techniques to create a precise and uniform mold cavity.
Core Production (If Required):
In some cases, the part may require internal cavities or complex shapes that cannot be achieved solely with the mold. In such instances, sand cores are produced. Cores are made from specially formulated sand mixes that are compacted in core boxes and then placed inside the mold to form the desired internal features.
Mold Assembly:
Once the mold cavity and cores are prepared, they are assembled, ensuring proper alignment and the formation of gating and riser systems. The gating system consists of channels that allow the molten metal to flow into the mold cavity, while the risers provide a reservoir of molten metal to compensate for shrinkage during solidification.
Melting and Pouring:
The chosen metal alloy is melted in a furnace at the appropriate temperature. Once the metal reaches the desired molten state, it is poured into the mold cavity through the gating system. Proper pouring techniques, such as controlling the pouring rate and avoiding turbulence, are crucial to ensure a smooth and defect-free fill.
Solidification and Cooling:
After the molten metal is poured, it begins to solidify within the mold cavity. The solidification process is influenced by factors such as the metal alloy, mold material, and cooling rate. Controlled cooling allows the metal to solidify gradually, ensuring the formation of a sound and structurally sound casting.
Shakeout and Cleaning:
Once the casting has solidified and cooled, the mold is broken apart through a process called shakeout. The casting is then removed from the sand and cleaned to remove any residual sand, gating material, or other debris. Various methods, such as mechanical cleaning, shot blasting, or chemical cleaning, may be employed to achieve the desired surface finish.
Finishing Operations:
After cleaning, the casting may undergo additional finishing operations to achieve the desired surface quality, dimensional accuracy, and functional properties. These operations can include grinding, machining, heat treatment, coating, or any other required processes.
Inspection and Quality Control:
The final step involves inspecting the casting to ensure it meets the required specifications and quality standards. Dimensional measurements, visual inspection, non-destructive testing, and metallurgical analysis may be performed to verify the integrity, surface finish, and mechanical properties of the casting.
The sand casting process offers flexibility, allowing for the production of a wide range of complex parts in various sizes and metal alloys. It remains a popular choice in many industries due to its versatility, cost-effectiveness, and ability to accommodate both prototype development and high-volume production.