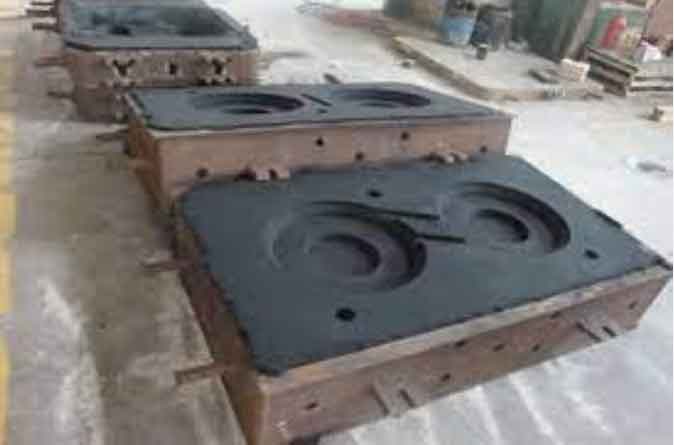
Furan sand casting is a common technique used in precision metal fabrication and foundry processes. It involves using furan resin as a binder to create sand molds for casting metal parts. Furan sand casting offers several advantages over traditional sand casting methods, including improved dimensional accuracy, surface finish, and overall casting quality. Here are some advanced techniques associated with furan sand casting:
- Mold Design and Preparation: Advanced techniques in mold design and preparation play a crucial role in achieving precision in metal fabrication. Computer-aided design (CAD) software is often used to create intricate and complex mold designs. Simulation software can also be employed to optimize the mold filling and solidification processes, ensuring better casting outcomes.
- Pattern Production: Patterns are used to create the impression in the sand molds. Advanced techniques, such as computer numerical control (CNC) machining and 3D printing, can be utilized to produce highly accurate and intricate patterns. These technologies enable the creation of complex geometries with precision and repeatability.
- Sand Preparation: The quality of the sand used in furan sand casting greatly affects the final casting quality. Advanced techniques for sand preparation include sand conditioning and optimization of the sand mixture. Sand conditioning involves controlling the moisture content and temperature of the sand, ensuring consistent properties. Optimizing the sand mixture involves adjusting the grain size distribution and binder-to-sand ratio to achieve the desired properties and mold strength.
- Molding Process: Advanced molding techniques involve precise control over the mold filling and compaction processes. This can be achieved through automated molding lines that provide consistent and controlled filling and compaction of the sand molds. The use of vibratory compaction and squeeze molding techniques helps to improve mold density and reduce defects, resulting in better casting quality.
- Casting Process: Advanced techniques in the casting process include the use of sophisticated pouring systems and gating designs. These techniques facilitate controlled metal flow and minimize turbulence, which can lead to defects like porosity and inclusions. Proper gating design ensures uniform filling of the mold and reduces the likelihood of defects such as shrinkage.
- Casting Solidification and Cooling: Advanced techniques focus on optimizing the solidification and cooling processes to prevent defects and improve dimensional accuracy. Simulation software can be used to predict solidification patterns and optimize the placement of chills or cooling elements to control solidification rates and minimize residual stresses.
- Quality Control and Inspection: Advanced techniques in quality control involve the use of non-destructive testing methods such as X-ray, ultrasound, and 3D scanning. These techniques allow for the detection of internal defects without damaging the casting. Additionally, dimensional inspection using coordinate measuring machines (CMM) ensures adherence to tight tolerances.
By implementing these advanced techniques in furan sand casting, precision metal fabrication can be achieved, resulting in high-quality castings with accurate dimensions, excellent surface finish, and reduced defects.