Based on the above comprehensive evaluation of the casting process plan, the casting simulation software is used to simulate the casting and solidification process after modeling, and various boundary conditions and heat transfer coefficients are set according to the actual conditions. There are many inner sand cores, and the higher pouring temperature is conducive to the gas escape. The pouring temperature is controlled at 1440 ℃~1400 ℃, except for the sand cores, the clay sand is set, and the heat transfer coefficient between the ductile iron castings and the sand mold is defined as 500 W/(m2 · K), The outside of the sand mold is set with air cooling, the pouring time is controlled for 10 s, the pouring speed is 3.5 kg/s, and the number of grids is 50200.
1) Filling simulation
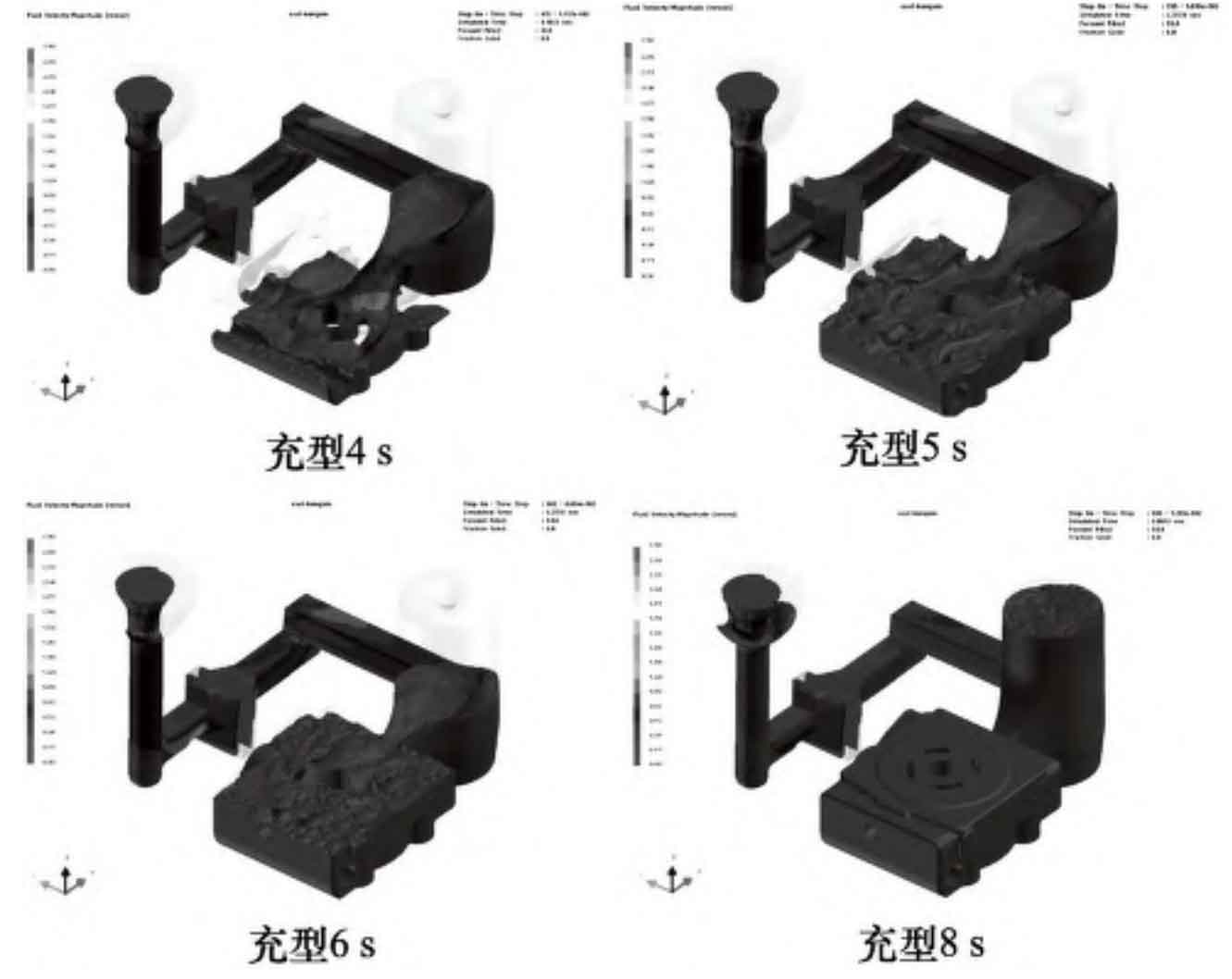
Fig. 1 Distribution of filling velocity field, analysis of the cloud chart of the filling process of molten iron, the maximum velocity of the drop when the molten iron initially enters the mold cavity is between 0.85 and 1 m/s. Since the pouring system is open, the average filling velocity is between 0.3 and 0.5 m/s, the whole filling process is free of molten iron scouring the sand core, splashing and eddy current, and the flow beam is free of major disturbance. After entering the open rear transverse runner, it is obvious that the pressure value is significantly reduced, and then the molten iron enters the cavity of ductile iron castings from four internal gates. The pressure value remains stable from the beginning of filling to filling the entire cavity, and the filling process is stable without obvious injection and a large amount of turbulence. Fig. 2 Analysis of air entrainment during mold filling process shows that the liquid level rises steadily during mold filling, the cavity air is discharged smoothly, and the air does not collect in the dead corner or inside the molten iron. By simulating the filling process of molten iron in the pump cover and analyzing the simulation results, the open gating system is stable and free of obvious turbulence, air entrainment and entrapment, and the gating system is feasible.
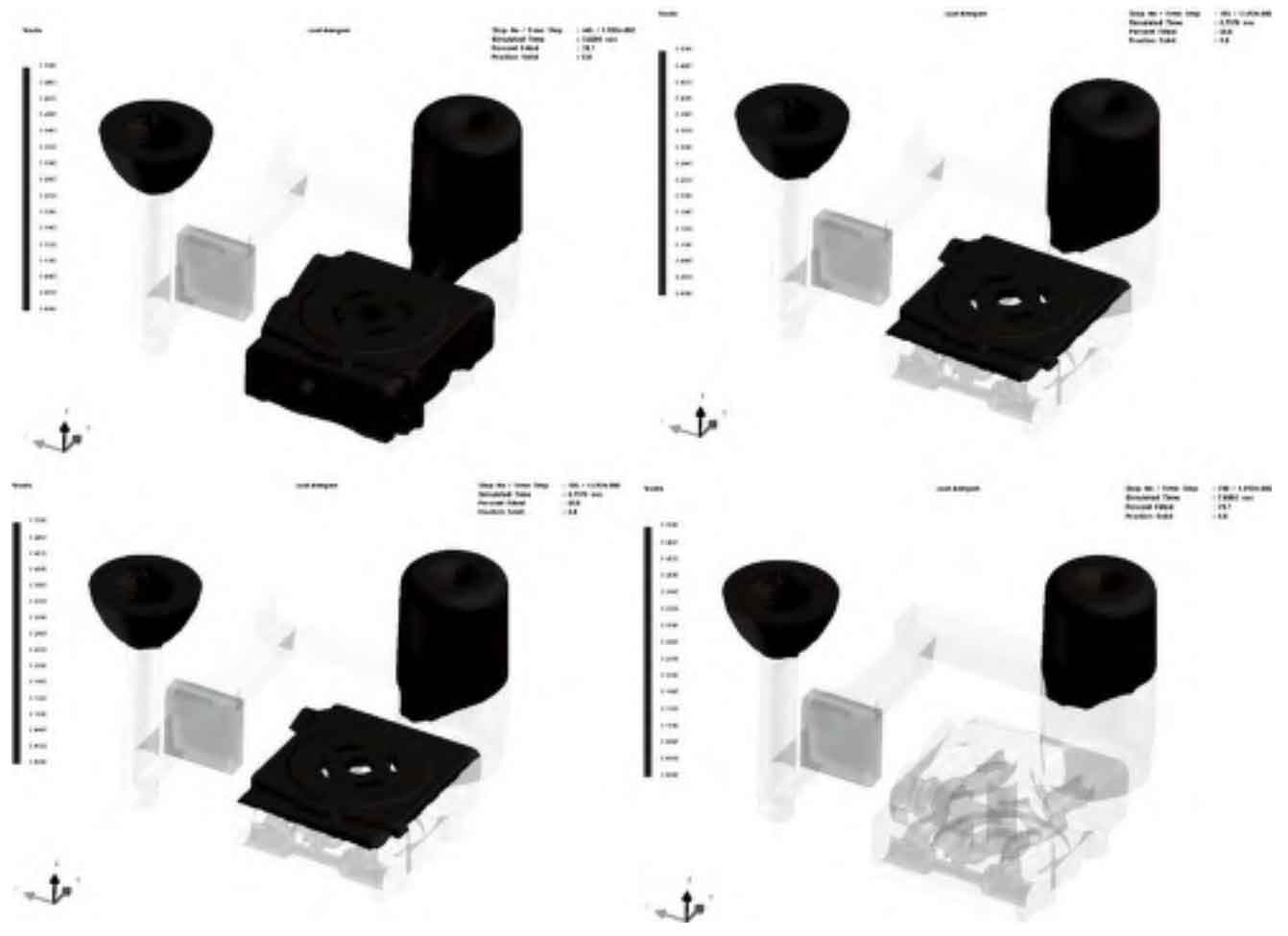
2) Solidification simulation

In this casting process, feeding system is designed to control sequential solidification. Fig. 3 Solidification volume distribution. The pouring system first cools and solidifies, then the nodular cast iron solidifies from the edge to the center, and finally the liquid phase zone completely enters the riser body, realizing the sequential solidification. Fig. 4 Solidification temperature distribution and shrinkage distribution. The solidification temperature field proves that the riser finally solidifies, and finally simulates that there is no distribution in the shrinkage casting.
