Gravity casting is a casting method that uses the gravity of the molten alloy to supplement the shrinkage during the casting process. Through this casting method, the molten alloy at the relatively lagging solidification position can supplement the gap caused by the hot expansion and cold shrinkage of the previously solidified alloy, and finally the shrinkage cavity, porosity and other defects in the casting process are concentrated at the last solidified riser position, so as to ensure the quality of the product.
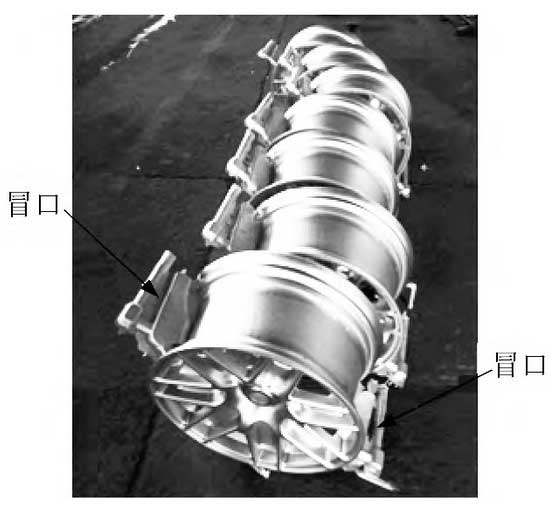
The figure shows the aluminum alloy hub casting blank cast by bilateral gravity. It can be seen clearly from the figure that the riser located at two protruding points of the hub, and the riser accounts for a large proportion of the whole hub casting blank. Although a lot of alloy is wasted, such reserved riser is reasonable compared with ensuring the quality of the hub.
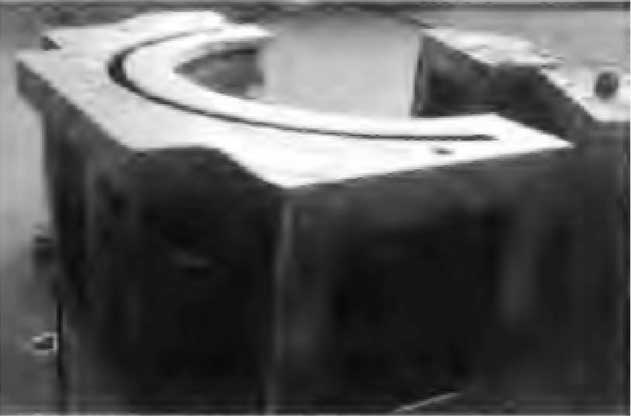
Nowadays, gravity casting is a relatively backward production technology, but because of its short casting time, relatively cheap equipment and mold, the production process is simple and low production cost, and it still has a certain position in the automobile hub production industry in China. Therefore, in order to make gravity casting develop its advantages and avoid its disadvantages, scholars have conducted in-depth research. Ma Ying et al. [5] used CAE technology, This paper analyzes the problem of aluminum leakage on one side of the gate caused by the deformation of the side mold under the action of thermal stress when the side mold is heated during casting. It is found that an empty groove is set at the rib plate of the side mold to separate it from the rotary surface of the cavity, and the side mold will not deform, which basically solves the problem of aluminum leakage, as shown in the figure.