The filling process of lost foam casting has a decisive influence on the quality of castings. Due to the existence of foam pattern, gasification decomposition and the interaction between decomposition products and molten metal, the filling process of molten metal and the generation and control of casting defects are extremely complex. For example, it is difficult to obtain high-quality castings under the guidance of ordinary sand mold casting process theory. Therefore, studying the influence laws of flow field, temperature field, mold filling capacity, pattern properties, coating and other factors in the liquid metal filling process of lost foam casting is an important topic in the basic theory of dry sand lost foam casting, which is the basic principle and applicable formula for determining the pouring scheme, The formation mechanism of defects and the prevention and elimination measures are of great significance.
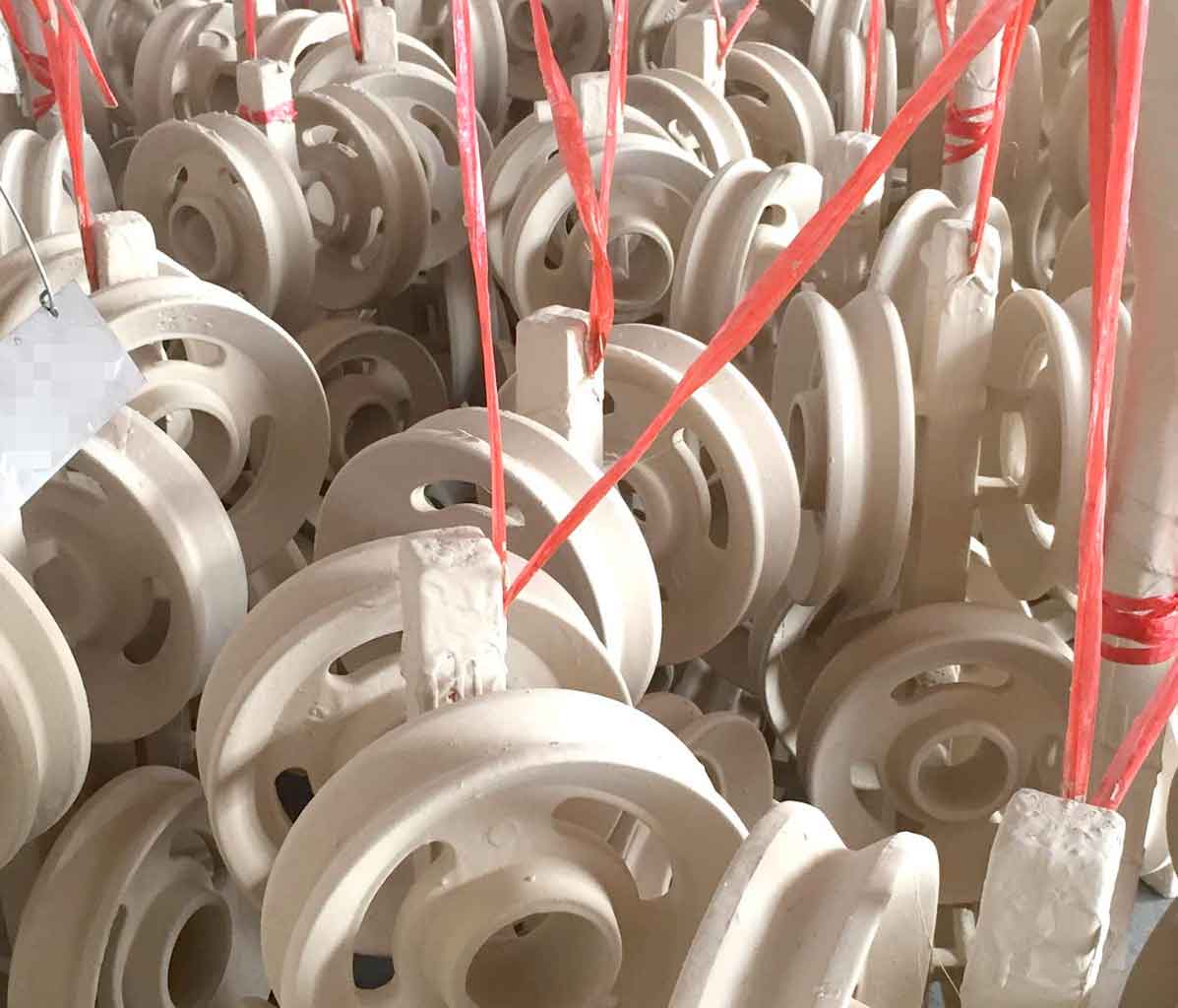
Although the lost foam casting process of iron castings has been well used in industrial production, the understanding of its filling process law is far from clear, and in terms of theoretical development, it is still far behind the practical engineering field, because most of the casting problems were initially considered as technical problems rather than scientific problems. Compared with ordinary cavity casting, there are many and complex factors affecting the filling process of lost foam casting. These factors usually include vacuum degree, pattern density, coating permeability, pouring temperature, liquid metal static head, inner gate size, pouring position, top pouring, bottom pouring or step pouring, pattern geometry, molding sand permeability, etc. The interaction of these factors will have a complex impact on the filling process of lost foam casting. To study the influence of these factors and their interaction on the filling process of lost foam casting in detail, it often requires a lot of manpower, funds and equipment investment.
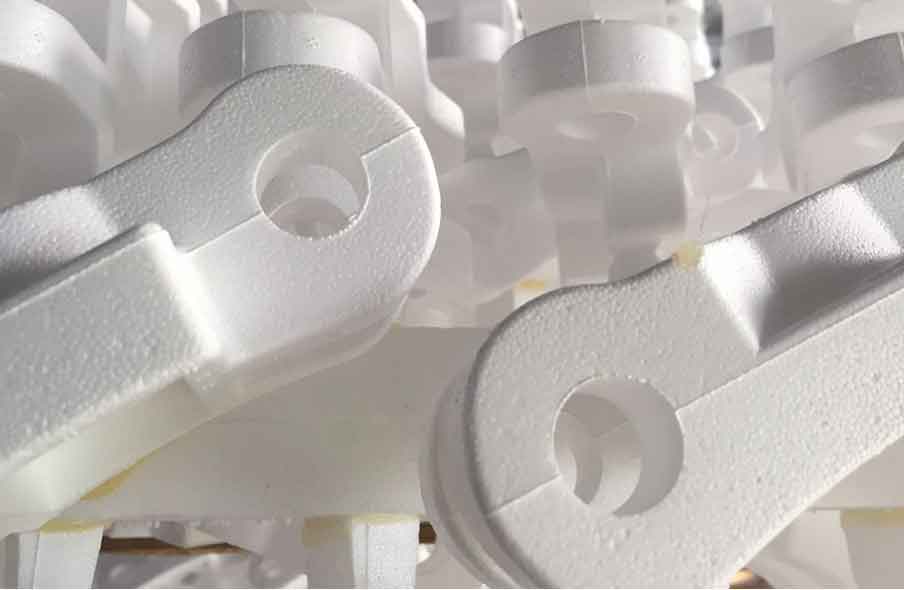
At present, the experimental research results of lost foam casting filling process are mainly focused on aluminum alloy, and the factors studied are often limited to pouring temperature, pouring position, coating permeability, liquid metal static head, etc., while for the experimental test of lost foam casting filling process of iron castings, only a few reports have reported the influence of some factors, and the basic principle and applicable formula of pouring scheme have not been determined, At present, the experience of sand casting is still used for reference. According to the characteristics of lost foam casting, some principles of gating system design are put forward. In actual production, the gating system is often selected and calculated according to experiments and experience.