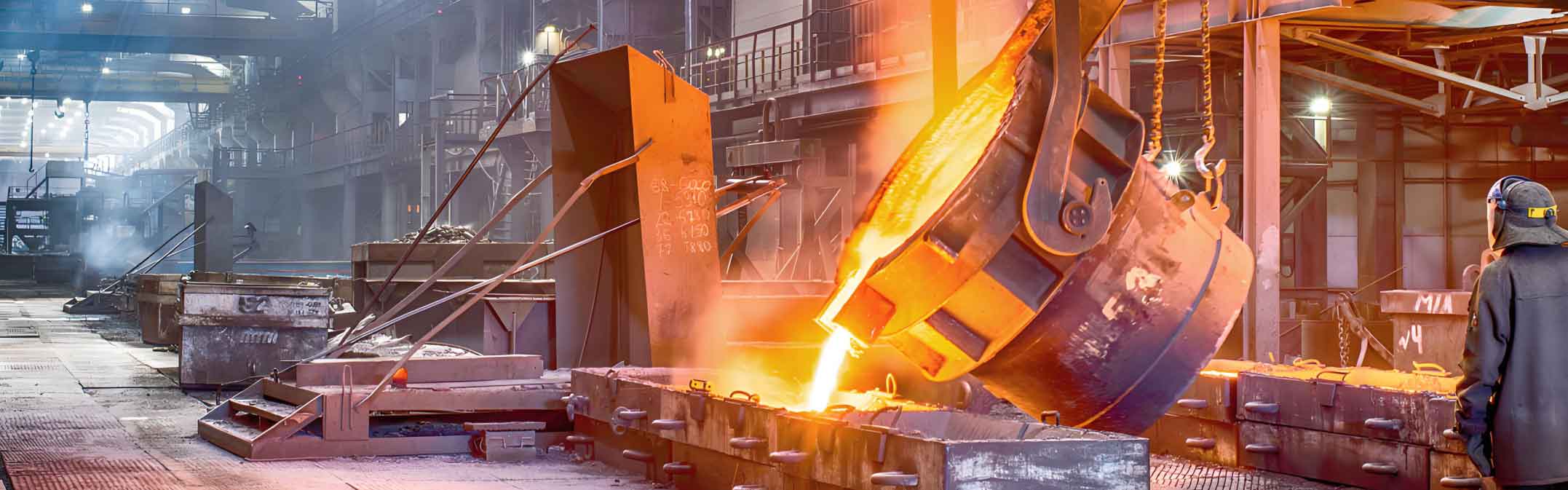
Sand casting is manufacturing process that has been a cornerstone of metal casting for centuries. Its versatility, cost-effectiveness, and ability to produce complex geometries make it a preferred choice in various industries. In recent years, sand casting has found significant applications in the electric vehicle and aerospace industries. This article explores these successful applications, highlighting the benefits and innovations that sand casting brings to these cutting-edge fields.
Sand Casting in the Electric Vehicle Industry
The electric vehicle industry is rapidly evolving, driven by the need for sustainable and efficient transportation solutions. Sand casting plays a crucial role in the production of key components for electric vehicles, offering several advantages such as cost-effectiveness, design flexibility, and the ability to produce complex shapes.
Key Components Produced by Sand Casting
- Motor Housings
- Sand casting is extensively used to manufacture motor housings for electric vehicles. The process allows for the production of intricate designs that are essential for efficient motor performance.
- Battery Enclosures
- Battery enclosures require precision and durability. Sand casting provides the ability to create robust and complex designs that protect the battery and ensure its efficient functioning.
- Chassis Components
- The chassis of an electric vehicle includes various components that can be efficiently produced using sand casting. This includes suspension parts, brackets, and frames.
Benefits of Sand Casting in Electric Vehicle Production
Cost-Effectiveness:
- Sand casting is an economical method, especially for producing large and complex components in low to medium volumes. This is particularly beneficial for electric vehicle manufacturers who need to keep costs down while maintaining high quality.
Design Flexibility:
- Sand casting allows for a high degree of design flexibility. Complex geometries and custom designs can be easily achieved, which is essential for optimizing the performance and efficiency of electric vehicles.
Material Versatility:
- A wide range of materials can be used in sand casting, including aluminum, magnesium, and various alloys. This versatility is crucial for meeting the diverse requirements of electric vehicle components.
Table 1: Commonly Sand Cast Electric Vehicle Components
Component | Material Used | Benefits |
---|---|---|
Motor Housing | Aluminum Alloy | Lightweight, good thermal conductivity |
Battery Enclosure | Magnesium Alloy | Lightweight, high strength-to-weight ratio |
Suspension Parts | Steel Alloy | High strength, durability |
Brackets | Aluminum Alloy | Corrosion resistance, lightweight |
Sand Casting in the Aerospace Industry
The aerospace industry demands precision, reliability, and the ability to withstand extreme conditions. Sand casting meets these requirements, making it an invaluable process for producing critical aerospace components. The ability to create complex and lightweight structures is particularly advantageous in this industry.
Key Aerospace Components Produced by Sand Casting
- Engine Components
- Sand casting is used to produce various engine components such as turbine blades, casings, and brackets. The process ensures that these parts are strong, lightweight, and capable of withstanding high temperatures.
- Structural Components
- Structural components, including frames and supports, are often produced using sand casting. The method allows for the creation of intricate designs that provide the necessary strength and rigidity.
- Landing Gear Components
- Landing gear components must be robust and reliable. Sand casting is used to manufacture these parts, ensuring they meet stringent safety and performance standards.
Benefits of Sand Casting in Aerospace Production
Precision and Accuracy:
- Sand casting allows for high precision and accuracy, essential for aerospace components that must meet strict specifications and tolerances.
Ability to Produce Complex Shapes:
- The process enables the production of complex geometries that are often required in aerospace components. This capability is vital for optimizing performance and reducing weight.
High-Temperature Resistance:
- Components produced by sand casting can withstand high temperatures, which is crucial for parts such as engine components that operate under extreme conditions.
Table 2: Commonly Sand Cast Aerospace Components
Component | Material Used | Benefits |
---|---|---|
Turbine Blades | Nickel Alloy | High temperature resistance, durability |
Engine Casings | Aluminum Alloy | Lightweight, good thermal conductivity |
Landing Gear Parts | Titanium Alloy | High strength, lightweight |
Structural Supports | Steel Alloy | High strength, rigidity |
Innovations in Sand Casting for Electric Vehicle and Aerospace Industries
Advanced Sand Casting Techniques
3D Sand Printing:
- The use of 3D sand printing in sand casting allows for the creation of highly complex molds and cores with exceptional precision. This technique is particularly beneficial for prototyping and low-volume production of intricate parts.
Automated Sand Casting:
- Automation in sand casting enhances efficiency and consistency. Robotic systems can perform repetitive tasks with high precision, reducing the likelihood of defects and improving overall quality.
Material Advancements
High-Performance Alloys:
- The development of high-performance alloys has expanded the capabilities of sand casting. These materials offer superior mechanical properties, making them ideal for demanding applications in electric vehicles and aerospace.
Lightweight Materials:
- The use of lightweight materials such as aluminum and magnesium alloys in sand casting helps reduce the weight of components. This is crucial for improving the efficiency and performance of electric vehicles and aerospace components.
List: Future Trends in Sand Casting
- Increased Use of Simulation Software:
- Simulation software will continue to play a significant role in optimizing sand casting processes. It allows for the prediction and mitigation of potential defects, enhancing the quality of cast components.
- Sustainable Sand Casting Practices:
- The focus on sustainability will drive the adoption of environmentally friendly sand casting practices. This includes recycling sand and reducing waste.
- Integration with Additive Manufacturing:
- Combining sand casting with additive manufacturing techniques will open new possibilities for creating complex and high-performance components.
- Enhanced Quality Control Measures:
- Advanced quality control measures, including real-time monitoring and inspection technologies, will ensure the consistent production of high-quality cast components.
Conclusion
Sand casting remains a vital manufacturing process in the electric vehicle and aerospace industries. Its ability to produce complex geometries, cost-effectiveness, and material versatility make it indispensable for producing key components in these fields. By embracing advanced techniques and materials, sand casting continues to evolve, meeting the stringent demands of modern electric vehicle and aerospace applications. As the industry moves forward, the innovations and trends in sand casting will undoubtedly contribute to the development of more efficient, reliable, and high-performance products.