This article provides a detailed analysis of the GB/T 9439 – 2023 “Grey Iron Castings” standard. It begins with an introduction to the background and importance of the standard, followed by a section-by-section examination of its key aspects, including normative reference documents, grey iron grades, technical requirements, sample preparation, test methods, and inspection rules. The article also compares the new standard with its predecessor, highlighting the changes and their implications. Additionally, it discusses the practical applications and benefits of the standard in the casting industry. Through this comprehensive analysis, readers will gain a deep understanding of the standard and its role in promoting the production and quality improvement of grey iron castings.
1. Introduction
Grey iron castings are widely used in various industries due to their excellent casting properties and cost-effectiveness. The GB/T 9439 standard plays a crucial role in ensuring the quality and performance of grey iron castings. The latest revision, GB/T 9439 – 2023, was introduced to keep pace with the development of the industry and international standards. This article aims to provide a detailed understanding of the new standard and its impact on the casting industry.
1.1 Background of Grey Iron Castings
Grey iron has been a staple in the manufacturing sector for centuries. Its unique combination of properties, such as good machinability, damping capacity, and wear resistance, makes it suitable for a wide range of applications. In recent years, the demand for lightweight and high-strength grey iron castings has increased, driven by the need for energy-efficient and high-performance machinery. This has led to the development of new manufacturing techniques and materials, which in turn have necessitated the update of the relevant standards.
1.2 Importance of the GB/T 9439 Standard
The GB/T 9439 standard serves as a guideline for the production, inspection, and acceptance of grey iron castings in China. It helps to ensure the consistency and quality of products, facilitating trade and communication between manufacturers, suppliers, and customers. Compliance with the standard is essential for companies operating in the casting industry, as it enables them to meet the requirements of various end-users and regulatory bodies.
2. Normative Reference Documents
The new standard lists 19 normative reference documents, which are essential for understanding and implementing the requirements of GB/T 9439 – 2023. These documents cover a wide range of topics, including testing methods, material specifications, and quality control.
2.1 Changes in the List of Reference Documents
Compared to the previous version (GB/T 9439 – 2010), the new standard has made several changes to the list of normative reference documents. Four standards have been deleted, while six new standards have been added. The details of these changes are shown in the following table:
Changes | Standards |
---|---|
Added | GB/T 223.72, GB/T 223.86, GB/T 9443, GB/T 20123, GB/T 38441 |
Deleted | GB/T 231.2, GB/T 231.3, GB/T 7233.1 |
2.2 Significance of the Changes
The addition of new standards reflects the industry’s evolving needs and the adoption of more advanced testing and analysis methods. For example, the new standards related to chemical analysis (GB/T 223.72, GB/T 223.86, and GB/T 20123) provide more accurate and comprehensive ways to determine the composition of grey iron. The deletion of some standards may be due to the obsolescence of certain testing procedures or the consolidation of related requirements into other standards.
3. Grey Iron Grades
The classification of grey iron grades is a fundamental aspect of the standard, as it determines the mechanical and physical properties of the castings.
3.1 Naming and Classification of Grey Iron Grades
The new standard classifies grey iron into two types based on their naming methods: strength grade and hardness grade. There are a total of 14 grades, with 8 grades named by strength and 6 grades named by hardness. The following table shows the correspondence between the grey iron grades in GB/T 9439 and other international standards:
Standard | GB/T 9439 | ISO | EN 1561 | ASTM A48M | JIS G5501 | SAE J431 |
---|---|---|---|---|---|---|
HT100 | ISO 185/JL/100 | EN – GJL – 100 | 100 | – | – | – |
HT150 | ISO 185/JL/150 | EN – GJL – 150 | 150 | FC150 | G9H12 | – |
HT200 | ISO 185/JL/200 | EN – GJL – 200 | 200 | FC200 | G10H18 | – |
HT225 | ISO 185/JL/220 | – | 225 | – | G10H21, G11H18 | – |
HT250 | ISO 185/JL/250 | EN – GJL – 250 | 250 | FC250 | G11H20 | – |
HT275 | ISO 185/JL/275 | – | 275 | – | G12H21, G13H19 | – |
HT300 | ISO 185/JL/300 | EN – GJL – 300 | 300 | FC300 | G13H22 | – |
HT350 | ISO 185/JL/350 | EN – GJL – 350 | 350 | FC350 | G13H24 | – |
HT – HBW155 | ISO 185/JL/HBW155 | EN – GJL – HB155 | – | – | H10 | – |
HT – HBW175 | ISO 185/JL/HBW175 | EN – GJL – HB175 | – | – | H11 | – |
HT – HBW195 | ISO 185/JL/HBW195 | EN – GJL – HB195 | – | – | H13, H14 | – |
HT – HBW215 | ISO 185/JL/HBW215 | EN – GJL – HB215 | – | – | H16 | – |
HT – HBW235 | ISO 185/JL/HBW235 | EN – GJL – HB235 | – | – | H18 | – |
HT – HBW255 | ISO 185/JL/HBW255 | EN – GJL – HB255 | – | – | H20 | – |
3.2 Changes in Grades Based on Strength
For grey iron named by strength grade, the new standard has introduced several significant changes:
3.2.1 Deletion and Transfer of Values
The expected tensile strength Rm(min) values of the casting body have been removed from the main text and placed in Appendix C. This change may affect the way manufacturers and users evaluate the quality of castings, as they need to refer to the appendix for this information.
3.2.2 Addition of Tensile Strength Values
The tensile strength values of side-by-side test bars have been added, which are the same as those of single-cast test bars. This provides an alternative testing method and may offer more flexibility in production and quality control.
3.2.3 Extension of Wall Thickness Range
New wall thickness ranges (2.5 – 5 mm) have been added for HT150 and HT200 grades, along with corresponding tensile strength values. This is in response to the development of new casting technologies that enable the production of thinner-walled castings.
3.2.4 Adjustment of Tensile Strength Limits
Both the maximum and minimum tensile strength values for single-cast and side-by-side test bars have been increased. Additionally, the minimum tensile strength values for some attached casting test blocks have been adjusted, with most values increased by 5 – 10 MPa compared to the previous standard.
3.2.5 Specification of Test Bar Types
The standard now requires the specification of test bar types, with /S for single-cast or side-by-side test bars, /A for attached casting test bars, and /C for body test bars. This helps to clarify the testing methods and ensures consistency in reporting results.
3.2.6 Clarification of Compulsory Values
The maximum and minimum tensile strength values for single-cast and side-by-side test bars are now compulsory. For attached casting test blocks, the tensile strength values can also be made compulsory by mutual agreement between the supplier and the purchaser.
3.2.7 Addition of Grade Application
The application of HT100 has been expanded to include materials requiring high damping and thermal conductivity. This provides more guidance for the selection of grey iron grades in specific applications.
3.3 Changes in Grades Based on Hardness
For grey iron named by hardness grade, the following changes have been made:
3.3.1 Naming Method Revision
The naming method has been updated to comply with GB/T 5612. The new format includes the grey iron code HT, the Brinell hardness symbol HBW, and the maximum hardness value for castings with a wall thickness of 40 – 80 mm.
3.3.2 Extension of Wall Thickness Range
New wall thickness ranges (2.5 – 5 mm) have been added for HT – HBW155 and HT – HBW175 grades, along with corresponding hardness values.
3.3.3 Hardness Difference Specification
The standard now specifies that the Brinell hardness difference at specific locations of the casting should not exceed 40 HBW for mass-produced castings. However, this range can be adjusted by mutual agreement between the supplier and the purchaser.
3.3.4 Deletion of Annotation
An annotation regarding the control of hardness difference within 40 HBW at a specific location agreed upon by the supplier and the purchaser has been removed.
4. Technical Requirements
The technical requirements section of the standard outlines the key parameters and specifications for grey iron castings.
4.1 Changes in Mechanical Property Acceptance Criteria
In the new standard, if the acceptance criteria are not specified in the order agreement, the tensile strength is used as the main acceptance basis. This simplifies the decision-making process for manufacturers and provides a default criterion for quality assessment.
4.2 Promotion of Appendix Contents
Certain content from the notes in the previous standard, such as the relationships between hardness and tensile strength (Appendix B) and between hardness and wall thickness (Appendix C), has been elevated to the main text. This emphasizes the importance of these relationships and makes the information more accessible.
4.3 Sampling Location of Casting Body
The new standard requires that the sampling location of the casting body be mutually agreed upon by the supplier and the purchaser. This replaces the previous provisions and gives more flexibility in determining the sampling location based on the specific requirements of each casting.
4.4 Adjustment of Detection Frequency and Quantity
The detection frequency and quantity of tensile strength and hardness have been moved to the sample preparation section and given a separate subsection. This reorganization highlights the significance of these parameters and allows for more detailed specification.
4.5 Addition of Annotations
Two annotations have been added to explain the factors affecting the performance of the casting body and the influence of sampling location defects on the tensile properties. This provides additional information for users to understand the variability in casting performance.
4.6 Specification of Brinell Hardness Test Conditions
The test conditions for Brinell hardness have been specified as 10/3000, unless otherwise stated. This standardizes the testing method and ensures consistent results.
4.7 Emphasis on Hardness Requirements
The content related to the classification of hardness grades and the inapplicability of hardness grading for castings with a wall thickness greater than or equal to 80 mm has been moved from the notes to the main text. This reflects the increasing importance of hardness control in the casting industry.
4.8 Revision of Hardness Detection Location
The hardness detection location is now determined by mutual agreement between the supplier and the purchaser and should be specified in the order agreement. Hardness can also be detected on the sample. This change provides more clarity and flexibility in hardness testing.
4.9 Unification of Hardness Acceptance Rules
The hardness acceptance rules in the new standard are the same for both the casting body and single-cast test bars, regardless of the test bar type. This simplifies the acceptance process and reduces confusion.
4.10 Revision of Metallographic Structure Requirements
The metallographic structure requirements have been revised to specify that the graphite morphology of grey iron castings should be mainly type A, with a content greater than 90%, and the total amount of carbides and phosphide eutectic should be less than 1%. This provides a more specific and quantitative guideline for the microstructure of grey iron castings.
4.11 Deletion of Surface Quality and Special Requirements
The requirements for surface quality and special requirements in the previous standard have been deleted. The surface protection, packaging, and storage requirements are now covered in other sections of the standard, and nondestructive testing is made mandatory.
5. Sample Preparation
Proper sample preparation is crucial for obtaining accurate test results and ensuring the quality of grey iron castings.
5.1 Marking of Test Bars
All test bars are now required to be clearly marked for traceability. This helps to identify the origin and processing history of each test bar, which is essential for quality control and problem-solving.
5.2 Selection of Sample Types
The selection of sample types (single-cast test bars, side-by-side test bars, attached casting test blocks, and body samples) should be based on the weight and wall thickness of the casting. If not specified by the purchaser, the supplier can determine the sample type. This provides a more systematic approach to sample selection.
5.3 Revision of Conditions for Using Attached Casting Test Blocks
The conditions for using attached casting test blocks have been revised. The weight requirement has been reduced from 2000 kg to 1000 kg, while the main wall thickness requirement has been increased from over 20 mm to over 50 mm. This change reflects the optimization of testing methods based on practical experience.
5.4 Changes in Single-Cast Test Bars
Several changes have been made to single-cast test bars:
- Three new size specifications (types I, III, and IV) have been added, in addition to the existing type II. The size of the test bars should correspond to the main wall thickness of the casting.
- The minimum sand consumption between single-cast test bars has been reduced from 50 mm to 40 mm.
- The dimensions of the samples processed from single-cast test bars and the body samples have been integrated into a single table, with the boldfaced values indicating the preferred dimensions.
5.5 Sampling Requirements for Side-by-Side Test Bars
Side-by-side test bars should be poured at the end of the same batch of castings and represent castings with similar main wall thicknesses. Their dimensions are shown in Figure 1. This sampling method helps to ensure the representativeness of the test results.
5.6 Deletion of Hardness Testing on Single-Cast Test Bars
The option of testing hardness on single-cast test bars has been deleted. Instead, hardness test blocks are used for castings with a wall thickness of not less than 20 mm. The hardness value is measured on the ground surface of the test block after cutting. This change may affect the testing process and the correlation between hardness and other properties.
6. Test Methods
Accurate test methods are essential for evaluating the quality and performance of grey iron castings.
6.1 Changes in Tensile Test Samples
The tensile test samples have two types, A and B, with the following changes compared to the previous standard:
- The minimum thread length and the total length of the A-type threaded clamping end sample have been increased.
- The minimum length of the cylindrical clamping end has been significantly reduced for most sizes.
- The diameter of the cylindrical clamping end has been slightly increased.
- The sample thread type has been changed from M28 to M30, with minor adjustments.
- The parallel section length of the B-type sample has been slightly modified.
- The surface roughness of the sample parallel section has been improved from Ra 3.2 μm to Ra 1.6 μm, while the previous standard’s Ra 6.3 μm is no longer required. However, the surface roughness notation still follows the old GB/T 131 – 1993 standard.
6.2 Hardness Testing Method
The hardness testing method is now in accordance with GB/T 231.1, with the deletion of GB/T 231.2 and GB/T 231.3. The standard also recommends using a hardness test with a test force-ball diameter square ratio of 30 or 10, preferably under the 10/3000 or 10/1000 test conditions. This change standardizes the hardness testing procedure and improves the accuracy and comparability of results.
6.3 Deletion of Heat Treatment and Surface Roughness Requirements
The requirements for heat treatment and surface roughness of castings have been deleted. This may simplify the production process but also requires manufacturers to ensure that the castings meet the performance requirements without relying on these specific parameters.
6.4 Revision of Chemical Composition Analysis Methods
The methods for analyzing the chemical composition of castings have been updated. New standards for sulfur and carbon content determination (GB/T 223.72, GB/T 223.86, and GB/T 20123) have been added, and the spectral chemical analysis method has been revised to GB/T 24234 or GB/T 38441. These changes provide more accurate and comprehensive ways to analyze the chemical composition of grey iron castings.
6.5 Change in Detection Method
The ultrasonic testing method has been replaced with the penetration testing method, which is now required to be carried out in accordance with GB/T 9443. This change may improve the detection of surface and near-surface defects in castings.
6.6 Deletion of Inspection Methods
The inspection methods using an endoscope and ultrasonic testing for the internal defects of castings have been deleted. X-ray testing is now the only method for detecting internal defects, which simplifies the inspection process but may require more advanced equipment.
6.7 Equivalent Test Methods
The standard allows the use of equivalent test methods for determining tensile strength, Brinell hardness, and metallographic structure, provided that they are agreed upon by the supplier and the purchaser. This provides flexibility in testing while ensuring the reliability of the results.
7. Inspection Rules
The inspection rules section of the standard defines the procedures and criteria for inspecting grey iron castings.
7.1 Deletion of Sections
The “Inspection Rights” and “Inspection Location” sections have been deleted. This may simplify the inspection process and reduce potential disputes between the supplier and the purchaser.
7.2 Revision of Batch Division
The batch division has been revised. The maximum weight of a sampling batch is now defined as 2000 kg of castings, and the sampling batch can be adjusted by mutual agreement. This change helps to ensure the representativeness of the samples and the consistency of the inspection results.
7.3 Change in Tensile Strength Test Frequency
The tensile strength test frequency has been changed from “at least one tensile test per sampling batch” to “one tensile test per sampling batch.” This simplifies the testing process while still ensuring the quality of the castings.
7.4 Addition of Hardness Test
A hardness test has been added, which can be carried out on the casting body, tensile test samples, or hardness test blocks. Each sampling batch should undergo one hardness test. This provides a more comprehensive evaluation of the casting quality.
7.5 Preservation of Test Data
Both the new and old standards require the preservation of all original test and inspection records. However, the new standard specifies that the records should be kept for at least five years or as required by the customer. This ensures the traceability and reliability of the test data.
8. Comparison with the Previous Standard
The comparison between GB/T 9439 – 2023 and GB/T 9439 – 2010 reveals significant changes in various aspects of the standard.
8.1 Normative Reference Documents
The new standard has updated the list of normative reference documents, adding six new standards and deleting four old ones. This reflects the industry’s progress and the need for more advanced testing and analysis methods.
8.2 Grey Iron Grades
The classification and naming of grey iron grades have been adjusted. The new standard has added new grades and modified the tensile strength and hardness requirements for some grades. These changes provide more options for users and improve the accuracy of grade classification.
8.3 Technical Requirements
The technical requirements have been revised in many areas, including the acceptance criteria for mechanical properties, the sampling location of the casting body, and the hardness testing method. These changes aim to enhance the quality control and performance evaluation of grey iron castings.
8.4 Sample Preparation
The sample preparation section has seen several changes, such as the marking of test bars, the selection of sample types, and the revision of the conditions for using attached casting test blocks. These changes ensure the representativeness and traceability of the samples.
8.5 Test Methods
The test methods have been updated, with changes in the tensile test samples, hardness testing method, and chemical composition analysis methods. These changes improve the accuracy and reliability of the test results.
8.6 Inspection Rules
The inspection rules have been simplified and optimized, with deletions and revisions in the batch division, test frequency, and data preservation requirements. These changes make the inspection process more efficient and practical.
9. Significance and Impact of the New Standard
The implementation of GB/T 9439 – 2023 has significant implications for the casting industry.
9.1 Quality Improvement
The new standard provides more detailed and accurate requirements for grey iron castings, which helps to improve the quality and consistency of products. This is beneficial for both manufacturers and users, as it reduces the risk of product failure and improves the performance of machinery and equipment.
9.2 International Compatibility
The standard is more in line with international standards, which facilitates the export of grey iron castings and promotes international trade. It also enables domestic manufacturers to better compete in the global market.
9.3 Technological Advancement
The changes in the standard encourage the adoption of new technologies and manufacturing processes. For example, the addition of new testing methods and the modification of sample preparation requirements promote the development and application of advanced casting techniques.
9.4 Industry Standardization
The new standard helps to standardize the production and inspection of grey iron castings, which improves the overall efficiency and competitiveness of the casting industry. It provides a common language and set of rules for manufacturers, suppliers, and customers.
10. Conclusion
GB/T 9439 – 2023 “Grey Iron Castings” is a comprehensive and updated standard that reflects the latest developments in the casting industry. The standard’s changes in various aspects, such as grey iron grades, technical requirements, sample preparation, test methods, and inspection rules, have significant implications for the production and quality control of grey iron castings. By complying with the new standard, manufacturers can improve the quality and performance of their products, enhance their competitiveness in the market, and contribute to the sustainable development of the casting industry. The standard also promotes international trade and cooperation by aligning with international standards. Overall, the implementation of GB/T 9439 – 2023 is essential for the advancement and standardization of the grey iron casting industry.
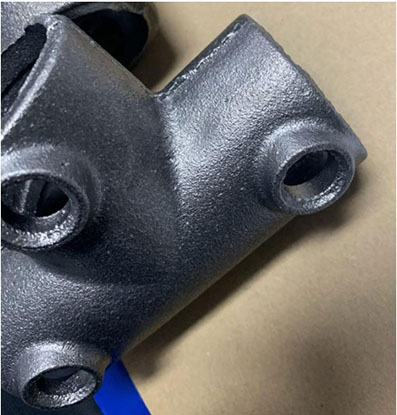