This article focuses on the application of casting elements in the production of automotive brake discs. It begins with an introduction to the importance of brake discs in the automotive braking system and the production base in certain regions of China. Then, it details the characteristics of casting elements, including their composition and advantages over traditional materials like pulverized coal and bentonite. The environmental benefits such as reduced harmful gas and solid emissions are discussed, along with the performance of casting elements in clay sand. Through several case studies of different companies, it illustrates how casting elements improve the production process, reduce defects, and enhance the quality of brake disc castings. Finally, it concludes that casting elements are a green, efficient, and promising material for the casting industry.
1. Introduction
The automotive braking system is a crucial safety component of a vehicle. Brake discs and brake drums are essential parts of this system and are among the iron castings suitable for large-scale sand casting in automotive parts. In China, the regions of Yantai, Longkou, and Laizhou in Shandong are major production bases for automotive brake discs and brake drums. These areas account for over 90% of the total national output in terms of export volume and supply to domestic and foreign main engine factories. The application of casting elements in these production processes has brought significant changes.
2. Casting Elements: An Overview
2.1 Composition and Properties
Casting elements are a new type of material independently developed by Shandong Xuguang Derui High-tech Materials Co., Ltd. and patented in China. It is a mixture for preparing clay sand, consisting of high-quality bentonite, a high-carbon environmentally friendly anti-sand sticking material replacing pulverized coal, α-starch, cellulose, etc. This unique composition gives it distinct properties compared to traditional materials. For example, it has a certain wet pressure strength, thermal wet tensile strength, and specific micro-volatilization and volatile content, as shown in Table 1.
Model | Blue Absorption/(g/100g) | Wet Pressure Strength/kPa | Thermal Wet Tensile Strength/kPa | Micro-volatilization/% | Volatile Content/% | Bright Carbon/% | 140-mesh Passing Rate/% |
---|---|---|---|---|---|---|---|
XZ50 | ≥20 | ≥70 | 2.8 – 3.3 | 10 – 12 | 15 – 23 | 6 – 8 | ≥90 |
XZ60 | ≥22 | ≥80 | 3.0 – 3.5 | 10 – 12 | 14 – 22 | 5 – 7 | ≥90 |
XZ65 | ≥25 | ≥85 | 3.0 – 3.5 | 10 – 12 | 12 – 20 | 4 – 6 | ≥90 |
XZ70 | ≥27 | ≥90 | 3.0 – 3.8 | 10 – 12 | 11 – 19 | 4 – 6 | ≥90 |
XZ75 | ≥28 | ≥95 | 3.2 – 3.8 | 10 – 12 | 10 – 18 | 3 – 5 | ≥90 |
XZ80 | ≥30 | ≥95 | 3.2 – 3.8 | 10 – 12 | 9 – 18 | 3 – 5 | ≥90 |
XZ85 | ≥30 | ≥100 | 3.2 – 3.8 | 10 – 12 | 8 – 16 | 3 – 4 | ≥90 |
Manufacturers recommend the XZ80 model for the production of brake disc and brake drum castings.
2.2 Advantages over Traditional Materials
2.2.1 Environmental Benefits
- Reduced Harmful Gas Emissions: Traditional clay sand preparation using pulverized coal and bentonite often leads to significant emissions of harmful gases. In contrast, casting elements use environmentally friendly high-carbon materials such as polymer polymers and natural plant materials to replace pulverized coal as an anti-sand sticking material. This substitution has significantly reduced air pollution and black pollution in the workshop. Table 2 shows the test results of harmful gas emissions from a company’s casting workshop.
Detection Date | Detection Project | April 17, 2020 | May 20, 2020 |
---|---|---|---|
SO2 | Measured Concentration | 6 | 3 |
Emission Rate | 0.0598 | 0.0301 | |
Toluene | Measured Concentration | 0.064 | 0.048 |
Emission Rate | 0.0006 | 0.0005 | |
etc. | … | … | … |
It is clear that the harmful gas emissions from casting element sand are significantly lower than those from pulverized coal-bentonite clay sand.
- Reduced Solid Emissions: In a casting workshop, sand treatment dust and discarded old sand are major solid emissions. Casting elements have a lower burnout rate of solid powder during high-temperature pouring, reducing the amount of new sand required for adjusting the sand properties and the amount of dust generated during sand treatment. As a result, solid emissions are decreased. For example, a company’s casting workshop using casting elements reduced the amount of auxiliary materials added from 0.74% to 0.44%, and the solid emissions decreased by 80%. The sand composition before and after using casting elements is shown in Table 3.
Material Name | Old Sand/kg | New Sand/kg | Bentonite/kg | Pulverized Coal/kg | Casting Element/kg | Dust Removal Ash/kg |
---|---|---|---|---|---|---|
Original Process | 2700 | 4 | 14 | 6 | 0 | 0 |
Current Process | 2700 | 0 | 0 | 0 | 12 | 9 |
2.2.2 Performance in Clay Sand
Studies have compared the XZ80 casting element with other similar materials. The results show that:
- The blue absorption and volatile content of 1 g of casting element are the same as those of 1.271 g of bentonite I and pulverized coal and 1.248 g of bentonite II and pulverized coal.
- The variation laws of wet pressure strength and air permeability of clay sand containing casting elements with casting elements and moisture are the same as those of bentonite and pulverized coal clay sand.
- The wet pressure strength and air permeability of clay sand containing casting elements without controlling the total mud content are higher than those of clay sand containing equivalent bentonite and pulverized coal.
- The wet pressure strength of clay sand containing casting elements with a total mud content of 13% of the sand mass is higher than that of clay sand containing equivalent bentonite and pulverized coal, and the air permeability is slightly higher or equal to that of clay sand containing equivalent bentonite and pulverized coal.
3. Application in Brake Disc and Brake Drum Production
3.1 Case Studies
3.1.1 Case One
A company’s casting workshop used 4 Japanese-imported horizontal unboxing injection molding lines for the production of automotive brake discs and brake drums. Initially, using pulverized coal and bentonite, the casting yield was 93%, with pore defects accounting for about 80% of the total rejects. Despite taking various measures such as increasing pouring temperature, enlarging the gas outlet area, reducing the gas evolution of the sand core, replacing the carburizer and inoculant, improving the quality of scrap steel, and increasing the sand grain size, the results were not satisfactory. After using casting elements, with the same process requirements for sand compaction rate, wet pressure strength, effective bentonite content, loss on ignition, and volatile content, the amount of casting elements added was less than the sum of bentonite and pulverized coal. The sand mud content decreased from 11.5% – 13% to 10% – 12%, and the water content decreased from 3.4% – 3.8% to 3.0% – 3.5%. The pore rejects of the casting decreased significantly. After further adjustments, the casting yield finally stabilized at 95% – 96%.
3.1.2 Case Two
A company’s casting workshop used two Japanese-imported vertical parting boxless injection molding lines for the production of automotive brake discs and brake drums. During production, there was a contradiction between increasing the wet pressure strength and increasing the collapsibility of the sand mold. When using pulverized coal and bentonite, adding more bentonite to increase the wet pressure strength and adding more pulverized coal to increase the collapsibility and sand release ability led to problems such as increased sand content and moisture in the sand, poor collapsibility and sand release ability, and serious sand sticking in the blank holes. After using casting elements, the amount of casting elements added was reduced to half of the original amount of bentonite and pulverized coal. The wet pressure strength, sand mud content, and compaction rate of the sand returned to normal. The collapsibility and sand release ability of the sand mold improved, and the problems of sand sticking in the blank holes were solved. The amount of new sand added was reduced to 1.5% – 3%, maintaining the balance of the sand treatment system.
3.1.3 Case Three
A company’s casting workshop used 3 Japanese-imported horizontal unboxing injection molding lines for the production of automotive brake discs and brake drums. Using a partition sand core to change from one mold for two pieces to one mold for four pieces increased the amount of collapsible core sand entering the sand, reducing the toughness of the sand and increasing the brittleness. This led to problems such as decreased demolding performance, increased waste molds, and increased defects such as sand washing, sand eyes, and sand inclusions in the casting. After using casting elements, the toughness and demolding performance of the sand gradually recovered. The casting rejects such as sand washing, sand eyes, and sand inclusions decreased, and the casting yield approached the level of the single-layer process.
3.1.4 Case Four
A company’s casting workshop used 3 Japanese-imported horizontal parting unboxing injection molding lines for the production of automotive brake discs and brake drums. When using artificial sodium-activated bentonite and high-quality pulverized coal, there were defects such as peeling, rat tail, vein pattern, and slight sand sticking near the small end root of larger brake disc castings. After using casting elements, the amount of casting elements added was reduced by 54% compared to the sum of bentonite and pulverized coal. The strength and toughness of the sand increased, and the defects such as peeling, rat tail, and vein pattern of the brake disc castings were completely solved. The amount of broken sand blocks and casting deformation rejects caused by boxing were also greatly reduced, and the initial inspection reject rate of the casting decreased by 60%.
3.2 Overall Benefits
From these case studies, it can be seen that when using casting elements, compared to using pulverized coal and bentonite:
- The amount of casting elements added is less.
- Harmful gas and solid emissions are reduced.
- The demolding property, collapsibility, and fluidity of the sand are improved.
- Defects such as pores, sand eyes, sand sticking, peeling, rat tail, vein pattern, and deformation of the casting are reduced.
4. Conclusion
Casting elements have proven to be a green, environmentally friendly, and efficient molding material in the production of automotive brake discs and brake drums. Their successful application in many domestic enterprises has brought numerous benefits, including reduced emissions, improved sand performance, and enhanced casting quality. This provides a new option for energy conservation, consumption reduction, and quality improvement in the casting industry.
5. Future Prospects and Research Directions
5.1 Potential for Wider Application
The success of casting elements in the production of automotive brake discs and brake drums indicates its potential for wider application in the casting industry. As environmental regulations become more stringent and the demand for high-quality castings increases, casting elements could be explored for use in other types of castings as well. For example, it could be tested in the production of engine blocks, transmission housings, or other critical automotive components. Its ability to reduce emissions and improve casting quality makes it an attractive option for manufacturers looking to meet both environmental and performance standards.
5.2 Further Research on Material Properties
While significant research has been conducted on casting elements, there is still room for further investigation. For instance, the long-term durability and stability of castings produced using casting elements need to be studied. This includes understanding how the material behaves over extended periods of use and under different operating conditions. Additionally, research could focus on optimizing the composition of casting elements to further enhance its properties. This could involve exploring different combinations of additives or modifying the existing components to achieve better performance in terms of strength, heat resistance, and anti-corrosion properties.
5.3 Integration with Advanced Manufacturing Technologies
The casting industry is evolving with the integration of advanced manufacturing technologies such as 3D printing and automation. Casting elements could be adapted to work in conjunction with these technologies. For example, in 3D printing of sand molds, the properties of casting elements could be exploited to create more precise and durable molds. In automated casting processes, the consistent performance of casting elements could contribute to more efficient and reliable production. Research and development efforts should be directed towards finding ways to integrate casting elements with these emerging technologies to stay ahead in a competitive manufacturing landscape.
6. Environmental and Economic Impact
6.1 Environmental Benefits and Sustainability
The use of casting elements has a significant positive impact on the environment. By reducing harmful gas and solid emissions, it helps to improve air quality in and around the casting facilities. This is not only beneficial for the health of the workers but also for the surrounding communities. Moreover, the reduction in the need for new sand and the reuse of dust removal ash contribute to resource conservation and waste reduction, making the casting process more sustainable. In a world where environmental concerns are at the forefront, the adoption of casting elements can be seen as a step towards a greener manufacturing industry.
6.2 Economic Advantages for Manufacturers
From an economic perspective, manufacturers can benefit from using casting elements in several ways. Firstly, the reduction in emissions can lead to compliance with environmental regulations, avoiding potential fines and penalties. Secondly, the improved casting quality results in fewer rejects and rework, saving costs associated with waste and additional production cycles. Thirdly, the lower consumption of auxiliary materials such as pulverized coal and bentonite reduces the material costs. Overall, the use of casting elements can enhance the economic competitiveness of manufacturers in the casting market.
7. Challenges and Solutions
7.1 Adoption Barriers
Despite the numerous benefits, there are some challenges associated with the widespread adoption of casting elements. One of the main barriers is the initial investment required for switching from traditional materials to casting elements. This includes the cost of purchasing new equipment or modifying existing equipment to handle the casting elements. Additionally, there may be a learning curve for workers who need to adapt to the new material and the associated production processes. Some manufacturers may be hesitant to make these changes due to concerns about potential disruptions to production and the uncertainty of the return on investment.
7.2 Solutions to Overcome Barriers
To overcome these adoption barriers, several solutions can be considered. Manufacturers can collaborate with equipment suppliers and research institutions to develop cost-effective solutions for equipment modification or replacement. Training programs can be implemented for workers to familiarize them with the properties and handling of casting elements. Demonstration projects can be carried out to showcase the benefits of casting elements in actual production settings, providing evidence of the potential return on investment. By addressing these challenges, the adoption of casting elements can be accelerated, leading to a more widespread use of this innovative material in the casting industry.
8. Comparison with Other Casting Materials
8.1 Casting Elements vs. Resin-Bonded Sand
Resin-bonded sand is another commonly used material in the casting industry. While it offers certain advantages such as high strength and good dimensional accuracy, it also has some drawbacks. For example, the resin used in resin-bonded sand can release harmful fumes during the casting process, which is a concern from an environmental perspective. In contrast, casting elements have been shown to significantly reduce harmful gas emissions. Additionally, the cost of resin-bonded sand can be relatively high compared to casting elements, especially when considering the large-scale production of brake discs and brake drums.
8.2 Casting Elements vs. Ceramic Mold Casting
Ceramic mold casting is known for its ability to produce high-quality, complex-shaped castings. However, it is a more complex and costly process compared to traditional sand casting methods. Casting elements, on the other hand, can be easily integrated into existing sand casting processes, offering a more straightforward and cost-effective solution for the production of brake discs and brake drums. Moreover, the environmental impact of ceramic mold casting may be higher due to the use of certain chemicals and materials in the mold-making process, while casting elements have been proven to be more environmentally friendly.
9. Conclusion
In conclusion, casting elements have emerged as a promising alternative to traditional casting materials in the production of automotive brake discs and brake drums. Their unique combination of properties, including environmental friendliness, improved casting quality, and cost-effectiveness, make them an attractive choice for manufacturers. While there are challenges associated with their adoption, solutions are available to overcome these barriers. The future of casting elements looks bright, with potential for wider application, further research and development, and integration with advanced manufacturing technologies. As the casting industry continues to evolve, casting elements are likely to play an increasingly important role in meeting the demands for high-quality, sustainable castings.
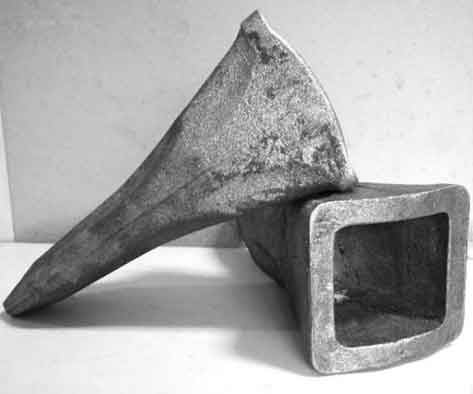