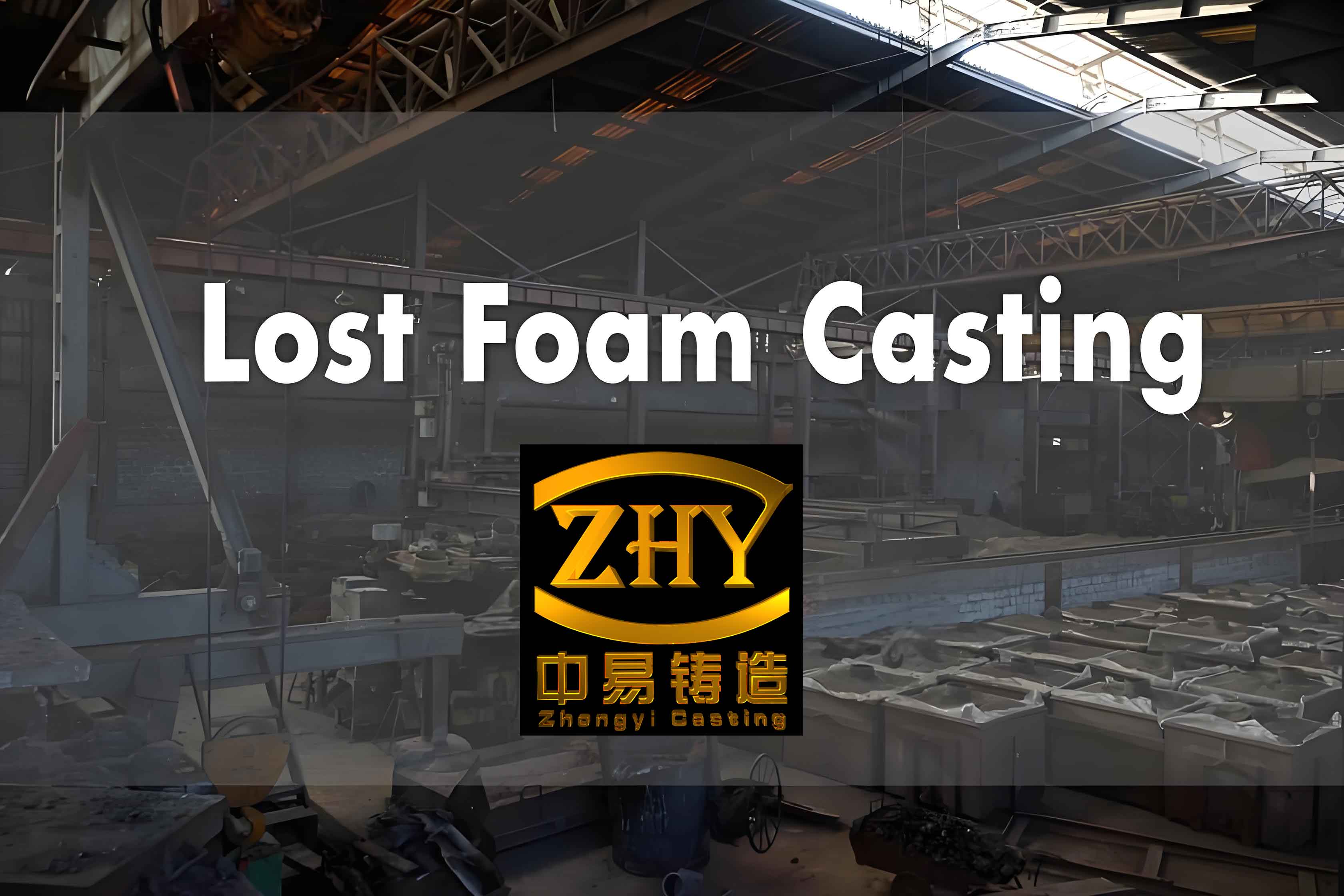
1. Introduction
Lost foam casting, a revolutionary casting method, has been widely used in the manufacturing industry. It offers unique advantages over traditional casting techniques, making it a popular choice for producing complex metal components. This article aims to provide a detailed exploration of lost foam casting, covering its principles, processes, applications, and quality control aspects.
1.1 Principles of Lost Foam Casting
Lost foam casting operates on the principle of using a polystyrene foam pattern that replicates the final shape of the desired casting. The foam pattern is coated with a refractory material to form a mold. When molten metal is poured into the mold, the foam pattern vaporizes, leaving behind a cavity that is filled with the metal. This process allows for the production of intricate shapes with high precision.
1.2 Historical Development
The concept of lost foam casting has evolved over time. It originated from the need to find a more efficient and accurate way to produce metal parts. Early experiments led to the development of the basic principles and techniques that are now widely used. Over the years, advancements in materials, equipment, and process control have significantly improved the quality and efficiency of lost foam casting.
1.3 Advantages and Disadvantages
- Advantages
- Complex geometries can be easily produced as the foam pattern can be molded into any shape.
- Reduced need for machining as the casting can be produced closer to the final shape.
- Good surface finish can be achieved due to the smooth surface of the foam pattern.
- The process is relatively clean as there are no parting lines or cores to remove.
- DisadvantagesDisadvantageDescriptionFoam Pattern DegradationThe foam pattern may degrade during handling or storage, affecting the final casting quality.Gas EvolutionThe vaporization of the foam pattern can lead to gas evolution problems, causing porosity in the casting.Cost of Foam and Coating MaterialsThe materials used for the foam pattern and coating can be expensive, increasing the overall cost of production.
2. Materials Used in Lost Foam Casting
2.1 Foam Patterns
The foam patterns used in lost foam casting are typically made of expandable polystyrene (EPS). EPS has several desirable properties such as low density, good moldability, and ease of machining. The density of the EPS can be adjusted depending on the requirements of the casting. For example, a higher density may be required for larger or more complex parts to ensure better dimensional stability.
Foam Pattern Properties | Details |
---|---|
Material | Expandable Polystyrene (EPS) |
Density Range | Varies depending on application (e.g., 15 – 30 g/L) |
Moldability | Good, can be molded into complex shapes |
Machinability | Easy to machine for final adjustments |
2.2 Coating Materials
The coating materials used in lost foam casting play a crucial role in protecting the foam pattern during the casting process and in forming a proper mold cavity. Commonly used coating materials include refractory slurries and ceramic coatings. These coatings must have good adhesion to the foam pattern, high refractoriness, and adequate permeability to allow for the escape of gases generated during the casting process.
Coating Material Properties | Details |
---|---|
Types | Refractory slurries, ceramic coatings |
Adhesion | Good adhesion to foam pattern |
Refractoriness | High, to withstand molten metal temperatures |
Permeability | Adequate to allow gas escape |
3. The Lost Foam Casting Process
3.1 Pattern Making
The first step in the lost foam casting process is pattern making. This involves creating the foam pattern using techniques such as injection molding or CNC machining. The pattern must be accurately designed to match the final shape of the casting. Any inaccuracies in the pattern will be transferred to the final casting.
Pattern Making Steps | Details |
---|---|
Methods | Injection molding, CNC machining |
Design Considerations | Accuracy to match final casting shape |
3.2 Coating Application
After the pattern is made, it is coated with the chosen coating material. This can be done by dipping, spraying, or brushing. The coating thickness must be carefully controlled to ensure proper mold formation and gas escape. Multiple coats may be required depending on the complexity of the casting.
Coating Application Steps | Details |
---|---|
Methods | Dipping, spraying, brushing |
Thickness Control | Carefully controlled for proper mold formation and gas escape |
Number of Coats | Varies depending on casting complexity |
3.3 Mold Assembly
Once the pattern is coated, it is assembled into a mold. This may involve placing the coated pattern in a flask and adding sand or other refractory materials around it. The mold must be properly compacted to ensure that it can withstand the pressure of the molten metal during pouring.
Mold Assembly Steps | Details |
---|---|
Placement | Coated pattern placed in flask |
Compaction | Proper compaction with sand or other refractory materials |
3.4 Pouring
The molten metal is then poured into the mold. The pouring temperature and rate must be carefully controlled to ensure proper filling of the mold cavity and to avoid defects such as porosity and incomplete filling. The type of metal used depends on the requirements of the final casting.
Pouring Steps | Details |
---|---|
Temperature Control | Carefully controlled to ensure proper filling and avoid defects |
Rate Control | Carefully controlled to ensure proper filling and avoid defects |
Metal Type | Depends on final casting requirements |
3.5 Solidification and Cooling
After pouring, the metal solidifies and cools in the mold. The cooling rate can affect the microstructure and mechanical properties of the casting. Therefore, it is important to control the cooling rate appropriately. This may involve using cooling jackets or other cooling devices.
Solidification and Cooling Steps | Details |
---|---|
Cooling Rate Control | Affects microstructure and mechanical properties, controlled appropriately |
Cooling Devices | Cooling jackets, etc. may be used |
3.6 Casting Removal and Finishing
Once the casting has cooled, it is removed from the mold. This may involve breaking the mold or using other extraction methods. The casting is then finished by removing any remaining sand or coating material and by performing any necessary machining operations.
Casting Removal and Finishing Steps | Details |
---|---|
Removal Method | Breaking mold or other extraction methods |
Finishing Operations | Removing sand and coating material, machining |
4. Applications of Lost Foam Casting
4.1 Automotive Industry
Lost foam casting is widely used in the automotive industry for producing engine components such as cylinder heads, engine blocks, and transmission cases. The ability to produce complex geometries and reduce machining requirements makes it an ideal choice for these applications.
Automotive Applications | Details |
---|---|
Components Produced | Cylinder heads, engine blocks, transmission cases |
Advantages for Automotive | Complex geometries, reduced machining |
4.2 Aerospace Industry
In the aerospace industry, lost foam casting is used for producing parts such as turbine blades and structural components. The high precision and good mechanical properties of the castings make them suitable for these critical applications.
Aerospace Applications | Details |
---|---|
Components Produced | Turbine blades, structural components |
Advantages for Aerospace | High precision, good mechanical properties |
4.3 Other Industries
Lost foam casting is also used in other industries such as the manufacturing of machinery, tools, and household appliances. It can be used to produce a wide variety of parts with different shapes and sizes.
Other Industries Applications | Details |
---|---|
Examples of Industries | Machinery, tools, household appliances |
General Advantages | Wide variety of parts production |
5. Quality Control in Lost Foam Casting
5.1 Inspection of Foam Patterns
Before coating, the foam patterns must be inspected for any defects such as cracks, holes, or dimensional inaccuracies. This can be done using visual inspection or more advanced techniques such as X-ray or CT scanning.
Foam Pattern Inspection Steps | Details |
---|---|
Methods | Visual inspection, X-ray, CT scanning |
Defects to Look For | Cracks, holes, dimensional inaccuracies |
5.2 Coating Quality Control
The coating quality must be controlled to ensure proper adhesion and thickness. This can be done by measuring the coating thickness using instruments such as a micrometer or by performing adhesion tests.
Coating Quality Control Steps | Details |
---|---|
Thickness Measurement | Using micrometer or other instruments |
Adhesion Tests | Performing adhesion tests |
5.3 Mold Inspection
The mold must be inspected for any defects such as cracks, voids, or improper compaction. This can be done using visual inspection or more advanced techniques such as ultrasonic testing.
Mold Inspection Steps | Details |
---|---|
Methods | Visual inspection, ultrasonic testing |
Defects to Look For | Cracks, voids, improper compaction |
5.4 Casting Inspection
After casting, the casting must be inspected for any defects such as porosity, cracks, or dimensional inaccuracies. This can be done using visual inspection, X-ray, or CT scanning. The mechanical properties of the casting must also be tested to ensure that it meets the required standards.
Casting Inspection Steps | Details |
---|---|
Methods | Visual inspection, X-ray, CT scanning |
Defects to Look For | Porosity, cracks, dimensional inaccuracies |
Mechanical Property Tests | To ensure standards are met |
6. Future Trends in Lost Foam Casting
6.1 Advancements in Materials
There is a continuous search for better foam and coating materials. New materials with improved properties such as higher refractoriness, better gas permeability, and lower cost are being developed. These materials will improve the quality and efficiency of lost foam casting.
6.2 Process Automation
Automation is becoming increasingly important in lost foam casting. Automated pattern making, coating application, and pouring processes will reduce human error and increase production efficiency. This will also lead to more consistent casting quality.
6.3 Simulation and Modeling
Simulation and modeling techniques are being used to predict the behavior of the casting process. This includes predicting the flow of molten metal, the evolution of gases, and the formation of defects. By using these techniques, the casting process can be optimized before actual production.
7. Conclusion
Lost foam casting is a versatile and important casting technique that has a wide range of applications. It offers many advantages over traditional casting methods, but also has some limitations. Through continuous research and development, the quality and efficiency of lost foam casting are constantly improving. The future trends in lost foam casting, such as advancements in materials, process automation, and simulation and modeling, will further enhance its capabilities and make it an even more valuable tool in the manufacturing industry.