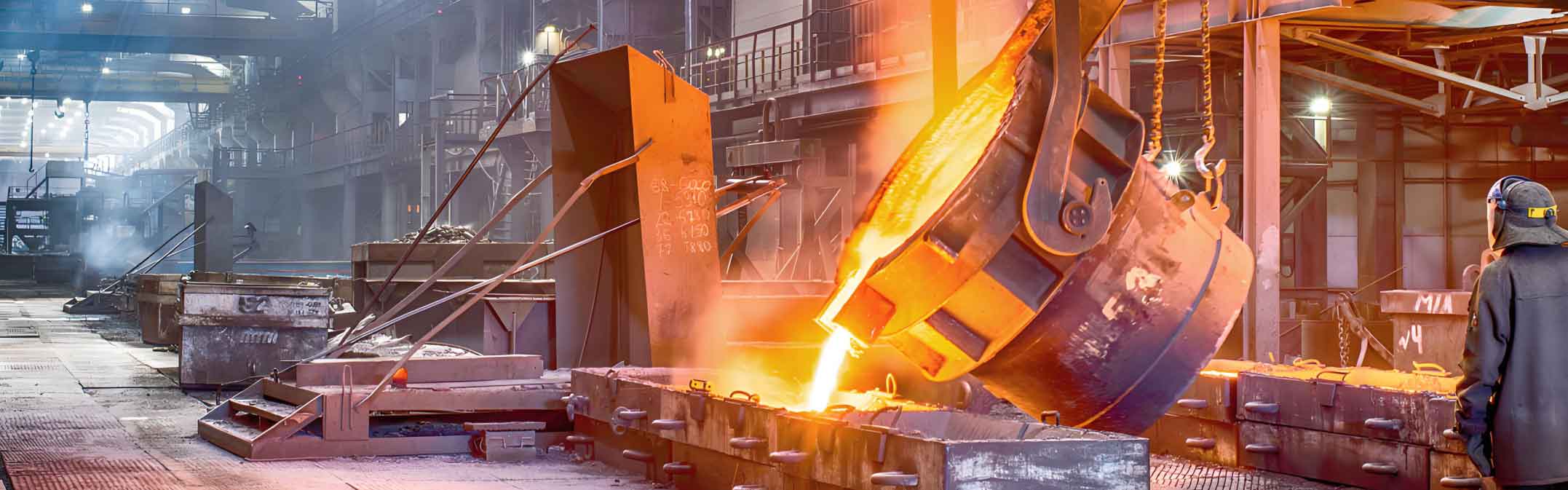
Porosity is a common defect in sand casting that can significantly affect the mechanical properties and overall quality of cast components. It manifests as small voids or cavities within the casting, which can lead to reduced strength, compromised structural integrity, and potential failure under stress. Addressing porosity is critical for producing high-quality sand castings, particularly in industries where reliability and performance are paramount. This article explores the causes of porosity in sand casting and presents advanced methods and technologies to reduce or eliminate this defect.
Introduction to Sand Casting
Sand casting is a versatile and widely used manufacturing process that involves creating a mold from a sand mixture and pouring molten metal into the cavity formed by a pattern. The sand mold is then broken away to reveal the metal casting. Despite its versatility, sand casting is prone to defects such as porosity, which can undermine the quality of the final product.
Importance of Reducing Porosity
- Mechanical Properties: Porosity reduces the strength and ductility of cast components.
- Structural Integrity: Voids and cavities can compromise the structural integrity of the casting.
- Surface Finish: Porosity can lead to rough surfaces, requiring additional finishing work.
- Leakage: In components like engine blocks or hydraulic parts, porosity can cause leaks.
Causes of Porosity in Sand Casting
Understanding the causes of porosity is the first step in mitigating this defect. Porosity in sand casting can result from several factors, including gas entrapment, shrinkage, and improper mold materials or techniques.
Gas Porosity
Gas porosity occurs when gases are trapped within the molten metal during the casting process. Sources of gas can include moisture in the mold, reactions between the metal and mold materials, and impurities in the metal.
- Moisture: Water vapor from damp sand or binders can cause gas bubbles.
- Reactions: Chemical reactions between the metal and mold materials can produce gases.
- Impurities: Impurities in the molten metal can release gases upon heating.
Shrinkage Porosity
Shrinkage porosity occurs due to the natural contraction of metal as it cools and solidifies. If the mold does not provide sufficient feed metal to compensate for this shrinkage, voids can form.
- Inadequate Feeding: Insufficient risers or feeders can lead to shrinkage porosity.
- Directional Solidification: Improper cooling rates can cause uneven solidification and void formation.
Mold Material and Design
The choice of mold material and design can significantly impact porosity levels. Poorly designed molds or suboptimal sand mixtures can contribute to porosity.
- Sand Quality: Low-quality sand or improper sand mixtures can lead to gas formation.
- Mold Design: Inadequate venting or improper gating systems can trap gases.
Cause of Porosity | Description |
---|---|
Gas Porosity | Gas bubbles trapped in the molten metal |
Shrinkage Porosity | Voids formed due to metal contraction during cooling |
Mold Material and Design | Poor sand quality, inadequate venting, or improper gating systems |
Methods to Reduce Porosity in Sand Casting
To produce high-quality sand castings with minimal porosity, various methods and technologies can be employed. These include improving mold materials and design, optimizing the casting process, and employing advanced techniques to control gas and shrinkage.
Improving Mold Materials and Design
High-Quality Sand
Using high-quality sand with uniform grain size and appropriate additives can reduce gas formation and improve mold strength.
- Uniform Grain Size: Ensures consistent permeability and reduces gas entrapment.
- Additives: Binders and additives can enhance sand properties and reduce gas generation.
Enhanced Mold Coatings
Applying mold coatings can create a barrier that reduces gas permeability and improves the surface finish of the casting.
- Gas Barrier: Coatings can prevent gases from escaping the mold into the molten metal.
- Surface Finish: Improves the surface finish and reduces defects related to mold-material interaction.
Optimized Gating and Venting Systems
Designing efficient gating and venting systems ensures proper metal flow and gas escape, reducing the likelihood of porosity.
- Gating Systems: Ensure smooth and controlled metal flow to avoid turbulence and gas entrapment.
- Venting Systems: Adequate venting allows gases to escape, preventing them from being trapped in the molten metal.
Method | Description |
---|---|
High-Quality Sand | Uniform grain size, appropriate additives |
Enhanced Mold Coatings | Reduces gas permeability, improves surface finish |
Optimized Gating and Venting Systems | Ensures proper metal flow and gas escape |
Optimizing the Casting Process
Controlled Pouring Temperature
Maintaining an optimal pouring temperature reduces gas solubility in the molten metal and minimizes the formation of gas porosity.
- Optimal Temperature: Ensures molten metal has the right fluidity and reduces gas solubility.
- Consistent Temperature: Prevents fluctuations that can lead to uneven solidification.
Use of Chills
Chills are metal inserts placed within the mold to accelerate cooling and promote directional solidification, reducing shrinkage porosity.
- Directional Solidification: Encourages controlled cooling and solidification, reducing void formation.
- Cooling Control: Helps achieve uniform cooling rates, preventing shrinkage porosity.
Method | Description |
---|---|
Controlled Pouring Temperature | Maintains optimal temperature to reduce gas solubility |
Use of Chills | Accelerates cooling, promotes directional solidification |
Advanced Techniques and Technologies
Vacuum-Assisted Casting
Vacuum-assisted casting involves applying a vacuum to the mold cavity to remove gases and reduce porosity.
- Gas Removal: Vacuum removes trapped gases, reducing gas porosity.
- Improved Quality: Results in higher quality castings with fewer defects.
Inert Gas Purging
Purging the molten metal with inert gases such as argon or nitrogen can remove dissolved gases and reduce gas porosity.
- Gas Purging: Inert gases displace dissolved gases, reducing gas porosity.
- Cleaner Metal: Results in cleaner metal with fewer impurities.
Simulation and Modeling
Using simulation and modeling tools to predict and optimize the casting process can help identify and mitigate potential sources of porosity.
- Predictive Modeling: Identifies areas prone to porosity and suggests design modifications.
- Process Optimization: Allows for the optimization of parameters to minimize defects.
Advanced Technique | Description |
---|---|
Vacuum-Assisted Casting | Removes gases using vacuum, reduces porosity |
Inert Gas Purging | Purges molten metal with inert gases to remove dissolved gases |
Simulation and Modeling | Predicts and optimizes casting process to mitigate porosity |
Applications in Grey Cast Iron Casting
Reducing porosity is particularly important in the casting of grey cast iron components, where mechanical properties and surface quality are critical.
Automotive Industry
- Engine Blocks: Reducing porosity improves the strength and durability of engine blocks.
- Brake Discs: Ensures reliable performance and safety in brake discs by minimizing defects.
Heavy Machinery
- Gear Housings: Enhanced structural integrity and performance by reducing porosity.
- Pump Housings: Improved reliability and efficiency in pump housings through minimized defects.
Aerospace Industry
- Turbine Components: High-performance turbine components with superior mechanical properties and minimal porosity.
- Structural Parts: Ensures high reliability and safety in critical aerospace structural parts.
Industry | Applications |
---|---|
Automotive | Engine blocks, brake discs |
Heavy Machinery | Gear housings, pump housings |
Aerospace | Turbine components, structural parts |
Conclusion
Reducing porosity in sand casting is crucial for producing high-quality grey cast iron components with enhanced mechanical properties, structural integrity, and surface finish. By understanding the causes of porosity and employing advanced methods and technologies, manufacturers can significantly reduce or eliminate this defect. Improving mold materials and design, optimizing the casting process, and utilizing advanced techniques such as vacuum-assisted casting, inert gas purging, and simulation and modeling are effective strategies for minimizing porosity. These advancements ensure the production of reliable and high-performance castings, meeting the stringent requirements of modern engineering and manufacturing across various industries.
Strategy | Description |
---|---|
Improving Mold Materials and Design | High-quality sand, enhanced coatings, optimized gating and venting |
Optimizing the Casting Process | Controlled pouring temperature, use of chills |
Advanced Techniques and Technologies | Vacuum-assisted casting, inert gas purging, simulation and modeling |
By adopting these strategies, manufacturers can achieve superior sand castings with minimal porosity, ensuring the reliability and performance of their products in demanding applications.