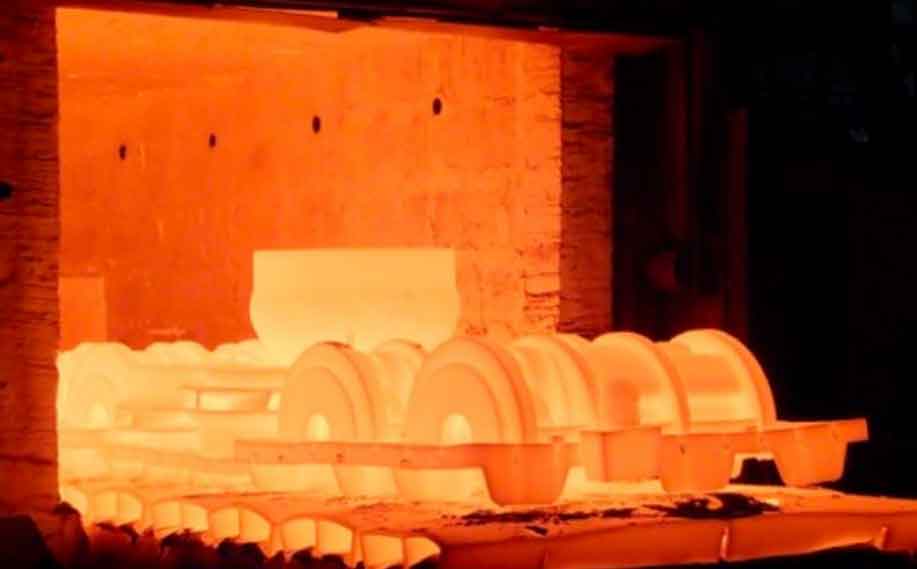
Investment casting is highly precise and versatile manufacturing process used to produce complex metal components with fine details. To enhance the mechanical properties and surface finish of these components, heat treatment and surface finishing techniques are employed. This article delves into the importance of heat treatment and surface finishing in investment casting, highlighting key processes, techniques, and their benefits.
Introduction to Investment Casting
Investment casting involves creating a wax model of the desired part, which is then coated with a ceramic shell. The wax is melted out, leaving a cavity that is filled with molten metal. Once the metal solidifies, the ceramic shell is removed to reveal the metal casting. This process is particularly advantageous for producing components with intricate geometries and high dimensional accuracy.
Key Steps in Investment Casting
- Pattern Creation: A wax model of the desired part is created using injection molding or hand carving.
- Assembly: Multiple wax models can be assembled onto a wax tree to create multiple parts in a single batch.
- Shell Building: The wax assembly is repeatedly dipped into a ceramic slurry and coated with fine sand to build a ceramic shell.
- Dewaxing: The ceramic shell is heated to remove the wax, leaving a hollow cavity.
- Metal Pouring: Molten metal is poured into the ceramic mold.
- Shell Removal: Once the metal has solidified, the ceramic shell is broken away to reveal investment casting.
- Finishing: The investment casting is cleaned, and any excess material is removed to achieve the final product.
Importance of Heat Treatment in Investment Casting
Heat treatment is a crucial post-casting process used to alter the microstructure of the cast metal, thereby enhancing its mechanical properties and performance. The primary objectives of heat treatment in investment casting are to improve hardness, strength, ductility, and toughness while reducing internal stresses and casting defects.
Key Heat Treatment Processes
- Annealing: A process that involves heating investment casting to a specific temperature and then slowly cooling it. Annealing is used to soften the metal, improve ductility, and relieve internal stresses.
- Normalizing: Involves heating investment casting to a higher temperature than annealing and then air cooling. Normalizing refines the grain structure, enhances toughness, and reduces residual stresses.
- Quenching: A process where investment casting is heated to a high temperature and then rapidly cooled in water, oil, or air. Quenching increases hardness and strength but can also make the metal more brittle.
- Tempering: Performed after quenching, tempering involves reheating investment casting to a lower temperature and then cooling it. This process reduces brittleness while maintaining the increased strength and hardness.
- Aging: Typically used for aluminum and other non-ferrous alloys, aging involves heating investment casting to a moderate temperature and holding it for an extended period to enhance strength and hardness.
Benefits of Heat Treatment
- Enhanced Mechanical Properties: Improved hardness, strength, ductility, and toughness.
- Reduced Residual Stresses: Minimizes internal stresses that can lead to distortion or failure.
- Improved Wear Resistance: Increases the surface hardness and wear resistance of investment casting.
- Refined Grain Structure: Produces a more uniform and refined grain structure for better mechanical performance.
Importance of Surface Finishing in Investment Casting
Surface finishing is essential in investment casting to improve the surface quality, appearance, and performance of the cast components. The primary objectives of surface finishing are to remove surface imperfections, enhance corrosion resistance, and achieve the desired surface texture.
Key Surface Finishing Techniques
- Mechanical Finishing: Involves processes such as grinding, polishing, and buffing to smooth and refine investment casting surface.
- Chemical Finishing: Uses chemical treatments like pickling and passivation to clean and improve the corrosion resistance of investment casting.
- Electroplating: Involves coating investment casting with a thin layer of metal (e.g., chrome, nickel) to enhance surface properties.
- Shot Blasting: A process where investment casting is blasted with high-speed abrasive particles to clean and smooth the surface.
- Vibratory Finishing: Involves placing investment casting in a vibrating container with abrasive media to polish and smooth the surface.
Benefits of Surface Finishing
- Improved Surface Quality: Removes surface imperfections and achieves a smoother finish.
- Enhanced Corrosion Resistance: Chemical treatments and coatings improve resistance to corrosion and oxidation.
- Aesthetic Enhancement: Improves the appearance of investment casting, making it more visually appealing.
- Increased Durability: Enhances the wear resistance and longevity of investment casting.
Tables and Lists for Key Processes and Techniques
Table 1: Key Heat Treatment Processes in Investment Casting
Heat Treatment Process | Description | Benefits |
---|---|---|
Annealing | Heating and slow cooling to soften metal and relieve stress | Improved ductility, reduced internal stresses |
Normalizing | Heating to a high temperature and air cooling | Refined grain structure, enhanced toughness |
Quenching | Heating and rapid cooling in water, oil, or air | Increased hardness and strength, potential brittleness |
Tempering | Reheating after quenching to a lower temperature | Reduced brittleness, maintained strength and hardness |
Aging | Heating and holding at moderate temperature for non-ferrous alloys | Enhanced strength and hardness |
Table 2: Key Surface Finishing Techniques in Investment Casting
Surface Finishing Technique | Description | Benefits |
---|---|---|
Mechanical Finishing | Grinding, polishing, and buffing to smooth and refine surface | Improved surface quality, aesthetic enhancement |
Chemical Finishing | Chemical treatments like pickling and passivation | Enhanced corrosion resistance, cleaned surface |
Electroplating | Coating with a thin layer of metal | Improved surface properties, increased durability |
Shot Blasting | Blasting with abrasive particles | Cleaned and smoothed surface |
Vibratory Finishing | Vibrating container with abrasive media | Polished and smoothed surface, increased durability |
List: Benefits of Heat Treatment in Investment Casting
- Enhanced mechanical properties such as hardness, strength, ductility, and toughness
- Reduced residual stresses that can lead to distortion or failure
- Improved wear resistance through increased surface hardness
- Refined grain structure for better mechanical performance
List: Benefits of Surface Finishing in Investment Casting
- Improved surface quality by removing imperfections and achieving a smoother finish
- Enhanced corrosion resistance through chemical treatments and coatings
- Aesthetic enhancement for a visually appealing casting
- Increased durability and wear resistance
Case Studies: Successful Application of Heat Treatment and Surface Finishing
Case Study 1: Aerospace Components
A leading aerospace manufacturer used a combination of quenching and tempering processes to enhance the mechanical properties of their investment cast turbine blades. The heat treatment process resulted in significantly improved hardness and strength, enabling the blades to withstand extreme operating conditions.
Case Study 2: Medical Implants
A medical device company implemented vibratory finishing and electroplating to enhance the surface quality and biocompatibility of their investment cast orthopedic implants. The finishing techniques improved the implants’ surface smoothness and corrosion resistance, resulting in higher patient satisfaction and longer implant life.
Case Study 3: High-Performance Automotive Parts
An automotive manufacturer employed shot blasting and chemical passivation to improve the surface finish and corrosion resistance of their investment cast engine components. The surface finishing techniques ensured a clean and smooth surface, reducing the risk of corrosion and enhancing the components’ overall performance.
Conclusion
Heat treatment and surface finishing are essential processes in investment casting that significantly impact the mechanical properties, surface quality, and performance of the cast components. By carefully selecting and implementing the appropriate heat treatment and surface finishing techniques, casting manufacturers can produce high-quality components that meet the stringent requirements of various industries. Continuous advancements in these processes ensure that investment casting remains a vital and versatile manufacturing method for creating complex and high-precision metal parts.