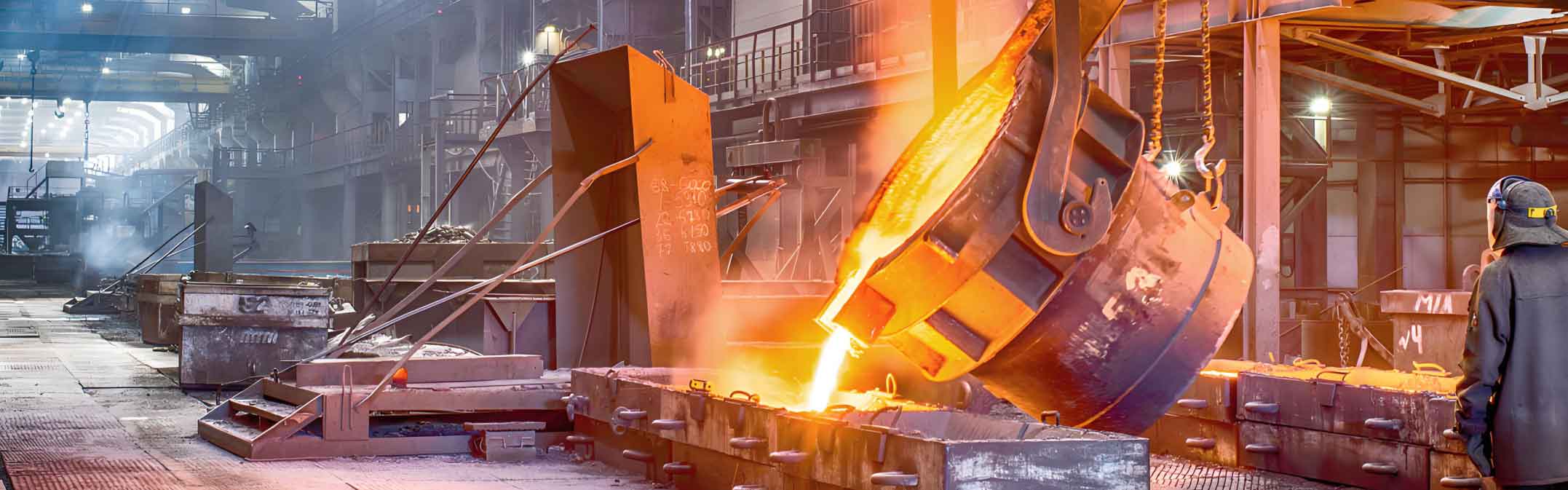
Sand casting is versatile and widely used method for producing metal components, especially for complex geometries and large castings. The cooling and solidification phases are critical in sand casting, as they significantly affect the microstructure, mechanical properties, and overall quality of the final casting. Innovations in cooling and solidification methods have enhanced the ability to control these processes, leading to improved casting quality and efficiency. This article explores various innovative cooling and solidification methods in sand casting, detailing their benefits, applications, and impact on casting quality.
Introduction to Sand Casting
Sand casting involves creating a mold from a sand mixture and pouring molten metal into the cavity formed by a pattern. The molten metal cools and solidifies within the mold, forming the final casting. The quality of the casting is highly dependent on the cooling and solidification processes, which determine the microstructure and mechanical properties of the metal.
Importance of Cooling and Solidification
- Microstructure Control: The rate and pattern of cooling influence the grain structure and phase distribution within the metal, affecting its mechanical properties.
- Defect Minimization: Proper cooling and solidification methods can reduce defects such as shrinkage porosity, hot tears, and internal stresses.
- Dimensional Accuracy: Controlled cooling helps maintain dimensional accuracy and minimizes distortion.
- Surface Finish: Effective cooling techniques can improve the surface finish of the casting.
Traditional Cooling and Solidification Methods
Traditional cooling and solidification methods in sand casting often rely on the natural cooling of the molten metal within the sand mold. While effective for many applications, these methods can have limitations in terms of control and efficiency.
Natural Cooling
Natural cooling involves allowing the molten metal to cool and solidify at its own rate within the sand mold.
- Advantages: Simple, cost-effective, requires minimal equipment.
- Disadvantages: Limited control over cooling rate, potential for defects, longer cooling times.
Chills
Chills are metal inserts placed within the mold to accelerate the cooling rate of specific areas.
- Advantages: Improves control over cooling rate, reduces shrinkage defects.
- Disadvantages: Can cause thermal stresses, may complicate mold design.
Risers
Risers are reservoirs of molten metal that feed the casting as it solidifies to compensate for shrinkage.
- Advantages: Helps prevent shrinkage porosity and voids.
- Disadvantages: Requires additional material, increases weight and cost of the casting.
Method | Advantages | Disadvantages |
---|---|---|
Natural Cooling | Simple, cost-effective, minimal equipment | Limited control, potential for defects, longer cooling times |
Chills | Improved cooling control, reduces shrinkage defects | Can cause thermal stresses, complicates mold design |
Risers | Prevents shrinkage porosity and voids | Requires additional material, increases cost |
Innovative Cooling and Solidification Methods
Recent advancements in cooling and solidification methods have provided greater control and efficiency in sand casting processes. These innovations include advanced cooling techniques, real-time monitoring systems, and novel solidification strategies.
Advanced Cooling Techniques
Directed Cooling
Directed cooling involves the use of targeted cooling channels and systems to control the cooling rate and pattern within the mold.
- Materials: Cooling tubes, heat sinks, and other cooling devices.
- Advantages: Precise control over cooling rate, reduces thermal stresses, improves microstructure.
- Applications: Suitable for complex geometries and large castings.
Active Cooling
Active cooling uses external cooling systems such as water jackets or forced air to accelerate the cooling process.
- Materials: Water jackets, air blowers.
- Advantages: Faster cooling, improved control over solidification, reduced cycle times.
- Applications: Ideal for high-production environments and components requiring rapid cooling.
Advanced Cooling Technique | Materials | Advantages | Applications |
---|---|---|---|
Directed Cooling | Cooling tubes, heat sinks | Precise control, reduces thermal stresses, improves microstructure | Complex geometries, large castings |
Active Cooling | Water jackets, air blowers | Faster cooling, improved control, reduced cycle times | High-production environments, rapid cooling needs |
Real-Time Monitoring Systems
Real-time monitoring systems use sensors and data acquisition tools to track the cooling and solidification process, allowing for immediate adjustments and optimization.
Thermal Imaging
Thermal imaging cameras monitor the temperature distribution within the mold in real-time.
- Advantages: Provides detailed thermal profiles, identifies hot spots and potential defects, enables real-time adjustments.
- Applications: Useful for critical castings where precise temperature control is required.
Thermocouples and Data Loggers
Thermocouples and data loggers measure and record temperature data throughout the cooling and solidification process.
- Advantages: Accurate temperature monitoring, facilitates process optimization, helps predict and prevent defects.
- Applications: Applicable to various casting processes, including grey cast iron.
Real-Time Monitoring System | Advantages | Applications |
---|---|---|
Thermal Imaging | Detailed thermal profiles, real-time adjustments | Critical castings requiring precise temperature control |
Thermocouples and Data Loggers | Accurate temperature monitoring, process optimization | Various casting processes, including grey cast iron |
Novel Solidification Strategies
Gradient Solidification
Gradient solidification involves controlling the temperature gradient within the mold to influence the direction and rate of solidification.
- Materials: Gradient control systems, thermal management devices.
- Advantages: Enhances grain structure, reduces defects, improves mechanical properties.
- Applications: Ideal for high-performance components requiring superior mechanical properties.
Electromagnetic Solidification
Electromagnetic solidification uses electromagnetic fields to influence the solidification process and improve metal properties.
- Materials: Electromagnetic coils, power supplies.
- Advantages: Refines microstructure, reduces segregation, enhances mechanical properties.
- Applications: Suitable for high-quality castings, including those in the aerospace and automotive industries.
Novel Solidification Strategy | Materials | Advantages | Applications |
---|---|---|---|
Gradient Solidification | Gradient control systems | Enhances grain structure, reduces defects, improves mechanical properties | High-performance components |
Electromagnetic Solidification | Electromagnetic coils | Refines microstructure, reduces segregation, enhances mechanical properties | High-quality castings, aerospace, automotive |
Benefits of Innovative Cooling and Solidification Methods
The implementation of innovative cooling and solidification methods in sand casting offers numerous benefits, enhancing the overall quality, efficiency, and performance of castings.
Improved Microstructure and Mechanical Properties
Advanced cooling and solidification techniques provide better control over the microstructure of the metal, leading to improved mechanical properties such as strength, hardness, and toughness.
Reduced Defects
Innovative methods help minimize common casting defects such as shrinkage porosity, hot tears, and internal stresses, resulting in higher quality castings.
Enhanced Dimensional Accuracy
Precise control over the cooling and solidification processes ensures that castings maintain their dimensional accuracy and minimize distortion.
Increased Efficiency
Faster and more controlled cooling methods reduce cycle times and improve production efficiency, making the casting process more cost-effective.
Benefit | Description |
---|---|
Improved Microstructure | Better control over metal microstructure, enhancing mechanical properties |
Reduced Defects | Minimizes casting defects like shrinkage porosity and hot tears |
Enhanced Dimensional Accuracy | Ensures castings maintain dimensional accuracy and minimizes distortion |
Increased Efficiency | Faster cooling reduces cycle times and improves production efficiency |
Applications in Grey Cast Iron Casting
The advancements in cooling and solidification methods have significant implications for the casting of grey cast iron, particularly in industries requiring high precision and superior mechanical properties.
Automotive Industry
- Engine Blocks: Advanced cooling techniques ensure uniform solidification, improving the strength and durability of engine blocks.
- Brake Discs: Real-time monitoring and active cooling reduce defects and enhance the performance of brake discs.
Heavy Machinery
- Gear Housings: Novel solidification strategies improve the grain structure and mechanical properties of gear housings.
- Pump Housings: Enhanced cooling methods ensure dimensional accuracy and reduce the risk of defects in pump housings.
Aerospace Industry
- Turbine Blades: Precise control over cooling and solidification is critical for producing high-quality turbine blades with superior mechanical properties.
- Structural Components: Innovative methods help achieve the stringent quality standards required for aerospace structural components.
Industry | Applications |
---|---|
Automotive | Engine blocks, brake discs |
Heavy Machinery | Gear housings, pump housings |
Aerospace | Turbine blades, structural components |
Conclusion
Innovative cooling and solidification methods in sand casting have revolutionized the production of high-quality metal components, particularly for grey cast iron. Advanced cooling techniques, real-time monitoring systems, and novel solidification strategies provide better control over the casting process, leading to improved microstructure, reduced defects, enhanced dimensional accuracy, and increased efficiency. These advancements have significant implications for various industries, including automotive, heavy machinery, and aerospace, where high precision and superior mechanical properties are essential. By adopting these innovative methods, manufacturers can achieve superior castings that meet the rigorous requirements of modern engineering and manufacturing, ensuring reliable and high-performance components.
Innovative Method | Advantages | Applications |
---|---|---|
Advanced Cooling Techniques | Precise control, faster cooling, improved microstructure | Complex geometries, high-production environments |
Real-Time Monitoring Systems | Accurate temperature control, defect prevention | Critical castings, grey cast iron |
Novel Solidification Strategies | Enhanced grain structure, reduced defects | High-performance components, aerospace, automotive |