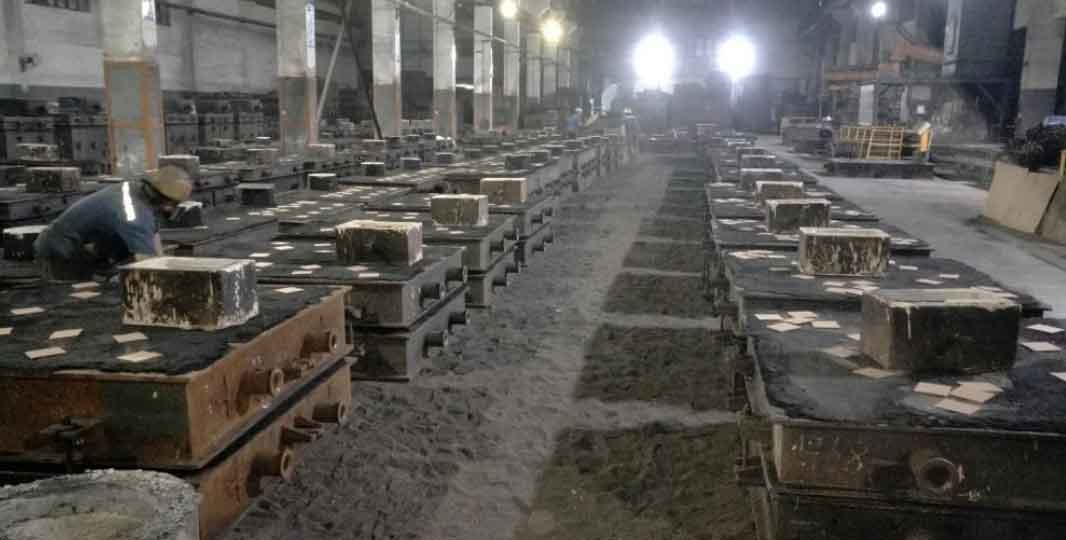
Sand casting is popular method for metal casting, primarily due to its ability to lower production costs in several key areas:
- Low-Cost Tooling: The molds used in sand casting are made from sand and bonding agents, which are significantly less expensive than the materials required for other types of casting molds, such as those used in die casting (which often involve high-grade steel). This makes it cheaper to create and replace molds, especially beneficial for small production runs or for producing large parts.
- Versatility and Reusability: Sand can be shaped into almost any form, making it ideal for sand casting complex shapes. After the metal has been cast and the part removed, the sand can often be recycled and reused to form new molds. This reusability factor reduces the need for continuous purchases of raw materials.
- Energy Efficiency: The temperatures required to melt metals for sand casting are generally lower compared to other high-precision casting processes, such as investment casting or die casting. This lower temperature requirement translates into less energy consumption, which not only lowers production costs but also minimizes the environmental impact.
- Reduced Waste: Sand casting typically generates less waste compared to other processes. Excess metal can be re-melted and reused, and the sand mold can often be recycled, minimizing waste disposal costs and reducing material costs through reuse.
- Simpler Machinery and Equipment: The equipment required for sand casting is generally less sophisticated and therefore less expensive than that required for other casting methods. This simplicity extends to maintenance costs, which are also lower, further reducing the overall cost of production.
- Flexibility in Material Selection: Sand casting allows for a wide range of metals to be used, including iron, steel, aluminum, bronze, and others. This flexibility can lead to cost savings if a less expensive metal can be substituted without compromising the integrity of the part.
- Lower Labor Costs: Although sand casting can be labor-intensive, it typically does not require as highly skilled labor as some other casting methods. Moreover, the process can be semi-automated, reducing labor costs while maintaining production efficiency.
- Quick Setup and Turnaround: The preparation time for making sand molds is relatively short, especially when compared to the time required to manufacture molds for more complex casting methods like injection molding or die casting. This quick setup allows for faster turnaround times on projects, which can be crucial for meeting production deadlines and reducing overall project costs.
- Adaptability to Changes: Changes to a design can be made relatively easily and at a low cost in sand casting. Adjustments often require simple modifications to the sand mold, which is far less expensive than modifying hard tooling used in other casting processes. This adaptability is particularly valuable in the prototyping phase or when customizing products for specific applications.
- Economical for Small to Medium Batch Production: Sand casting is exceptionally cost-effective for small to medium batch production. It doesn’t require large upfront investments for tooling and setup, making it economically viable for smaller quantities that would not justify the higher costs of permanent mold or die casting processes.
- Lower Cost of Defects and Errors: In case of defects or errors in sand casting, the cost of remaking a sand mold is minimal compared to the costs involved in scrapping and redoing parts in more expensive mold materials like steel. This aspect reduces the financial risk associated with the manufacturing of new or complex parts.
- Scalability: While sand casting is often associated with lower and medium volume production, it also offers scalability. As demand increases, the production can be ramped up with relatively low incremental costs compared to setting up additional production lines in other casting methods.
- Lower Material Restrictions: Unlike some other casting methods that require specific alloys or materials to ensure the integrity of the mold, sand casting does not impose such restrictions. This freedom allows manufacturers to opt for cheaper materials without the concern for the compatibility of the mold material.
- Global Availability of Materials: The basic materials used in sand casting, primarily sand and basic binding agents, are globally available and inexpensive. This universal availability helps in keeping the input costs low and reduces the dependency on specialized or costly imports.
- Integration with Other Manufacturing Processes: Sand casting is often used in conjunction with other manufacturing processes. For example, a rough sand casting might be completed before the part is finished with precision machining. This allows for the bulk of the material to be shaped at a lower cost through sand casting, with only critical dimensions being machined. This hybrid approach can reduce overall manufacturing costs while still achieving the necessary specifications.
- Reduced Transportation Costs: Because sand and basic binders are widely available, manufacturers can set up production close to where the materials are sourced or where the final products are needed, reducing transportation costs. This local production capability is particularly advantageous for large or heavy items that would be costly to ship over long distances.
- Flexibility in Production Volume Adjustments: Sand casting processes can be easily scaled up or down without significant additional costs. This flexibility in adjusting production volumes helps manufacturers respond quickly to market demands without incurring significant financial risks or overheads.
- Minimal Rework for Design Errors: The ease of altering sand molds means that design errors can often be corrected without complete retooling, minimizing the time and cost associated with rework. This is especially beneficial during the design and prototype stages, where iterative design changes are common.
- Accessibility for Custom or One-off Productions: For custom or one-off productions, such as bespoke components or restoration parts for vintage machinery, sand casting is a practical solution. It avoids the high costs associated with creating permanent molds for limited use, making it an economically sensible choice for specialized or low-volume items.
- Environmental and Regulatory Benefits: The ability to recycle and reuse sand in sand casting process not only cuts down on material costs but also aligns with environmental regulations and green manufacturing practices. This can result in savings related to waste management and disposal, and potentially leverage tax incentives for sustainable practices.
- Economic Tooling Modifications: Since the tooling involved in sand casting (the pattern and the sand mold) is relatively inexpensive and quick to produce, it allows for economic modifications. This can be crucial when adapting to changing market needs or updating product designs without significant financial impact.
- Long-term Durability of Tooling: Although sand molds are generally used for one casting, the patterns used to shape these molds can last for many years if properly maintained. This reduces the need for frequent tooling replacements and spreads the cost of pattern creation over many parts, contributing to lower per-unit costs over time.
By combining these factors, sand casting proves to be a versatile and economically advantageous method of production, particularly suitable for industries and projects where cost efficiency is paramount without the need for ultra-precise dimensional tolerances. This makes it a favorite choice among a wide range of industries from automotive and industrial machinery to sculptures and historical restorations.
Through these multiple facets, sand casting not only keeps initial investment and ongoing production costs low but also offers operational flexibility, making it a valuable technique for a wide range of applications and industries. Its cost-effectiveness is particularly crucial for maintaining competitive pricing in markets where margins are tight.