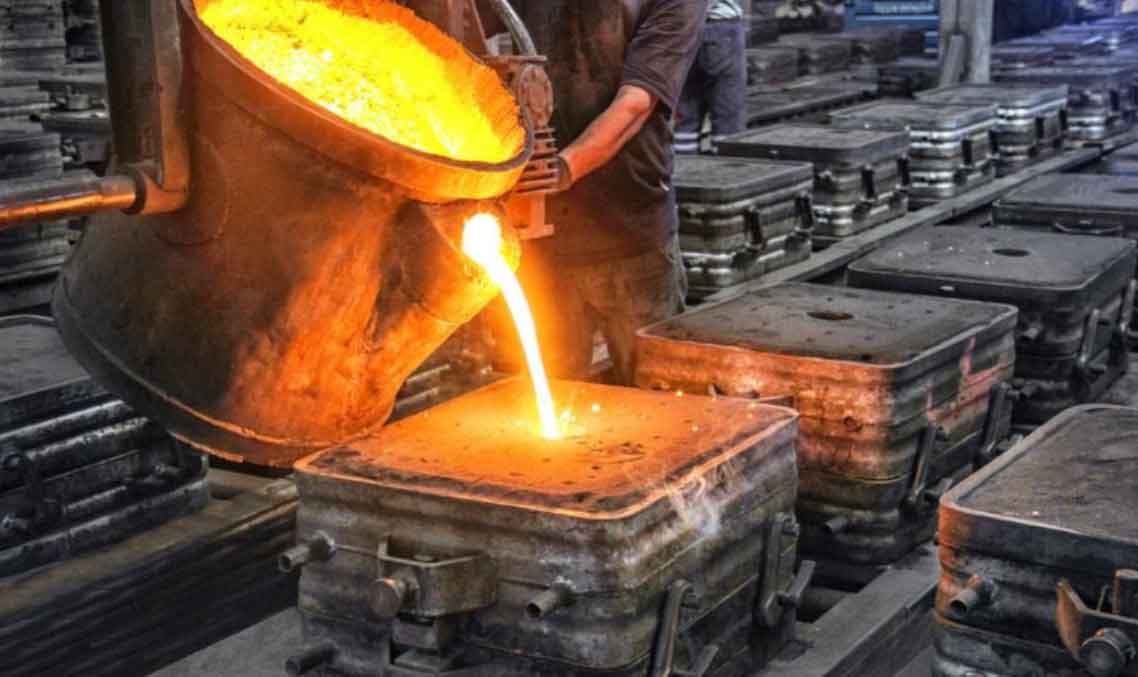
Chapter 1: Production Capacity of Sand Casting Manufacturers
The production capacity of sand casting manufacturers can vary widely based on factors such as the size of the foundry, available resources, equipment, and the complexity of the castings being produced. It’s important to note that specific production capacity details may differ from one manufacturer to another. Here’s a general overview of the production capacity aspects you might encounter:
Number of Castings per Day/Year:
- The number of castings a manufacturer can produce per day or year depends on factors such as the size of the casting, the type of sand casting process (green sand, resin sand, etc.), and the efficiency of the production line.
- Larger foundries with advanced equipment and automation might have higher daily or annual production rates compared to smaller facilities.
Specification Range:
- Sand casting manufacturers can produce a wide range of castings, from small components to large and complex parts. The size, weight, geometry, and material of the casting can influence the manufacturer’s capability to produce it.
- The manufacturer’s expertise and equipment, such as the size of the molding boxes and the lifting capacity of cranes, also play a role in determining the specification range.
Production Capacity:
- The production capacity of a sand casting manufacturer is often measured in terms of the tons of metal poured per year. This metric accounts for the volume and weight of the castings produced.
- A manufacturer’s production capacity might be influenced by factors like available furnace capacity, the number of molds produced per hour, and the overall efficiency of the casting process.
It’s important to communicate directly with sand casting manufacturers to get precise information about their production capacity. They can provide you with detailed insights into their capabilities, including the specific types of castings they excel at, the size ranges they can accommodate, and the average output per day or year.
When considering a sand casting manufacturer for your project, make sure to provide clear specifications and requirements so that they can assess whether their production capacity aligns with your needs. Additionally, inquire about their quality control processes, lead times, and any specialized services they offer to ensure a successful partnership.
Chapter 2: Equipment and Technology Owned by Sand Casting Manufacturers
Sand casting manufacturers employ a variety of equipment and technology to carry out the sand casting process efficiently and produce high-quality castings. The specific equipment and technology they possess can vary based on their size, specialization, and technological advancements. Here’s an overview of some common equipment used by sand casting manufacturers:
Smelting Furnaces:
- Induction Furnaces: These furnaces use electromagnetic induction to heat metal to its melting point. They offer precise temperature control and energy efficiency.
- Cupola Furnaces: Traditional cupola furnaces are used for melting iron. They are cost-effective for high-volume production.
- Electric Arc Furnaces (EAF): EAFs are used for melting steel scrap and other raw materials. They are common in steel foundries.
Mold Preparation Equipment:
- Molding Machines: Mechanized molding machines automate the creation of molds, ensuring consistent mold quality and production efficiency.
- Molding Boxes: These are used to create the mold cavities. Different sizes and types of molding boxes are used to accommodate various casting sizes and shapes.
- Sand Mixers: Sand mixers blend sand with binders to create the molding sand used to form the molds.
Core Production Equipment:
- Core Shooters: These machines produce sand cores used to create internal cavities in castings. They ensure precise core dimensions and complex geometries.
- Core Ovens: Ovens cure the sand cores, ensuring their strength and dimensional stability before they are placed in the mold.
Melting and Pouring Equipment:
- Ladles: Ladles are used to transfer molten metal from the furnace to the mold. They are designed to handle different types of metals and alloys.
- Pouring Systems: Automated pouring systems ensure accurate and controlled pouring of molten metal into the mold.
Shakeout and Cleaning Equipment:
- Shakeout Machines: These machines remove the sand from the solidified casting after it has cooled. They are essential for separating the casting from the mold material.
- Shot Blasting Equipment: Shot blasting cleans and removes residual sand from the castings, improving surface finish and preparing them for further processing.
Quality Control and Inspection Equipment:
- X-Ray and Ultrasonic Testing: Advanced testing methods are used to inspect castings for defects and ensure quality.
- Coordinate Measuring Machines (CMM): CMMs are used to measure and verify the dimensional accuracy of castings.
Automation and Digital Technology:
- Some modern sand casting manufacturers use digital technology and automation for process monitoring, data analysis, and optimization.
It’s important to communicate with sand casting manufacturers directly to understand the specific equipment and technology they have available. A well-equipped manufacturer with modern technology and a comprehensive range of equipment is more likely to meet diverse casting needs, produce high-quality components, and provide efficient and reliable services.
Chapter 3: The Process Control Level of Sand Casting Factory
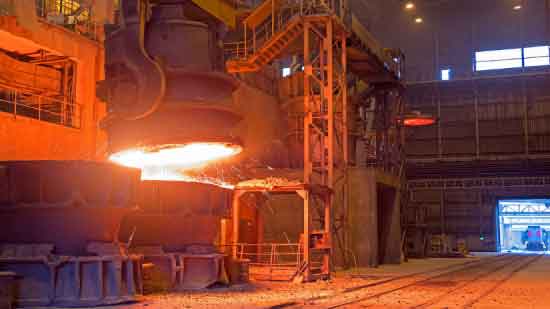
The process control level of sand casting manufacturers refers to the techniques and methods they employ to ensure consistency, quality, and efficiency throughout the sand casting process. Here are some key aspects of process control in sand casting:
Metal Melting:
- Temperature Control: Manufacturers use advanced temperature monitoring and control systems to achieve precise melting temperatures for different metals and alloys. This helps ensure the desired properties of the molten metal.
- Alloy Composition: Spectrographic analysis is used to verify the composition of the molten metal, ensuring it meets the required specifications.
Pouring:
- Pouring Rate and Speed: Manufacturers control the rate and speed of pouring to achieve proper filling of the mold cavity without causing turbulence that could lead to defects.
- Gating System: Proper design of the gating system, including sprues, runners, and gates, is essential for controlling the flow of molten metal into the mold.
Cooling and Solidification:
- Cooling Rate: Manufacturers monitor and control the cooling rate to ensure uniform solidification and prevent the formation of defects like shrinkage cavities.
- Chills and Insulation: Chills and insulating materials are strategically placed to control the cooling rate in specific areas of the casting, optimizing the microstructure.
Mold Preparation and Sand Control:
- Sand Properties: Manufacturers monitor and adjust the properties of the molding sand, such as moisture content and compactability, to achieve consistent mold quality.
- Molding Parameters: Automation and computer-controlled molding machines ensure accurate molding parameters and reduce human variability.
Core Production:
- Core Placement: Precise core placement within the mold is crucial for achieving complex geometries and ensuring the integrity of the final casting.
- Core Binder Control: Manufacturers monitor and control core binders to achieve proper curing and prevent defects.
Quality Control and Inspection:
- Non-Destructive Testing (NDT): Techniques like X-ray, ultrasonic testing, and dye penetrant inspection are used to detect defects and ensure casting integrity.
- Dimensional Inspection: Coordinate measuring machines (CMM) and other measurement tools are used to verify the dimensional accuracy of castings.
Data Monitoring and Analysis:
- Some manufacturers use data monitoring and analysis tools to track process parameters in real-time, identifying trends and deviations that could affect casting quality.
Automation and Robotics:
- Automation and robotics can be employed to enhance process control, ensuring consistent and repeatable operations.
Manufacturers that have a high level of process control utilize a combination of advanced technology, skilled personnel, and strict quality assurance practices to ensure that each step of the sand casting process is well-managed and optimized. This ultimately leads to the production of high-quality castings with minimal defects and consistent properties.
Chapter 4: The Quality Control System of Sand Casting Manufacturers
Quality control is a critical aspect of sand casting manufacturing to ensure the production of high-quality castings. Sand casting manufacturers implement various techniques and methods to assess and verify the quality of their products. Here’s an overview of quality control practices commonly used in the industry:
Non-Destructive Testing (NDT):
- X-ray Testing: X-ray inspections are used to detect internal defects such as porosity, inclusions, and voids within the casting.
- Ultrasonic Testing: Ultrasonic waves are used to identify defects and irregularities in the casting’s internal structure.
- Magnetic Particle Testing: This method detects surface and near-surface defects by applying magnetic particles to the casting and observing their behavior.
Dimensional Measurement:
- Coordinate Measuring Machines (CMM): CMMs are used to measure the dimensions and geometrical features of castings, ensuring they meet design specifications.
- Optical Metrology: Optical measurement systems use cameras and lasers to capture and analyze the surface profiles and dimensions of castings.
Metallographic Analysis:
- Microscopy: Metallographic microscopes are used to examine the microstructure of castings, revealing information about grain size, phase composition, and defects.
- Etching: Chemical etching is used to reveal the microstructure of castings, helping identify issues like segregation and inclusions.
Hardness Testing:
- Hardness tests determine the hardness of the casting’s surface, which can provide insights into its mechanical properties and material composition.
Visual Inspection:
- Skilled inspectors visually examine castings for surface defects, such as cracks, roughness, and incomplete filling of the mold.
Mechanical Testing:
- Tensile Testing: Tensile tests measure the casting’s tensile strength, yield strength, and elongation, providing valuable mechanical property data.
- Impact Testing: Impact tests assess the casting’s ability to withstand sudden loads and shocks.
Chemical Analysis:
- Spectrographic analysis is used to verify the composition of the casting’s material, ensuring it meets the required specifications.
Documentation and Traceability:
- Manufacturers maintain detailed records of each casting’s production process, including material used, process parameters, and inspection results, to ensure traceability and quality consistency.
Quality Management Systems:
- Sand casting manufacturers may be certified under quality management standards such as ISO 9001 to demonstrate their commitment to quality control.
Implementing a robust quality control system ensures that castings meet the required standards, specifications, and performance criteria. This systematic approach helps identify and address defects and deviations early in the production process, leading to improved overall quality, reduced scrap rates, and increased customer satisfaction. When evaluating sand casting manufacturers, it’s essential to inquire about their quality control practices and certifications to ensure that they have the necessary systems in place to deliver high-quality castings.
Chapter 5: Skill level of employees in sand casting factories
The skill level and training plan of employees in sand casting manufacturers play a crucial role in ensuring the quality, efficiency, and success of the casting process. Different roles within the manufacturing process require specific skills and training to perform their tasks effectively. Here’s an overview of the skill levels and training plans for various roles within sand casting manufacturers:
Operators:
- Operators are responsible for operating and maintaining the casting equipment, such as molding machines, furnaces, and core shooters.
- Skill Level: Operators need a solid understanding of the casting process, equipment operation, and safety protocols. They should be skilled in tasks like mold preparation, metal pouring, and shakeout.
- Training: Operators typically undergo on-the-job training and may participate in workshops or courses on equipment operation, safety practices, and process control.
Molders and Core Makers:
- Molders create molds from sand and other materials, while core makers produce sand cores used in the casting process.
- Skill Level: Molders and core makers need a deep understanding of sand properties, mold design, and core production techniques. They should be skilled in achieving precise mold dimensions and ensuring proper core placement.
- Training: Training for molders and core makers includes learning about sand mixtures, molding techniques, and core production methods. Apprenticeships or mentoring programs are common in this field.
Foundry Engineers:
- Foundry engineers oversee the entire casting process, from design and material selection to process optimization and quality control.
- Skill Level: Foundry engineers require strong knowledge of metallurgy, casting techniques, process optimization, and quality assurance.
- Training: Foundry engineers often have a bachelor’s or master’s degree in materials science, metallurgy, or a related field. They may also receive specialized training in casting technology and process improvement.
Quality Inspectors:
- Quality inspectors are responsible for inspecting castings for defects, ensuring they meet specifications and quality standards.
- Skill Level: Quality inspectors should have a keen eye for detail and a thorough understanding of casting defects, NDT methods, and quality control techniques.
- Training: Quality inspectors typically undergo training in NDT methods, dimensional measurement, and quality assurance practices. They may also receive certifications in specific inspection techniques.
Skilled Craftsmen:
- Skilled craftsmen, such as pattern makers and finishers, contribute to the production of high-quality castings by creating accurate patterns and finishing the final products.
- Skill Level: Skilled craftsmen need expertise in pattern making, gating system design, and finishing techniques to achieve the desired surface finish and dimensional accuracy.
- Training: Pattern makers often undergo apprenticeships or vocational training to learn the art of pattern making. Finishers may receive training in various surface finishing methods.
Training plans for employees in sand casting manufacturers may include a combination of formal education, on-the-job training, workshops, and continuous professional development. Successful manufacturers invest in their employees’ skills to ensure that they are equipped to handle the complexities of the casting process and deliver high-quality castings to customers.
Chapter 6: Previous Project Experience in Sand Casting Manufacturers
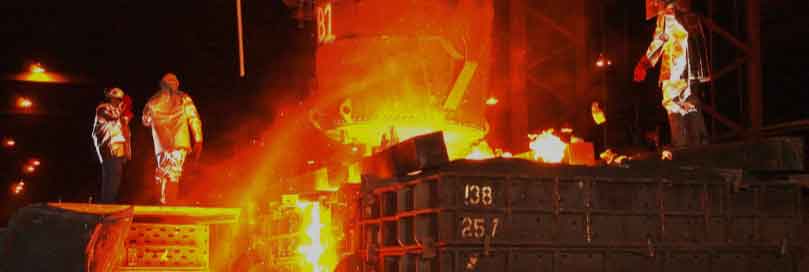
The past project experience of sand casting manufacturers provides valuable insights into their capabilities, expertise, and areas of specialization. Reviewing their previous projects can help you understand their strengths, areas of concern, and the types of applications they have successfully served. Here are some aspects to consider when evaluating the past project experience of sand casting manufacturers:
Types of Castings:
- Look at the range of castings they have produced, including size, complexity, and material. Consider whether they have experience with the types of castings you require for your project.
Industries Served:
- Identify the industries the manufacturer has worked with. This could include automotive, aerospace, defense, industrial machinery, and more. Experience in your industry may indicate a better understanding of your specific requirements.
Complexity of Projects:
- Assess the complexity of the castings they have produced. Have they successfully handled intricate and complex geometries? This is important if your project involves intricate designs.
Quality and Defect Rates:
- Inquire about their track record regarding casting defects and quality issues. A manufacturer with a low defect rate demonstrates a commitment to quality.
Customization and Prototyping:
- Have they been involved in custom casting solutions or prototyping projects? This indicates their ability to adapt to unique requirements and provide tailored solutions.
Production Volume:
- Consider their experience with both low-volume and high-volume production. If your project requires a specific production volume, their past experience in handling similar volumes is crucial.
Application-Related Projects:
- Look for projects that are similar to your intended application. For example, if you’re in the automotive industry, find out if they have successfully produced castings for automotive components.
Areas of Concern:
- While evaluating their past projects, pay attention to any areas of concern or challenges they might have faced. This can give you insight into their transparency and ability to address issues.
References and Testimonials:
- Request references or testimonials from their previous clients. This can provide firsthand feedback on their performance, communication, and project outcomes.
It’s important to have open and detailed discussions with the sand casting manufacturers to understand their project experience fully. Sharing the specifics of your project and requirements will help them provide relevant examples from their past work. Additionally, visiting their facility, if possible, can give you a better understanding of their operations and capabilities.
Chapter 7: Supply Chain Management Capabilities of Sand Casting Manufacturers
Inspecting the supply chain management capabilities of sand casting manufacturers is crucial to ensuring a smooth and efficient production process. Here are key aspects to consider when evaluating their supply chain management capabilities:
Raw Material Procurement:
- Inquire about their sources of raw materials (metals, alloys, sand, binders, etc.). Do they have established relationships with reputable suppliers?
- Check if they perform material testing and verification to ensure the quality and consistency of raw materials.
Inventory Management:
- Ask about their inventory practices. Do they maintain an adequate stock of raw materials to avoid production delays?
- Inquire about their approach to managing surplus materials and waste.
Production Scheduling and Planning:
- Understand their production scheduling methods. How do they prioritize and schedule orders?
- Are they able to accommodate rush orders or last-minute changes in production schedules?
Capacity Management:
- Assess their production capacity and flexibility. Can they handle varying production volumes and demands?
- Inquire about their ability to scale up or down based on project requirements.
Lead Times:
- Ask about typical lead times for different types of castings. Are they able to meet your project’s timelines?
Quality Control and Inspection:
- Inquire about their quality control and inspection processes at different stages of production. How do they ensure that each casting meets quality standards?
Logistics and Delivery:
- Understand their delivery capabilities. Do they have a reliable logistics network for timely and safe transportation of finished castings?
- Inquire about their track record of on-time deliveries and their approach to handling shipping and delivery challenges.
Communication and Collaboration:
- Evaluate their communication channels and willingness to collaborate. Do they provide regular updates on order status and potential issues?
- Consider their responsiveness to inquiries, changes, and concerns.
Risk Management:
- Ask about their approach to mitigating supply chain risks, such as disruptions in raw material supply or transportation delays.
Environmental and Sustainability Practices:
- Inquire about their efforts to reduce waste, optimize energy usage, and minimize the environmental impact of their supply chain.
Certifications and Compliance:
- Check if they have relevant certifications related to supply chain management, such as ISO 9001 for quality management.
A sand casting manufacturer with strong supply chain management capabilities can ensure that the right materials are available, production is optimized, and deliveries are made on time. A well-organized and efficient supply chain contributes to smoother operations, reduced lead times, and higher customer satisfaction.
Chapter 8: Certification Related to Sand Casting Manufacturers
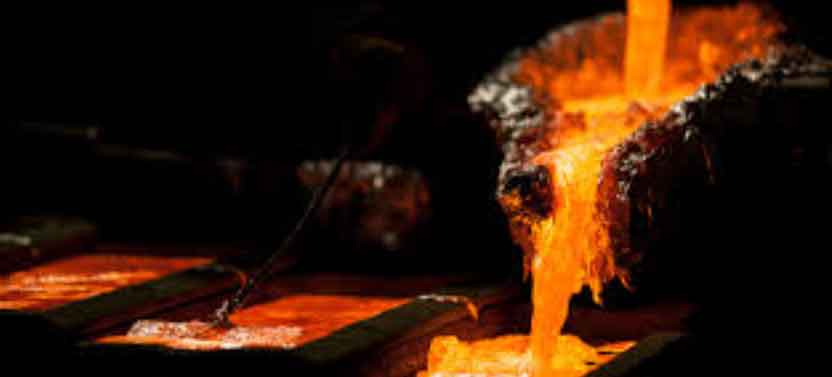
Evaluating the certifications and industry standards compliance of sand casting manufacturers is essential to ensuring their commitment to quality, safety, and best practices. Here are some relevant certifications and standards to consider:
ISO 9001:
- ISO 9001 is a globally recognized standard for quality management systems. It demonstrates the manufacturer’s dedication to consistently delivering products that meet customer requirements and adhere to regulatory standards.
ISO 14001:
- ISO 14001 focuses on environmental management systems, indicating the manufacturer’s commitment to minimizing environmental impact, reducing waste, and promoting sustainability.
ISO 45001:
- ISO 45001 is related to occupational health and safety management. Manufacturers with this certification prioritize the safety and well-being of their employees and stakeholders.
AS9100 (for Aerospace):
- AS9100 is a quality management system standard specifically tailored to the aerospace industry. It ensures compliance with rigorous aerospace and defense industry requirements.
NADCAP (for Aerospace and Defense):
- The National Aerospace and Defense Contractors Accreditation Program (NADCAP) ensures that manufacturers in the aerospace and defense industries meet industry-specific quality and process standards.
ISO/TS 16949 (for Automotive):
- ISO/TS 16949 is a quality management system standard for the automotive industry, demonstrating the manufacturer’s capability to meet automotive industry requirements.
API Q1 (for Oil and Gas):
- API Q1 is a quality management system standard for organizations involved in the oil and gas industry, emphasizing risk management, quality control, and process improvement.
AWS D1.1 (for Welding):
- The American Welding Society (AWS) D1.1 certification ensures that welding procedures and practices meet industry standards.
Certifications for Non-Destructive Testing (NDT):
- Depending on the industry and applications, certifications such as ASNT Level II or III for various NDT methods (ultrasonic testing, radiographic testing, magnetic particle testing, etc.) may be relevant.
Local and National Regulations:
- Ensure that the manufacturer complies with relevant local and national regulations, safety standards, and environmental regulations.
When evaluating sand casting manufacturers, inquire about their certifications and standards compliance. Request documentation and evidence of their certifications, and verify their authenticity with relevant certifying bodies if necessary. A manufacturer with the appropriate certifications and industry standards compliance demonstrates a commitment to quality, safety, and continuous improvement.
Chapter 9: Closer Look at Sand Casting Manufacturers Industry Insights and Trends
1. Automation and Robotics:
- Automation and robotics have continued to play a significant role in sand casting foundries. Manufacturers are increasingly adopting automated systems for various tasks, such as mold handling, pouring, and finishing. Robotics enhance productivity, improve consistency, and reduce the reliance on manual labor, leading to cost savings and higher efficiency.
2. Sustainability and Eco-Friendly Practices:
- Sustainability and eco-friendly practices have become essential considerations for sand casting manufacturers. Foundries are adopting measures to reduce energy consumption, implement waste recycling and reclamation, and minimize emissions to create a more environmentally responsible manufacturing process.
3. Additive Manufacturing Integration:
- Additive manufacturing, such as 3D printing, is increasingly being integrated into the sand casting process. 3D-printed sand molds and cores offer enhanced design flexibility, faster prototyping, and the ability to create complex geometries that were previously challenging with traditional methods.
4. Simulation and Digitalization:
- The use of simulation software and digitalization in sand casting has gained momentum. Manufacturers are using advanced simulation tools to optimize mold design, predict casting defects, and improve casting quality. Digital process control systems enable real-time data monitoring, leading to better process optimization and reduced material wastage.
5. Materials and Alloys:
- Sand casting manufacturers are continuously exploring new materials and alloys to meet the evolving demands of various industries. The development of high-performance alloys and metal composites expands the range of applications for sand casting.
6. Lean Manufacturing and Continuous Improvement:
- Lean manufacturing principles and continuous improvement methodologies are being adopted by sand casting manufacturers to enhance efficiency, reduce waste, and optimize production processes. This approach allows foundries to remain competitive and responsive to market demands.
7. Quality Assurance and Certifications:
- Quality assurance remains a top priority for sand casting manufacturers. Many foundries obtain certifications like ISO 9001 to demonstrate their commitment to high-quality production processes.
8. Collaborative Design and Engineering:
- Collaborative design and engineering practices have become more prevalent, with manufacturers working closely with customers and using advanced design tools to optimize casting designs for cost-effectiveness and performance.
9. Globalization and Outsourcing:
- The sand casting industry has seen continued globalization, with manufacturers seeking opportunities for cost-effective production and new markets. Outsourcing of casting production to specialized foundries has become common, particularly for industries seeking highly complex and large-scale castings.
It’s important to note that the sand casting industry is continuously evolving, and new trends and innovations may have emerged since my last update. Manufacturers that embrace technology, sustainability, and continuous improvement are likely to remain competitive and successful in the ever-changing sand casting market.