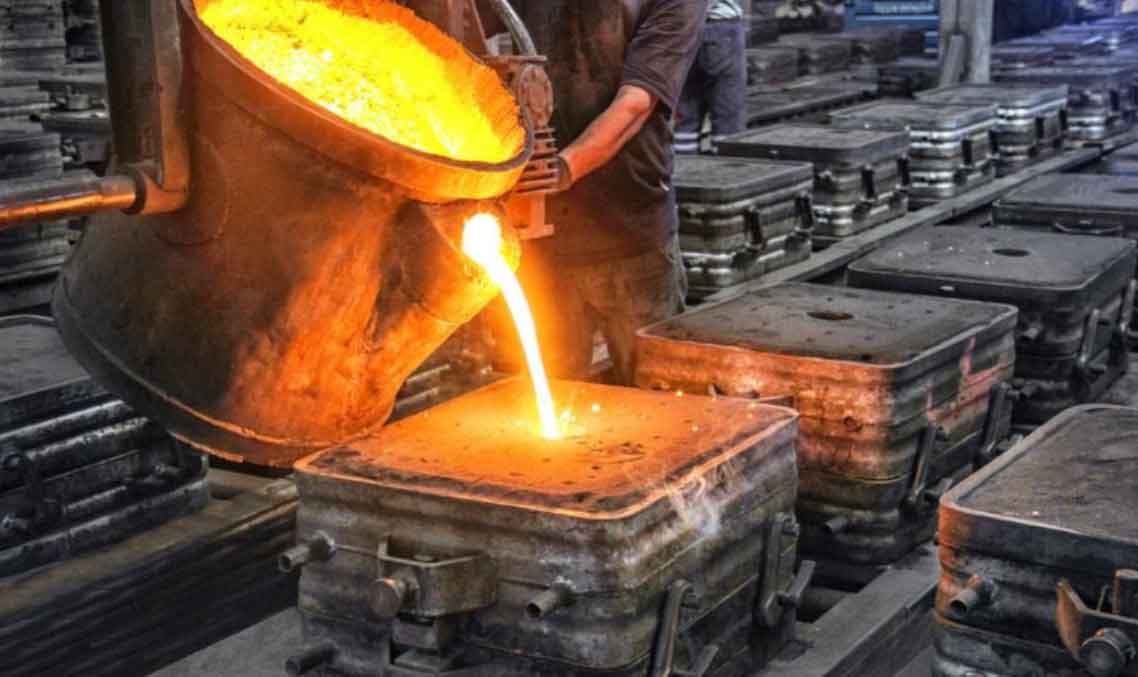
Sand casting manufacturers are continuously driven by the pursuit of innovation to push the boundaries in metalwork. Embracing new technologies, materials, and processes allows them to enhance production capabilities, improve casting quality, and expand the range of applications. Here are some ways in which sand casting manufacturers are pushing the boundaries in metalwork:
1. Advanced Simulation and Digital Twin Technology:
- Manufacturers are leveraging advanced simulation software and digital twin technology to optimize casting designs and predict casting defects. Digital twins allow for virtual experimentation, enabling manufacturers to refine processes before physical production.
2. Additive Manufacturing Integration:
- Integrating additive manufacturing (3D printing) with sand casting allows manufacturers to create complex patterns, cores, and molds with unprecedented design freedom. This combination enables rapid prototyping and the production of intricate geometries.
3. High-Performance Alloys and Metal Composites:
- Sand casting manufacturers are exploring the use of high-performance alloys and metal composites to meet the demands of modern industries. These materials offer enhanced strength, corrosion resistance, and other specific properties for critical applications.
4. Sustainable and Eco-Friendly Practices:
- The focus on sustainability drives sand casting manufacturers to implement eco-friendly practices. This includes sand reclamation and recycling, using environmentally friendly binders, and reducing energy consumption.
5. Automation and Robotics:
- Manufacturers are increasingly integrating automation and robotics into various stages of the sand casting process. This allows for improved precision, efficiency, and productivity, leading to cost savings and consistent quality.
6. Real-Time Process Monitoring:
- Utilizing sensors and real-time process monitoring systems provides manufacturers with valuable insights into production conditions. This data-driven approach helps optimize processes, reduce defects, and ensure consistent casting quality.
7. Energy-Efficient Melting and Casting:
- Advancements in energy-efficient melting technologies, such as induction furnaces and electric arc furnaces, contribute to reducing the environmental impact and production costs.
8. Collaboration with Customers and Research Institutions:
- Sand casting manufacturers actively collaborate with customers, research institutions, and industry partners to develop innovative solutions for specific applications. These collaborations foster knowledge exchange and drive continuous improvement.
9. Customization and Tailored Solutions:
- Manufacturers are offering more tailored solutions to meet the unique requirements of their customers. This includes customization of casting processes, materials, and finishing techniques to address specific challenges.
10. Investment in Research and Development:
- Manufacturers prioritize research and development efforts to explore new technologies and techniques that can revolutionize the sand casting industry. This includes investing in advanced equipment, software, and talent to stay at the forefront of innovation.
By embracing innovation and pushing the boundaries in metalwork, sand casting manufacturers contribute to the advancement of various industries. Their commitment to continuous improvement ensures that sand casting remains a relevant and versatile casting method for diverse applications in the ever-evolving manufacturing landscape.