Grey cast iron is widely used material known for its excellent castability, machinability, and vibration damping properties. However, its inherent brittleness poses challenges for applications requiring high fracture toughness. Alloying elements play a crucial role in modifying the microstructure of grey cast iron, thereby enhancing its fracture toughness. This article explores the impact of various alloying elements on the fracture toughness of grey cast iron, providing insights into their effects and optimal usage.
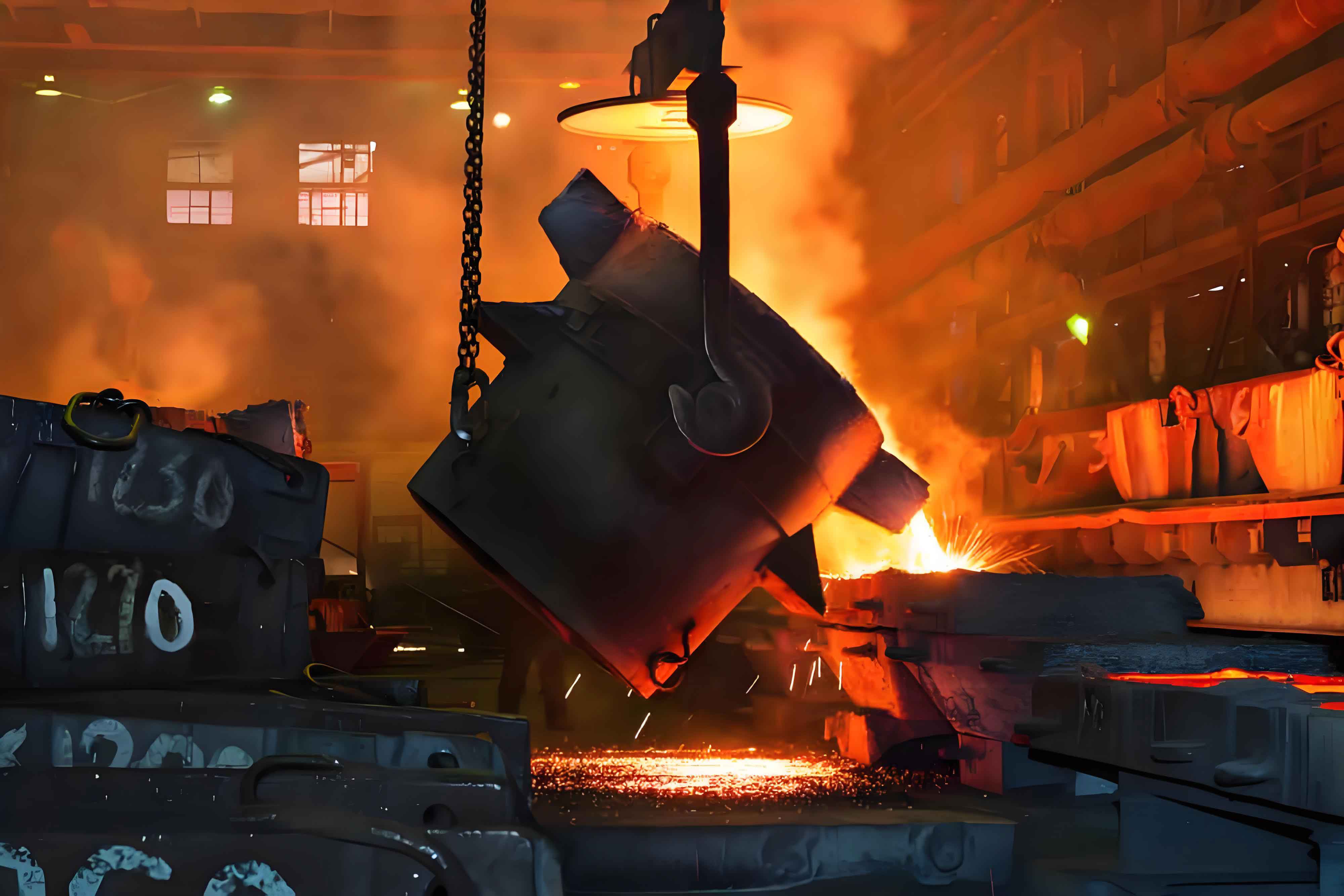
Introduction
Fracture toughness is a critical property that determines a material’s ability to resist crack propagation under stress. For grey cast iron, achieving high fracture toughness is essential for its performance in demanding applications such as automotive components, machinery, and structural parts. The presence of graphite flakes in grey cast iron’s microstructure can act as stress concentrators, making it prone to cracking. Alloying elements can help mitigate this issue by enhancing the material’s overall mechanical properties.
Key Alloying Elements and Their Effects
- Silicon (Si):
- Role: Silicon is primarily added to improve the castability and fluidity of grey cast iron. It also influences the formation and distribution of graphite flakes.
- Impact on Fracture Toughness: Silicon can enhance fracture toughness by promoting the formation of a ferritic matrix, which is more ductile. However, excessive silicon can lead to brittleness, reducing fracture toughness.
- Nickel (Ni):
- Role: Nickel is added to improve strength and toughness by stabilizing the austenitic phase and refining the pearlitic structure.
- Impact on Fracture Toughness: Nickel enhances fracture toughness by increasing the ductility and reducing the brittleness of the matrix. It also improves resistance to crack initiation and propagation.
- Molybdenum (Mo):
- Role: Molybdenum is used to increase hardenability and strength.
- Impact on Fracture Toughness: Molybdenum promotes the formation of a fine pearlitic or bainitic microstructure, which helps distribute stress more evenly and inhibit crack growth, thereby enhancing fracture toughness.
- Copper (Cu):
- Role: Copper is added to improve strength and hardness.
- Impact on Fracture Toughness: Copper can enhance fracture toughness by refining the matrix structure. However, excessive copper can lead to embrittlement, so it must be carefully controlled.
- Chromium (Cr):
- Role: Chromium is used to improve wear resistance and hardness.
- Impact on Fracture Toughness: Chromium enhances wear resistance but can reduce fracture toughness if present in high amounts due to the formation of hard carbides.
- Tin (Sn):
- Role: Tin is added to improve strength and hardness.
- Impact on Fracture Toughness: Small amounts of tin can enhance the matrix strength, but higher concentrations may increase brittleness, reducing fracture toughness.
Comparative Table of Alloying Elements and Their Effects
Alloying Element | Primary Role | Effect on Fracture Toughness | Optimal Range (wt%) |
---|---|---|---|
Silicon (Si) | Fluidity, castability | Moderate levels enhance; excessive levels reduce | 1.5 – 2.5 |
Nickel (Ni) | Toughness, strength | Enhances by refining pearlitic structure | 0.5 – 2.0 |
Molybdenum (Mo) | Hardenability, strength | Enhances by promoting fine pearlitic/bainitic structure | 0.2 – 0.5 |
Copper (Cu) | Strength, hardness | Moderate levels enhance; excessive levels reduce | 0.5 – 1.5 |
Chromium (Cr) | Wear resistance, hardness | Enhances wear resistance; high levels reduce toughness | 0.2 – 0.5 |
Tin (Sn) | Strength, hardness | Small amounts enhance; high levels reduce toughness | 0.05 – 0.1 |
Mechanisms of Improvement
- Silicon (Si):
- Silicon enhances the formation of a ferritic matrix, which is more ductile than a pearlitic matrix. This ductility improves the material’s ability to absorb energy before fracturing. However, excessive silicon can lead to brittleness, reducing fracture toughness.
- Nickel (Ni):
- Nickel refines the pearlitic or bainitic matrix, reducing the brittleness associated with graphite flakes. This refinement improves the material’s resistance to crack initiation and propagation, enhancing overall fracture toughness.
- Molybdenum (Mo):
- Molybdenum promotes a finer microstructure, which helps distribute stress more evenly across the material. This finer structure inhibits crack growth, improving fracture toughness.
- Copper (Cu):
- Copper improves the strength and hardness of the matrix, which can help prevent crack initiation. However, excessive copper can lead to embrittlement, so it must be carefully balanced.
- Chromium (Cr):
- Chromium improves wear resistance by forming hard carbides within the matrix. While beneficial for wear resistance, excessive chromium can reduce fracture toughness by making the matrix more brittle. Optimal levels are essential to balance these effects.
- Tin (Sn):
- Tin strengthens the matrix and refines the microstructure, but higher levels can increase brittleness. Small additions improve fracture toughness, while higher concentrations should be avoided.
Practical Implications and Applications
- Automotive Components:
- Engine Blocks and Cylinder Heads: Enhancing fracture toughness is crucial for components subjected to thermal cycling and mechanical stress. The addition of nickel and molybdenum can significantly improve the toughness of grey cast iron used in these parts, ensuring better performance and longevity.
- Industrial Machinery:
- Gears and Housings: Components such as gears and housings benefit from improved wear resistance and fracture toughness. A balanced addition of chromium and copper can enhance these properties, making grey cast iron suitable for heavy-duty applications.
- Construction Materials:
- Pipes and Fittings: Grey cast iron pipes and fittings used in construction need high fracture toughness to withstand internal pressures and external impacts. Alloying with silicon and nickel can improve the toughness and durability of these components.
Future Trends and Research
- Nanostructured Alloys:
- Research into nanostructured grey cast iron alloys aims to further enhance fracture toughness by refining the microstructure at the nanoscale. This approach could lead to significant improvements in mechanical properties.
- Additive Manufacturing:
- The development of additive manufacturing techniques for grey cast iron allows for the creation of complex geometries and optimized microstructures. This can improve fracture toughness by controlling the distribution and orientation of graphite flakes and alloying elements.
- Sustainable Alloying Practices:
- Using recycled materials and eco-friendly alloying elements can reduce the environmental impact of grey cast iron production while maintaining or improving its fracture toughness. Research into sustainable practices is ongoing to balance performance and environmental considerations.
Conclusion
The fracture toughness of grey cast iron can be significantly enhanced through the careful selection and optimization of alloying elements. By understanding the roles and effects of elements such as silicon, nickel, molybdenum, copper, chromium, and tin, manufacturers can improve the mechanical properties of grey cast iron to meet the demands of various applications. Ongoing research and technological advancements will continue to provide new solutions and enhance the performance of grey cast iron in the future.