Spheroidal graphite cast iron (SG iron), also known as ductile iron, is a versatile material widely used in various industries due to its superior mechanical properties, such as high strength, ductility, and wear resistance. The addition of alloying elements plays a crucial role in enhancing the microstructure and performance of spheroidal graphite cast iron. This article explores the impact of different alloying elements on spheroidal graphite cast iron, providing detailed insights into how they influence its properties and performance. Comprehensive tables and lists are included to enhance understanding.
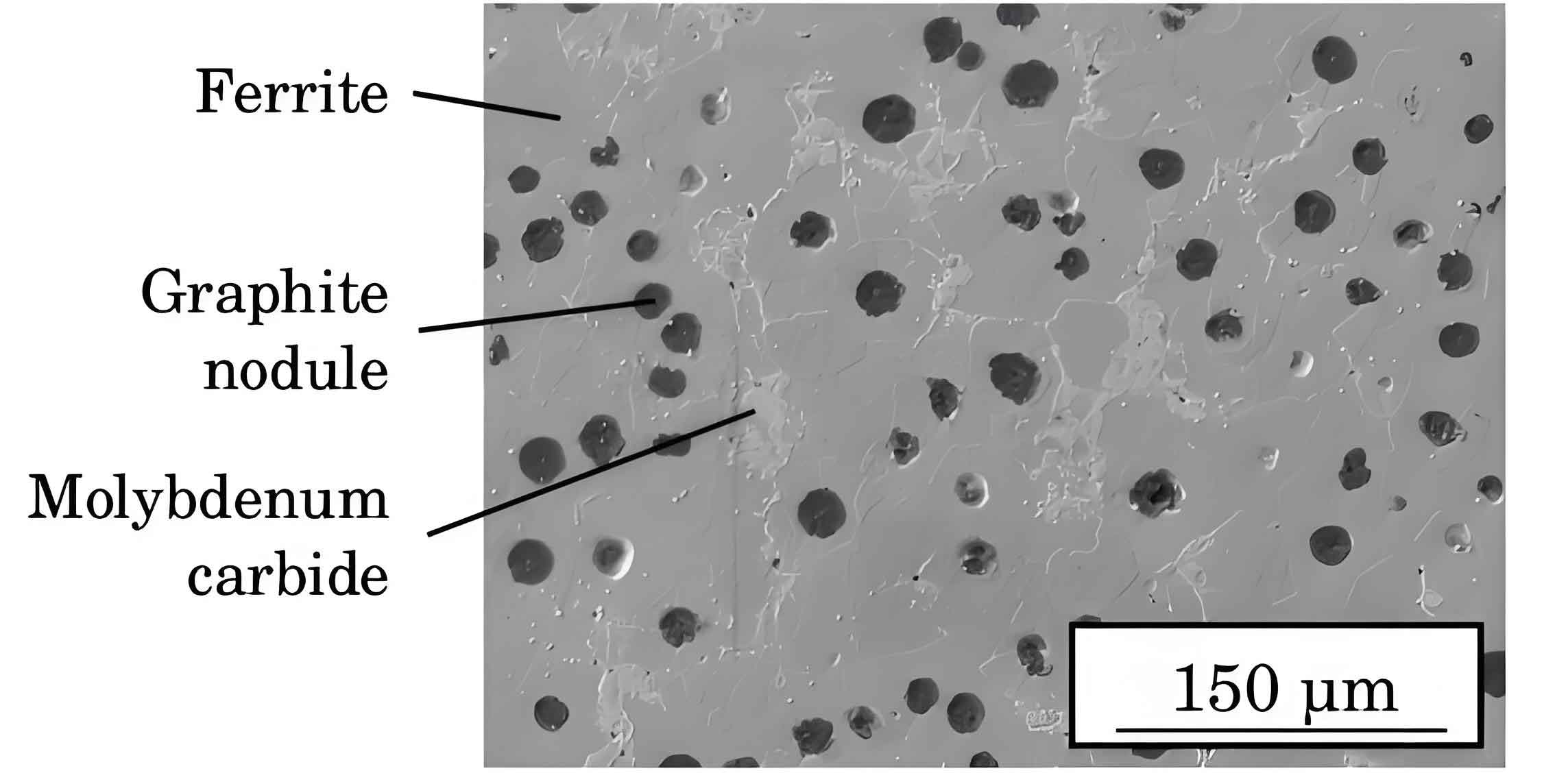
Introduction
Spheroidal graphite cast iron is characterized by the presence of graphite in the form of spheroids, which imparts significant mechanical benefits compared to traditional gray iron. The mechanical properties of spheroidal graphite cast iron can be tailored by adjusting its chemical composition through the addition of various alloying elements. These elements affect the microstructure, including the size and distribution of graphite nodules and the matrix phase, which in turn influence the overall performance of the material.
Key Alloying Elements and Their Effects
- Carbon (C):
- Role: Primary element for graphite formation.
- Effect: Higher carbon content increases the number of graphite nodules, improving ductility but may reduce strength if excessive.
- Silicon (Si):
- Role: Promotes graphite formation and enhances ferritic matrix.
- Effect: Increases ductility and corrosion resistance but can decrease strength at high levels.
- Magnesium (Mg):
- Role: Essential for nodulizing graphite.
- Effect: Converts flake graphite to spheroidal form, improving strength and ductility.
- Nickel (Ni):
- Role: Stabilizes austenite and improves toughness.
- Effect: Enhances low-temperature toughness and corrosion resistance.
- Copper (Cu):
- Role: Strengthening element.
- Effect: Increases tensile strength and hardness, may reduce ductility.
- Manganese (Mn):
- Role: Deoxidizer and sulfur scavenger.
- Effect: Improves strength and hardness but can promote carbide formation if excessive.
- Chromium (Cr):
- Role: Increases hardenability and wear resistance.
- Effect: Enhances wear resistance and hardness, but may reduce ductility if high.
- Molybdenum (Mo):
- Role: Strengthens ferrite and pearlite.
- Effect: Increases high-temperature strength and hardness, enhances resistance to thermal fatigue.
- Tin (Sn):
- Role: Pearlite stabilizer.
- Effect: Increases strength and hardness by promoting pearlitic matrix.
- Cerium (Ce) and Rare Earth Elements:
- Role: Assist in nodulization process.
- Effect: Improve nodule formation, reduce sensitivity to impurities.
Table: Impact of Alloying Elements on Spheroidal Graphite Cast Iron
Element | Role | Effect |
---|---|---|
Carbon (C) | Primary element for graphite formation | Increases nodule count, improves ductility, may reduce strength if excessive |
Silicon (Si) | Promotes graphite formation, enhances ferritic matrix | Increases ductility and corrosion resistance, decreases strength at high levels |
Magnesium (Mg) | Essential for nodulizing graphite | Converts flake graphite to spheroidal form, improves strength and ductility |
Nickel (Ni) | Stabilizes austenite, improves toughness | Enhances low-temperature toughness, corrosion resistance |
Copper (Cu) | Strengthening element | Increases tensile strength, hardness, may reduce ductility |
Manganese (Mn) | Deoxidizer, sulfur scavenger | Improves strength, hardness, may promote carbide formation if excessive |
Chromium (Cr) | Increases hardenability, wear resistance | Enhances wear resistance, hardness, may reduce ductility if high |
Molybdenum (Mo) | Strengthens ferrite, pearlite | Increases high-temperature strength, hardness, thermal fatigue resistance |
Tin (Sn) | Pearlite stabilizer | Increases strength, hardness by promoting pearlitic matrix |
Cerium (Ce) and Rare Earth Elements | Assist in nodulization process | Improve nodule formation, reduce sensitivity to impurities |
Influence on Microstructure
- Graphite Nodule Formation:
- Carbon and Magnesium: Primary agents in forming spheroidal graphite.
- Cerium and Rare Earth Elements: Aid in achieving uniform nodule distribution.
- Matrix Composition:
- Silicon and Nickel: Promote a ferritic matrix, enhancing ductility.
- Copper, Tin, and Chromium: Stabilize pearlite, increasing strength and hardness.
- Molybdenum: Strengthens both ferritic and pearlitic matrices, improving high-temperature performance.
- Carbide Formation:
- Manganese and Chromium: High levels can lead to carbide formation, affecting machinability and toughness.
List: Key Effects of Alloying Elements on Microstructure
- Graphite Nodule Formation:
- Enhanced by carbon, magnesium, cerium, and rare earth elements.
- Matrix Composition:
- Ferritic matrix: Promoted by silicon and nickel.
- Pearlitic matrix: Stabilized by copper, tin, and chromium.
- Carbide Formation:
- Increased by high levels of manganese and chromium.
Performance Enhancements
- Mechanical Properties:
- Strength and Hardness: Increased by copper, chromium, tin, and molybdenum.
- Ductility: Enhanced by magnesium, silicon, and nickel.
- Wear Resistance:
- Chromium and Molybdenum: Significantly improve wear resistance.
- Corrosion Resistance:
- Nickel and Silicon: Enhance corrosion resistance, making spheroidal graphite cast iron suitable for harsh environments.
- Thermal Stability:
- Molybdenum and Chromium: Improve high-temperature performance and resistance to thermal fatigue.
Table: Performance Enhancements Due to Alloying Elements
Property | Enhancing Elements | Impact |
---|---|---|
Strength and Hardness | Copper, Chromium, Tin, Molybdenum | Increased tensile strength and hardness |
Ductility | Magnesium, Silicon, Nickel | Enhanced ductility |
Wear Resistance | Chromium, Molybdenum | Improved wear resistance |
Corrosion Resistance | Nickel, Silicon | Enhanced corrosion resistance |
Thermal Stability | Molybdenum, Chromium | Improved high-temperature performance, resistance to thermal fatigue |
Future Trends in Alloying for Spheroidal Graphite Cast Iron
- Advanced Alloy Design:
- Custom Compositions: Development of custom alloy compositions tailored for specific applications.
- Nanotechnology: Incorporating nanomaterials to refine microstructure and enhance properties.
- Sustainable Alloying Practices:
- Recycling: Increasing the use of recycled materials to reduce environmental impact.
- Green Additives: Utilizing eco-friendly alloying elements and additives.
- Smart Manufacturing:
- IoT and AI Integration: Implementing IoT and AI for real-time monitoring and control of alloying processes.
- Predictive Maintenance: Using advanced analytics to predict and prevent defects in real-time.
- Collaborative Research:
- Industry-Academia Partnerships: Fostering collaborations to drive innovation in alloying techniques.
- Government Support: Leveraging government initiatives and funding for research and development.
List: Future Trends in Alloying for Spheroidal Graphite Cast Iron
- Advanced Alloy Design:
- Custom compositions tailored for specific applications.
- Incorporating nanomaterials for refined microstructure.
- Sustainable Alloying Practices:
- Increasing use of recycled materials.
- Utilizing eco-friendly alloying elements.
- Smart Manufacturing:
- IoT and AI for real-time monitoring and control.
- Predictive maintenance using advanced analytics.
- Collaborative Research:
- Industry-academia partnerships for innovation.
- Government support for research and development.
Conclusion
The addition of alloying elements significantly impacts the microstructure and performance of spheroidal graphite cast iron, enabling the material to meet the demanding requirements of various high-performance applications. By understanding the roles and effects of different alloying elements, manufacturers can tailor the properties of spheroidal graphite cast iron to achieve optimal performance. Future advancements in alloy design, sustainable practices, smart manufacturing, and collaborative research will further enhance the capabilities of spheroidal graphite cast iron, solidifying its role as a critical material in modern engineering.