With the continuous improvement of locomotive speed and carrying capacity, higher requirements are put forward for the steel castings of locomotive bogies, especially the stressed parts. The axle box of subway vehicles belongs to the structural castings of thin-walled boxes, and is also an important force-bearing part of axle box assembly. In the pre-production and processing process, there are shrinkage, sand holes, cracks, the sand core in the box pouring process is crooked, there are black leather and other defects during processing, the production of these defects and the casting process of the axle box body has an important relationship, so it is necessary to analyze and adjust the axle box process.
1 Casting structure and production requirements
The product structure of the axle box is shown in Figure 1, and the casting material is ZG25MnCrNiMo
(C grade steel), the main wall thickness is 20~30 mm, the casting blank weight is 95 kg, the casting line shrinkage takes 2%, the molding and sand core use CO2 hardened water glass sand, one box of two pieces, melting using 10 t electric arc furnace, bottom pouring, pouring temperature control at 1 560~1 580 °C. The design requires the surface of the casting to do magnetic particle flaw detection as a whole, according to the requirements of locomotive assembly accessories, all the processing surfaces and main stress parts of the axle box are not allowed to have shrinkage and crack defects, and the castings are ultrasonic inspection according to batches.
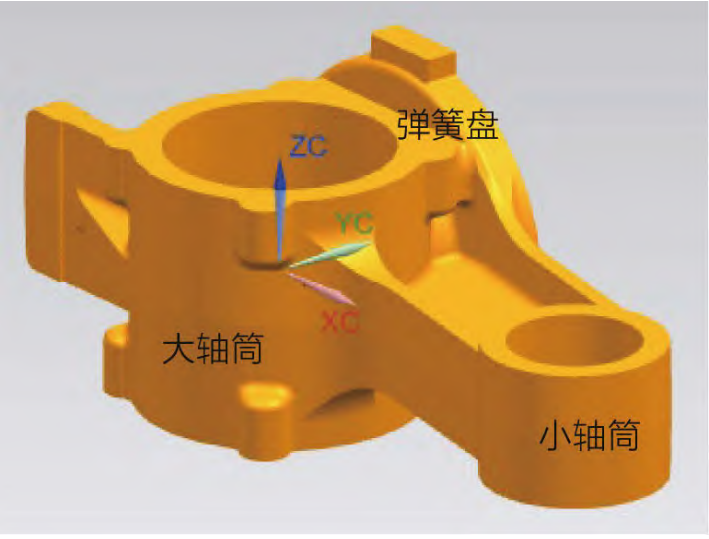
Figure 1 Schematic diagram of the axle box product structure
2 Original process plan and existing problems
2.1 Introduction to the original casting process
Figure 2 is a three-dimensional model of the shaft box casting process scheme, the axle box is divided along the middle of the shaft barrel, and the large shaft barrel is equipped with a waist-shaped type subsidy to ensure the sequential solidification and contraction of the shaft barrel; There are hot joints in the connection between the small shaft barrel and the axle box rib plate, but the modulus and radius are small, and a semicircular dark riser is set near the connection at the top to ensure the internal quality; The lower box of the large shaft barrel and the spring plate surface need to be equipped with a 16 mm thick cold iron plate to enhance the cooling effect, and the inner sprue of the casting is selected at the position of the central rib plate. The original process scheme ensures the quality of the casting processing surface and the main stressed parts in the general direction, but in the mass production process, the defects mainly exist in the large shaft cylinder, inner runner and spring disc, and at the same time, there are problems of molding sand shedding and uneven processing volume.
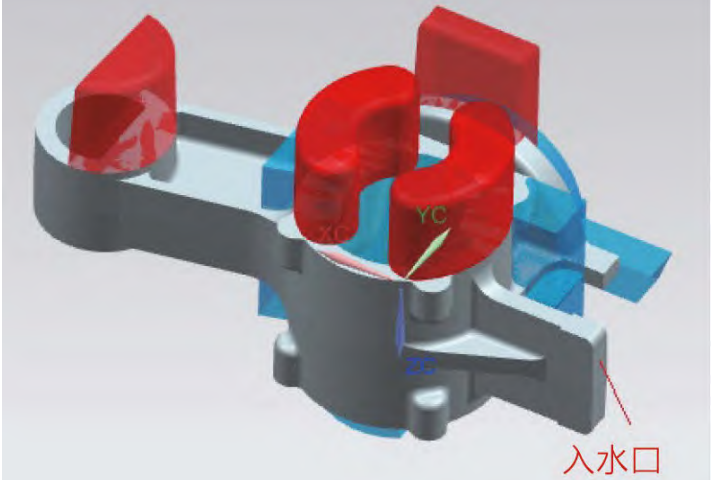
Figure 2 Shaft box casting process scheme
2.2 There is a problem
The main problems in the production process of axle box are the following:
(1) During the shaft box molding process, defects caused by molding sand falling off on the large and small shaft barrel connecting rib plates, as shown in Figure 3, the falling molding sand is wrapped in molten steel and cannot be processed, resulting in small batches of scrap, the same problem
Present at the ear tidal hanging sand core.
(2) A certain proportion of trachoma and shrinkage defects occur in the large shaft cylinder, as shown in Figure 4, which needs to be welded after rough processing, which increases production costs and affects product quality.
(3) The spring disc surface sand core is skewed during the pouring process, resulting in uneven spring disk processing allowance, as shown in Figure 5.
(4) There is a shrinkage crack defect in the gating channel position in the casting, and the shovel needs to be welded.
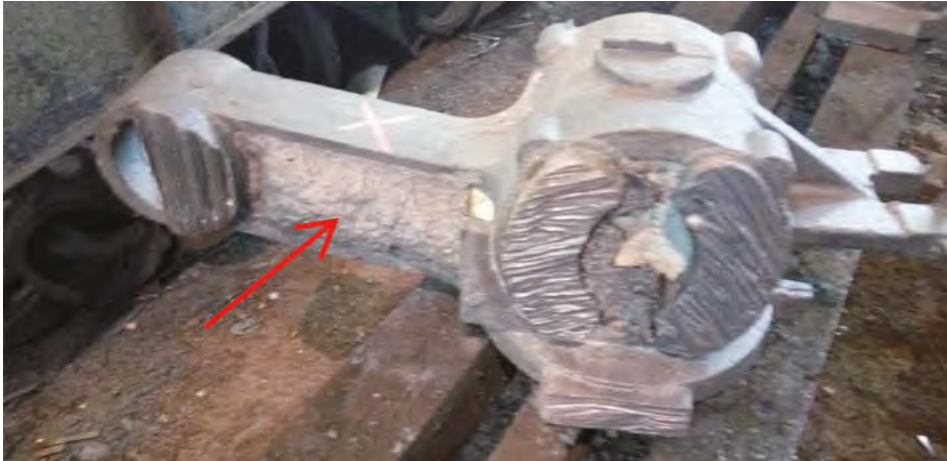
Figure 3 Defects formed by sand shedding
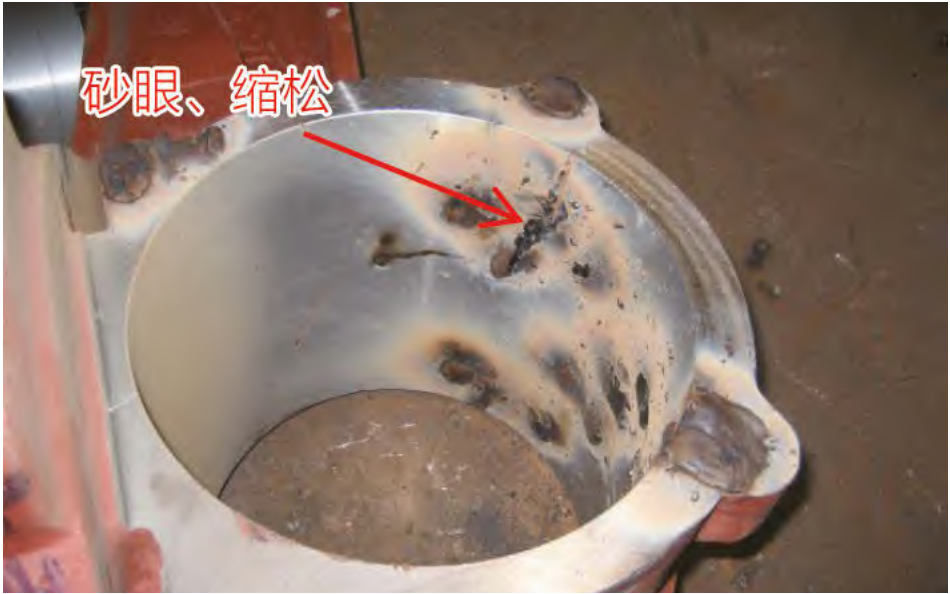
Figure 4 Trachoma and shrinkage defects

Figure 5 Insufficient machining allowance
3 Cause analysis and process improvement
3.1 Sand shedding
The reasons for the formation of molding sand shedding may be: low molding sand strength, poor bonding ability, and uneven mixing; With few or no box stops; The upper box surface or sand lifting part is not hooked, and the reinforcement strength of the iron nail is not enough; The firmness is not enough, the compactness is uneven or partially leaked; The depth of the cavity is too deep, and the unstable closing leads to bumping; After closing the box, the pin eye is aligned or the clamp is beaten and vibrated during tightening. The axlebox is made of CO2 hardened water glass sand, and the molding sand falls off in two places The situation is: the sand core of the shaft ear is molded rubber tide crane, there will be bumps in the process of turnover lifting, the sticky core paste does not reach the required strength will cause the molding sand to fall off, under the premise of solving the problem and meeting the production of the use of the core core center reserved hole, tide hanging sand core from the reserved hole embedded nails added Solid; The height of the cavity of the large and small shaft connecting ribs is 50 mm, the depth is relatively deep, the strength of the sand mold at this position is insufficient after the vibration table is used during molding, and the molding sand is falling off due to the scouring of the molten steel during the pouring process, and the core bone is folded into the core bone with a welding rod during molding, and the sand core strength of this part is strengthened through the core bone.
3.2 Large shaft barrel inner shrinkage loosening and trachoma
The main defects in the large shaft barrel are shrinkage and trachoma. The reason for the occurrence of trachoma in processing is that the operation is not careful, and the cleaning cavity is not clean resulting in sand hole defects in the shaft barrel, because the inner wall of the cylinder is the processing surface, and most of the trachoma can be removed after processing, for this reason, the trachoma defect is effectively solved by increasing the processing amount of this part. Shrinkage is 25 mm before processing of the wall thickness of the large cylinder, the distance between the end area of the filling is about 65 mm, the riser area is about 50 mm, the vertical filling distance is 115 mm, the shaft height is 245 mm, to achieve the sequential solidification full contraction, the subsidy depth value is 130 mm, the distance between the two insulation risers of the casting is 120 mm, and the filling distance between the two risers is 100 mm. In summary, the shrinkage defect of the large shaft cylinder is caused by the insufficient shrinkage distance between the risers, and the pouring temperature of the molten steel is not easy to control, resulting in the shrinkage defect. The tentative improvement scheme is to convert the original 2 waist circles
The insulation riser is replaced with 3 round insulation risers, and the distance between the risers is reduced to 90 mm, which can theoretically achieve a good shrinkage effect without affecting the yield of the casting process.
3.3 The spring disc machining allowance is insufficient
The reason for the insufficient processing volume of the spring disc is that the sand core at the position of the spring disc in the original production is a disc sand core with a lower core head, and there is an error between the position of the core head of the core box and the mold starting slope of the core seat, and the deformation of the wood mold during production and use leads to the gap between the core head and the core base after the core is too large, and the sand core is tilted forward when the box is closed, and the blank is poured after pouring The machining allowance of the spring disc surface is uneven, and the machining allowance of the upper part is insufficient and needs to be welded. The positioning effect of the lower core head is not good, the lower core head scheme is adjusted to the left and right core heads, the core head size is reduced, the adjusted core head and the core seat are better coordinated, and the positioning effect is better than the former.
3.4 Inner sprue shrinkage and cracks
The size of the sprue in the shaft box is 40/35 mm×H, where H is the height of the inner runner section, the height dimension transitions from the cross runner to the casting rib plate position is 15 mm, the thickness of the rib plate at the inner runner is 7.5 mm, there is a thickness difference, the casting rib plate will solidify before the inner runner, causing tensile stress on the contact position, and cracks will appear when the casting solidifies. Due to structural limitations in this part, to solve the shrinkage loosening, the thickness of the inner runner and the casting rib plate tends to be uniform, the inner runner needs to do an open pouring system, and the inner sprue is made flat, but the molten steel has the characteristics of high melting point and poor fluidity, and the pouring temperature control of the molten steel in the pouring process after changing to a flat structure may be insufficient pouring. The process considers adjusting the position of the inner runner, adjusting the inner runner to the left notch, the notch position is the processing surface, the thickness is 25 mm, the choice of the inner runner is more reasonable here, even if cracks or other defects can be eliminated.
4 New process on-site production control
Based on the above improvement measures, the new casting process is designed, the process diagram is shown in Figure 6, and the new casting process is simulated and the results are consistent with the analysis. Make molds for trial production, and strengthen the control of the molding link during production. bear During production, according to the provisions of the process card, cold iron, gate rod, thermal insulation riser sleeve, etc., the cold iron shall not be skewed or sanded, the amount of sand eating between the core bone and the mold wall should be controlled at 15~50 mm (or more than this amount of sand), the molding should be stable, the compactness of each part of the sand mold and sand core should be uniform, its compactness must comply with the provisions of the process card, the compactness of the no process card should be controlled above 45 units, and the core brush coating should be at a suitable depth, no accumulation, no flow marks, and the thickness should be uniform and flat. Before lifting the core, the sand cavity must be cleaned. The virtual sand air around the cold iron should be scraped and blown clean around the eye hole, and the air outlet hole should be smooth Through, the oxygen hole in the cavity should be plugged with molding sand and smoothed. The surface of the sand core must be cleaned, the flashes and burrs should be smoothed, and the sharp edges should be rounded.
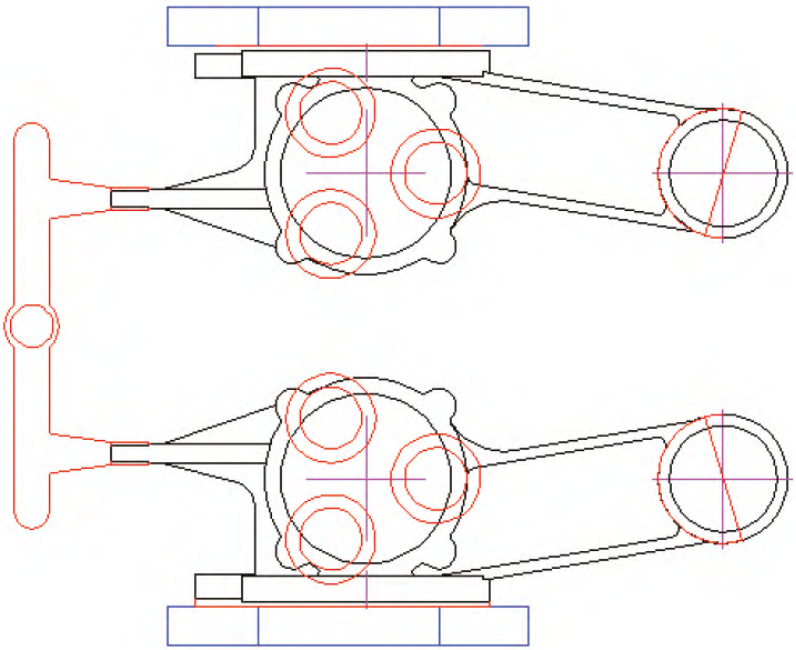
Figure 6 Process diagram
The improved process scheme was used to produce 10 samples, and the castings were cleaned and polished for visual inspection, and the improved castings had no sand loss defects; Dimensional scribing inspection is carried out, the main inspection size of the casting is good, and the spring disc position is located machining allowance 7 mm and uniform thickness; After cleaning, the shaft barrel was ultrasonic inspected, and no shrinkage defects were found inside all castings, and the external inclusions and trachoma were significantly reduced; Magnetic particle flaw detection is carried out on the inner runner position, and there are no surface defects such as cracks, and the flaw detection is qualified. The first batch of castings were inspected and flawed one by one, and all of them were qualified, which verified the rationality of the cause analysis and the feasibility of improvement measures.