The company produces a rod-shaped casting (shown in Figure 1) with contour dimensions of φ40 mm ×326 mm, made of chrome cast iron Cr20, which is a typical anti-wear white cast iron, characterized by high hardness and a strong metal matrix supporting high-strength carbides. Due to low thermal conductivity, poor plasticity, large shrinkage, large tendency to hot cracking and cold cracking, the casting performance of anti-wear white cast iron is poor. The original process uses precision casting process to produce the anti-wear cast iron casting, but the scrap rate of the original process product is high, which is about 20% by statistics, and the precision casting process has more production processes and a long production cycle, resulting in the production of the casting paraffin, molding sand and other raw materials consumed, the process yield rate is not ideal, the production cost is high, and the production efficiency is low. Therefore, the design decided to adopt the coated sand shell casting process.
1 Casting process design
1.1 Casting process
The rod casting material is chromium cast iron Cr20, so the casting line shrinkage rate is designed to be 2%, according to the structure and size of the product according to the modulus method to calculate the rod casting to be supplemented by the modulus part modulus is M pieces = 1/4× 4.5 cm = 1.125 cm, from which the riser module can be calculated as M = (1.1~1.2) ×M pieces = 1.15× 1.125 cm=1.24 cm, according to the structure and combined with the actual can be used spherical riser (the smallest volume of spherical riser in the case of the same specific surface area) into the process design, for this reason, according to the principle of spherical riser to the casting hot joint compensation to carry out the process design, so as to calculate the spherical shape The riser D=7.44 cm, from which the spherical riser size is determined to be SR =1/2×6×M min=3.75 cm, and the spherical riser is designed at the tail of the rod casting, as shown in Figure 2, which facilitates bottom-up sequential solidification during the molten iron solidification process.
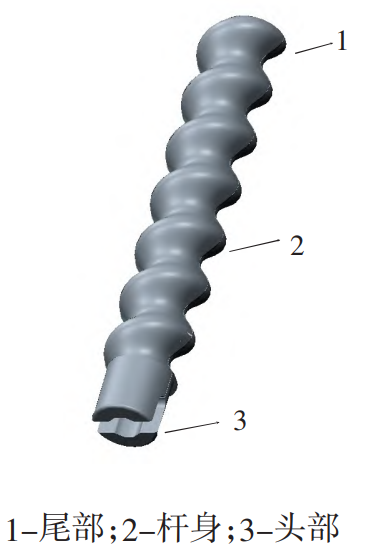
Fig. 1 Three-dimensional structural diagram of rod-shaped anti-wear cast iron castings
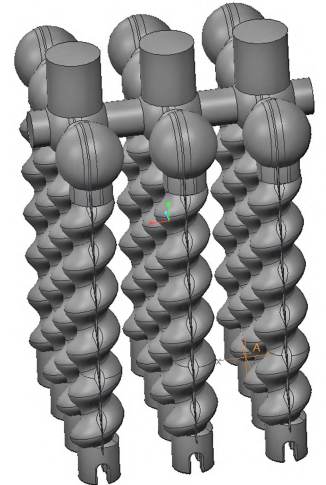
Figure 2 Three-dimensional structure diagram of the rod casting casting process
1.2 Casting method
The sand mold (core) is produced by the coated sand shell molding process, and the sand (mold) is made by using a metal mold on a 40 kg heat shot core machine, each type is made of two pieces on the left and right, the sand mold design is 4 pieces/type, and the sand core is designed as 4 pieces sharing 1 sand core (as shown in Figure 3), and its function is to form the inner cavity structure of the head of the rod-shaped casting. The sand mold (core) assembly method is carried out by special tandem tooling core molding, each casting is equipped with a spherical riser, each rod casting is connected by φ40 mm cross runner with each other, and the sand mold is connected by φ40 mm tandem sprue, the current process design 6The sand molds (cores) are split into 1 casting group, 48 rod castings are poured in 1 casting group, and 1 gate cup is set up for the guidance of molten iron, as shown in Figure 4.
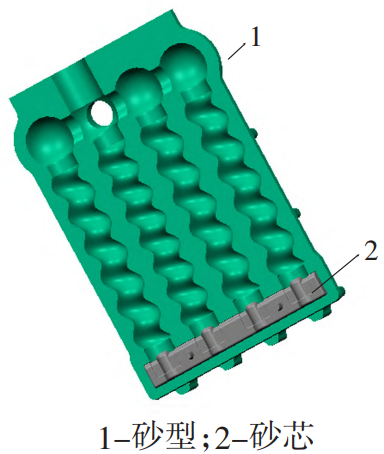
Figure 3 Three-dimensional structure diagram of sand mold (core) of rod casting
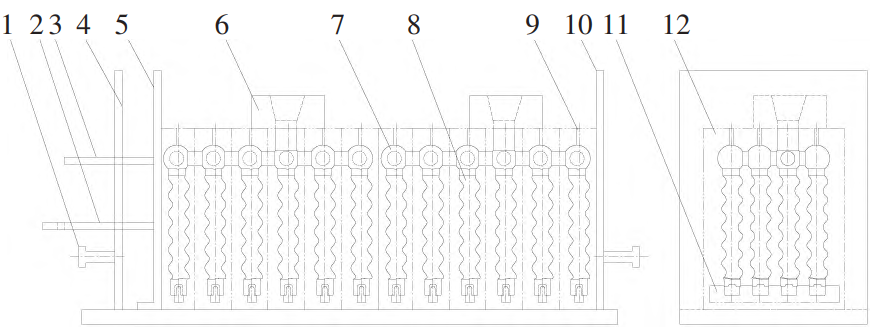
Figure 4 Schematic diagram of the sand (core) core
1.3 Smelting process
The use of medium frequency induction electric furnace to melt molten iron, molten iron chemical composition press According to w(C) 2.8~3.0%, w(Si)≤0.6%, w(Mn)0.5~0.8%, w(P)≤0.02%, w(S)≤0.04%, w(Cr)20.0~21.0%.The temperature of molten iron is controlled according to 1 500 °C±10 °C, and the pouring speed is controlled Degree (25 s~30 s) / pouring group, pour the molten iron that is qualified for melting into the special Molten iron pouring package, using the lifting bag method (the original process adopts lifting bag pouring,1 pack of iron moisture 3 times pouring 3 mold shells) for molten iron pouring, pouring The process is carried out according to the “slow-fast-slow” rhythm, and after pouring, the point gate should be flushed 1~2 times in time, and the shot blasting cleaning operation can be carried out after the molten iron solidifies for more than 8 h.
1.4 Process simulation
In order to further verify the reliability of the process, the ProCAST virtual simulation software was used to simulate the rod casting process, and no shrinkage holes were found in the casting after simulation calculation phenomenon (as shown in Figure 5), which shows that the process has a certain operability, which provides favorable support for subsequent actual production.

Figure 5 Process simulation diagram
2 Process test and verification
Design and make the hot core box metal type through the rod casting process, and make the coated sand sand mold (core) according to the process requirements after the hot core box is made, melt molten iron with medium frequency induction electric furnace, the actual furnace temperature is 1 509 °C, and the 500 kg pouring package is used to complete 1 furnace casting (4 pouring) in 4 pouring
The injection group is 1 furnace), the measured pouring speed is 30 s, 28 s, 29 s, 28 s. The casting completed pouring was cut and cleaned in the later stage, and no casting defects such as loose shrinkage holes were found at the root of the spherical riser and the tail of the rod-shaped casting (as shown in Figure 6), in order to further verify the reliability of the process The piece was dissected by wire cutting, and the internal structure of the casting was dense, and no casting defects such as loosening were found (as shown in Figure 7). Subsequently, the casting process yield of the product was 70.5% compared with the physical weighing of the casting and riser, which was 5% higher than that of the original precision casting process product. After machining by the processing unit, it was found that the machining allowance of the rod-shaped casting blank was reasonable, and no processing was found”Black leather” and other defects, which indicates that the size of the rod-shaped casting is qualified, but it is found that there are different degrees of porous defects on the surface of some castings after processing (as shown in Figure 8), and the proportion of the porous defects is about 90% after statistics, due to the special characteristics of chromium cast iron The product has not been repaired and other measures, resulting in batch scrapping of the product.

Figure 8 Stomatic defects
In view of the problem of stomatal defects after processing, the stomatal defects should be subcutaneous stomata after further analysis, and the analysis reason is that the binder for coated sand contains hexamethylene tetramine, which is generated when decomposed by heat NH3, CN, the chemical binding energy of these two gases is low, easy to decompose into an atomic state, and after being involved in molten metal, it is easy to form pores when the casting solidifies. In addition, the gas generation of the coated sand itself is large, resulting in the failure to effectively eliminate the intra-type gas in the pouring process, resulting in a certain degree of subcutaneous porous defects in the casting. In order to effectively solve the problem of subcutaneous pores in rod-shaped castings, follow-up measures were taken to improve targeted tests, specifically for the combination of sand Before the mold (core), the sand mold (core) is impregnated and impregnated with an integral alcohol-based coating After ignition and drying in time to pre-emptively exclude and fully decompose NH3 and CN Excluding the residual moisture in the coated sand mold, the inner surface dipping coating is conducive to preventing the occurrence of porosity defects, and the rod-shaped casting produced after the improvement has been effectively solved by machining.
3 Conclusion
1) The use of spherical riser effectively solves the problem of rod-shaped casting shrinkage, which is conducive to the improvement of the yield rate of the casting process and the reduction of raw material consumption.
2) The inner cavity or surface of the coated sand mold is impregnated with alcohol-based graphite coating, which can improve the surface finish of the casting while preventing the occurrence of subcutaneous porous defects of the casting.