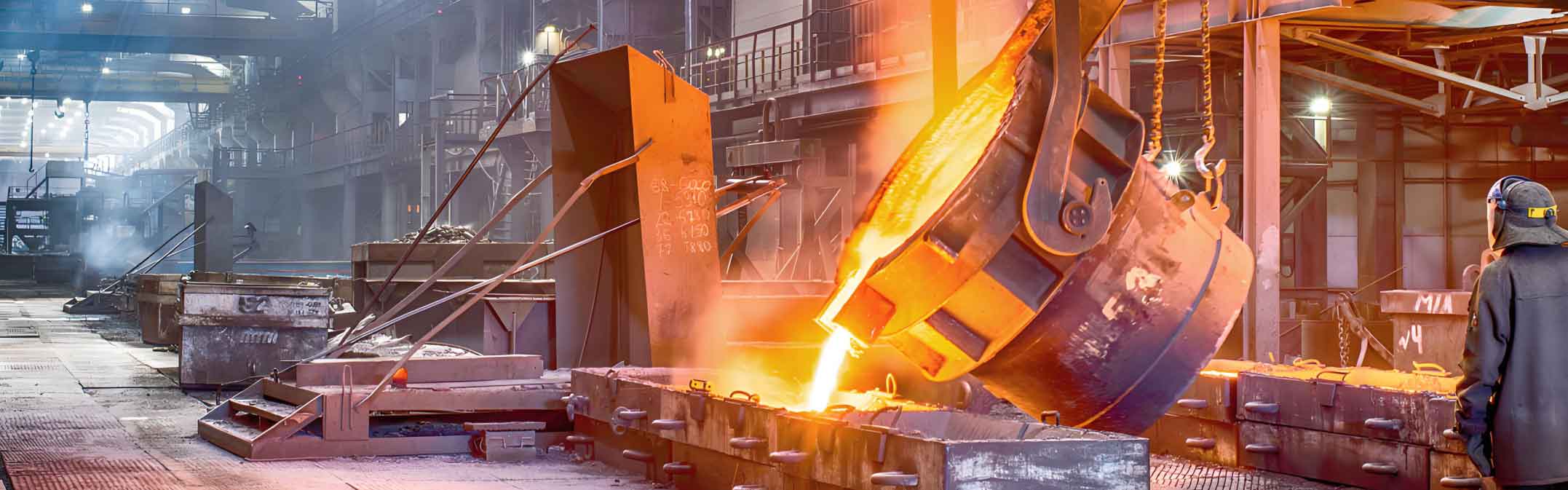
Lost foam casting is a precise and efficient casting process that offers numerous advantages for producing complex metal components. However, achieving high-performance castings requires careful optimization of various casting parameters. This article explores the key parameters involved in lost foam casting and provides insights into optimizing these parameters to achieve superior casting quality, mechanical properties, and overall performance.
Introduction to Lost Foam Casting
Lost foam casting involves creating a foam pattern that replicates the final metal part, coating it with a refractory material, and embedding it in a sand mold. When molten metal is poured into the mold, the foam pattern vaporizes, leaving behind a detailed metal casting. The process is particularly well-suited for producing intricate geometries with high precision and minimal need for post-casting machining.
Key Steps in Lost Foam Casting
- Foam Pattern Creation: A foam model of the desired component is created using suitable foam materials.
- Pattern Assembly: The foam pattern is assembled with gating systems if needed.
- Coating: The foam pattern is coated with a refractory material to form a thin shell.
- Mold Preparation: The coated foam pattern is placed in a sand mold, and sand is packed around it.
- Metal Pouring: Molten metal is poured into the mold, causing the foam pattern to vaporize and be replaced by the metal.
- Mold Breakout: Once the metal has solidified, the sand mold is broken away to reveal the metal casting.
- Finishing: The casting is cleaned, and any excess material is removed to achieve the final product.
Key Parameters in Lost Foam Casting
To achieve high-performance lost foam castings, several key parameters must be carefully controlled and optimized. These parameters include foam pattern materials, coating materials, sand properties, pouring temperature, and cooling rate.
Foam Pattern Materials
The choice of foam pattern materials significantly impacts the accuracy, surface finish, and overall quality of the final casting.
- Density: Affects the pattern’s strength and the ease of handling. Higher density foams provide better dimensional stability but may be harder to vaporize.
- Thermal Conductivity: Influences the rate at which the foam vaporizes when in contact with molten metal. Lower thermal conductivity is preferred to ensure complete vaporization.
- Dimensional Stability: Ensures the pattern retains its shape during handling and coating, leading to accurate castings.
Coating Materials
Coating the foam pattern with refractory materials is essential for protecting the pattern during the casting process and ensuring a high-quality surface finish.
- Permeability: Allows gases to escape during metal pouring, reducing the risk of defects.
- Strength: Provides mechanical support to the foam pattern and prevents deformation.
- Thermal Stability: Ensures the coating can withstand the high temperatures of molten metal without breaking down.
Sand Properties
The sand used to create the mold plays a crucial role in the lost foam casting process.
- Grain Size: Finer sand grains provide a smoother surface finish but may reduce permeability.
- Binder Content: The amount and type of binder used can affect the strength and stability of the sand mold.
- Moisture Content: Excessive moisture can lead to gas porosity and defects in the casting.
Pouring Temperature
The temperature at which molten metal is poured into the mold affects the fluidity of the metal and the vaporization of the foam pattern.
- Optimal Temperature: Ensures that the metal remains fluid enough to fill the mold completely without solidifying prematurely.
- Consistency: Maintaining a consistent pouring temperature prevents temperature fluctuations that can lead to defects.
Cooling Rate
The rate at which the casting cools and solidifies impacts the microstructure and mechanical properties of the final product.
- Controlled Cooling: Ensures uniform solidification and reduces internal stresses.
- Directional Solidification: Promotes the formation of desirable microstructures by controlling the direction of solidification.
Parameter | Considerations |
---|---|
Foam Pattern Materials | Density, thermal conductivity, dimensional stability |
Coating Materials | Permeability, strength, thermal stability |
Sand Properties | Grain size, binder content, moisture content |
Pouring Temperature | Optimal temperature, consistency |
Cooling Rate | Controlled cooling, directional solidification |
Optimizing Foam Pattern Materials
The foam pattern is a critical component in lost foam casting, as it directly influences the accuracy, surface finish, and overall quality of the final casting.
Selecting the Right Foam Material
Choosing the appropriate foam material is essential for achieving high-performance castings. The material should have the right balance of density, thermal conductivity, and dimensional stability.
- Expanded Polystyrene (EPS): Commonly used due to its excellent dimensional stability and ease of handling. Provides good surface finish but requires careful control to ensure complete vaporization.
- Expanded Polypropylene (EPP): Offers higher strength and better thermal resistance compared to EPS, making it suitable for more demanding applications.
- Polyurethane Foam: Known for its excellent surface finish and high dimensional accuracy, ideal for precision castings.
Enhancing Foam Pattern Properties
Improving the properties of foam patterns can further enhance casting quality.
- Additives: Incorporating additives such as flame retardants can improve the thermal stability and vaporization characteristics of the foam.
- Surface Treatment: Applying surface treatments to the foam pattern can improve its dimensional stability and reduce defects.
Foam Material | Advantages | Applications |
---|---|---|
Expanded Polystyrene (EPS) | Good dimensional stability, ease of handling, cost-effective | Automotive components, engine blocks, machinery parts |
Expanded Polypropylene (EPP) | High strength, superior thermal resistance | Aerospace components, high-stress automotive parts |
Polyurethane Foam | Excellent surface finish, high dimensional accuracy | Medical devices, precision instruments |
Optimizing Coating Materials
Coating materials play a vital role in protecting the foam pattern and ensuring a high-quality casting.
Selecting the Right Coating Material
Choosing the appropriate coating material is essential for achieving high-performance castings. The material should have the right balance of permeability, strength, and thermal stability.
- Refractory Coatings: Commonly used coatings that provide good thermal stability and mechanical support.
- Permeable Coatings: Allow gases to escape during metal pouring, reducing the risk of defects.
Enhancing Coating Properties
Improving the properties of coatings can further enhance casting quality.
- Additives: Incorporating additives such as anti-cracking agents can improve the strength and stability of the coating.
- Multiple Layers: Applying multiple layers of coating can enhance the mechanical support and thermal stability of the foam pattern.
Coating Material | Advantages | Applications |
---|---|---|
Refractory Coatings | Good thermal stability, mechanical support | General-purpose castings |
Permeable Coatings | Allows gas escape, reduces defects | Complex geometries, high-precision castings |
Optimizing Sand Properties
The sand used to create the mold plays a crucial role in the lost foam casting process.
Selecting the Right Sand
Choosing the appropriate sand is essential for achieving high-performance castings. The sand should have the right balance of grain size, binder content, and moisture content.
- Silica Sand: Commonly used due to its good thermal stability and availability.
- Zircon Sand: Offers superior thermal stability and provides a smoother surface finish.
- Olivine Sand: Known for its good thermal properties and reduced environmental impact.
Enhancing Sand Properties
Improving the properties of sand can further enhance casting quality.
- Additives: Incorporating additives such as binders and moisture controllers can improve the strength and stability of the sand mold.
- Pre-conditioning: Pre-conditioning the sand to the right moisture content can reduce the risk of gas porosity and defects.
Sand Type | Advantages | Applications |
---|---|---|
Silica Sand | Good thermal stability, widely available | General-purpose castings |
Zircon Sand | Superior thermal stability, smoother surface finish | High-precision castings |
Olivine Sand | Good thermal properties, reduced environmental impact | Eco-friendly casting processes |
Optimizing Pouring Temperature
The temperature at which molten metal is poured into the mold affects the fluidity of the metal and the vaporization of the foam pattern.
Determining the Optimal Pouring Temperature
Selecting the optimal pouring temperature is essential for achieving high-performance castings. The temperature should ensure that the metal remains fluid enough to fill the mold completely without solidifying prematurely.
- Metal Type: Different metals have different optimal pouring temperatures. For example, aluminum alloys typically require lower temperatures than cast iron.
- Mold Material: The thermal properties of the mold material can influence the optimal pouring temperature.
Maintaining Consistency
Maintaining a consistent pouring temperature is crucial for preventing temperature fluctuations that can lead to defects.
- Temperature Control Systems: Using advanced temperature control systems can ensure that the molten metal remains at the optimal temperature throughout the pouring process.
Metal Type | Optimal Pouring Temperature |
---|---|
Aluminum Alloys | 660-750°C |
Cast Iron | 1200-1450°C |
Steel | 1500-1600°C |
Optimizing Cooling Rate
The rate at which the casting cools and solidifies impacts the microstructure and mechanical properties of the final product.
Controlling Cooling Rate
Controlling the cooling rate is essential for achieving high-performance castings. The cooling rate should ensure uniform solidification and reduce internal stresses.
- Cooling Channels: Incorporating cooling channels into the mold can help control the cooling rate and promote uniform solidification.
- Chills: Using chills can accelerate the cooling rate in specific areas, promoting directional solidification.
Promoting Directional Solidification
Promoting directional solidification can enhance the mechanical properties of the final casting.
- Thermal Gradients: Creating thermal gradients within the mold can promote directional solidification, leading to a more desirable microstructure.
Cooling Technique | Advantages | Applications |
---|---|---|
Cooling Channels | Ensures uniform solidification, reduces internal stresses | General-purpose castings |
Chills | Accelerates cooling rate, promotes directional solidification | High-stress components, structural parts |
Conclusion
Optimizing casting parameters is crucial for achieving high-performance lost foam castings. By carefully selecting and controlling foam pattern materials, coating materials, sand properties, pouring temperature, and cooling rate, manufacturers can produce castings with superior quality, mechanical properties, and overall performance. These advancements ensure that lost foam casting remains a viable and highly effective method for producing precision metal components across various industries, including automotive, aerospace, medical devices, and industrial machinery.
Parameter | Considerations |
---|---|
Foam Pattern Materials | Density, thermal conductivity, dimensional stability |
Coating Materials | Permeability, strength, thermal stability |
Sand Properties | Grain size, binder content, moisture content |
Pouring Temperature | Optimal temperature, consistency |
Cooling Rate | Controlled cooling, directional solidification |
By focusing on these critical parameters and employing advanced techniques, manufacturers can achieve superior results, ensuring high-quality, reliable, and cost-effective castings for a wide range of applications.