At present, there are generally two kinds of structures at the cylinder head injector of diesel engine. One is press fitting the injector bushing after machining (hereinafter referred to as the bushing structure); The other structure is that the injector bushing is not pressed, and the bushing shape is directly machined (hereinafter referred to as the bushing free structure). The two different structures have great influence on the casting process, and each has its own advantages and disadvantages. The specific analysis is as follows.
1.Cylinder head has bushing structure
The cylinder head injector with bushing structure is common in the diesel engine cylinder head developed by our company, as shown in Figure 1.
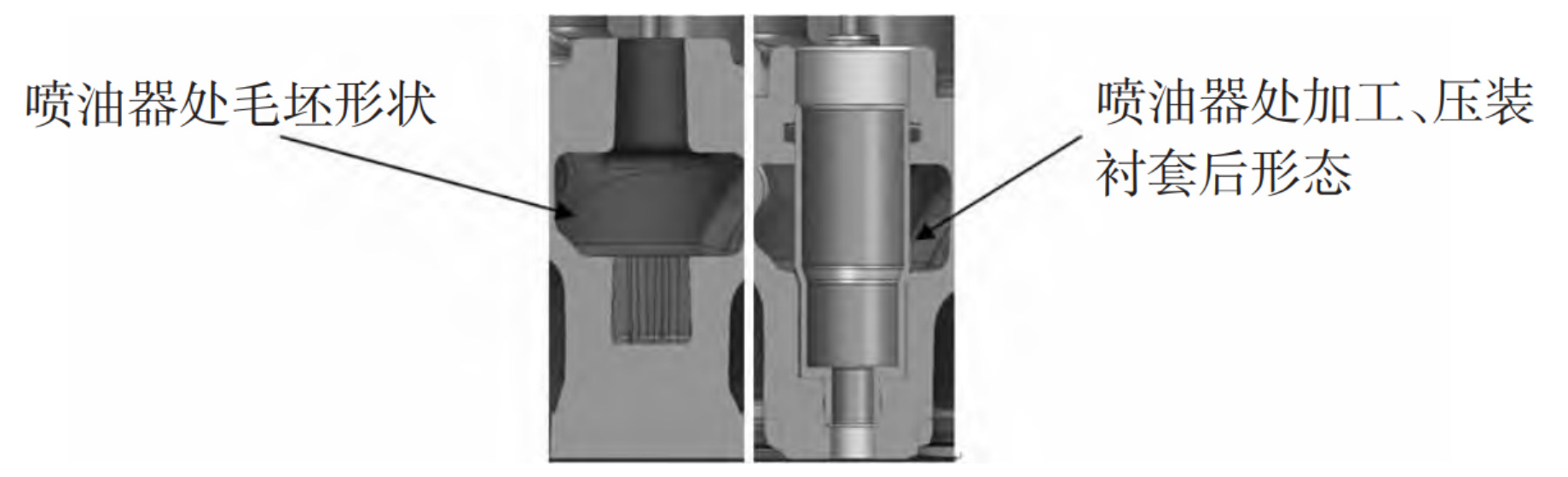
The advantage of the bushing structure is that the blank hole can be cast at the injector position of the casting, which can remove sand and facilitate the cleaning of the casting gap; At the same time, the sand core forming the hole can also play the role of sand core exhaust, positioning and compaction in the casting process, reduce the occurrence of casting defects, and facilitate the cleaning of the blank cavity.
The disadvantage of the bushing structure is that the fuel injector bushing needs to be pressed after processing. Generally, it is a copper bushing with high cost. In addition, if the bushing is not well sealed during the pressing process, there will be leakage.
2.Cylinder head without bushing structure
The Bushless structure of cylinder head injector is mainly used in the cylinder head, a new product developed by our company in recent years, as shown in Figure 2.
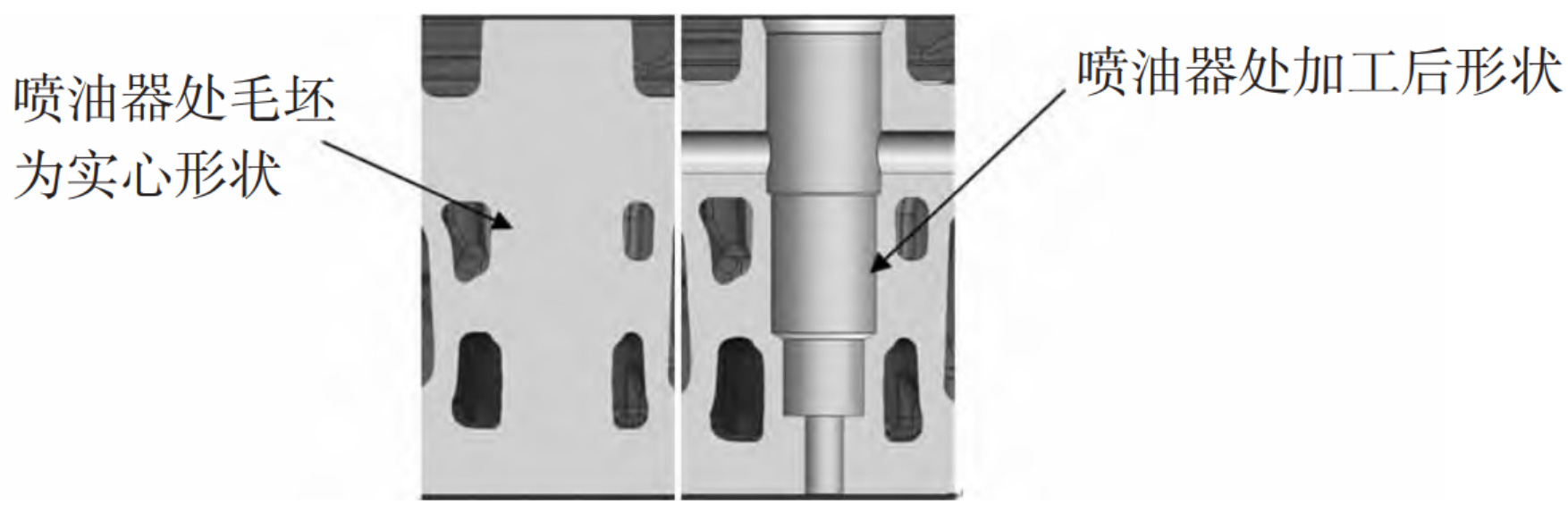
The advantage of the Bush free structure is that the solid structure at the blank injector can be directly machined into the final shape of the injector hole, and there is no need to press fit the Bush after machining. The structure can not only reduce the cost, but also reduce the problem of leakage due to poor sealing of the bushing in the press fitting process.
The disadvantage of the bushing free structure is that the sand core structure around the injector is relatively weak, and casting defects such as sand sticking and sintering are easy to occur. However, the casting injector has no casting blank hole, which will lead to the problem that there are sand sticking defects near the injector and can not be cleaned, as shown in Figure 3.
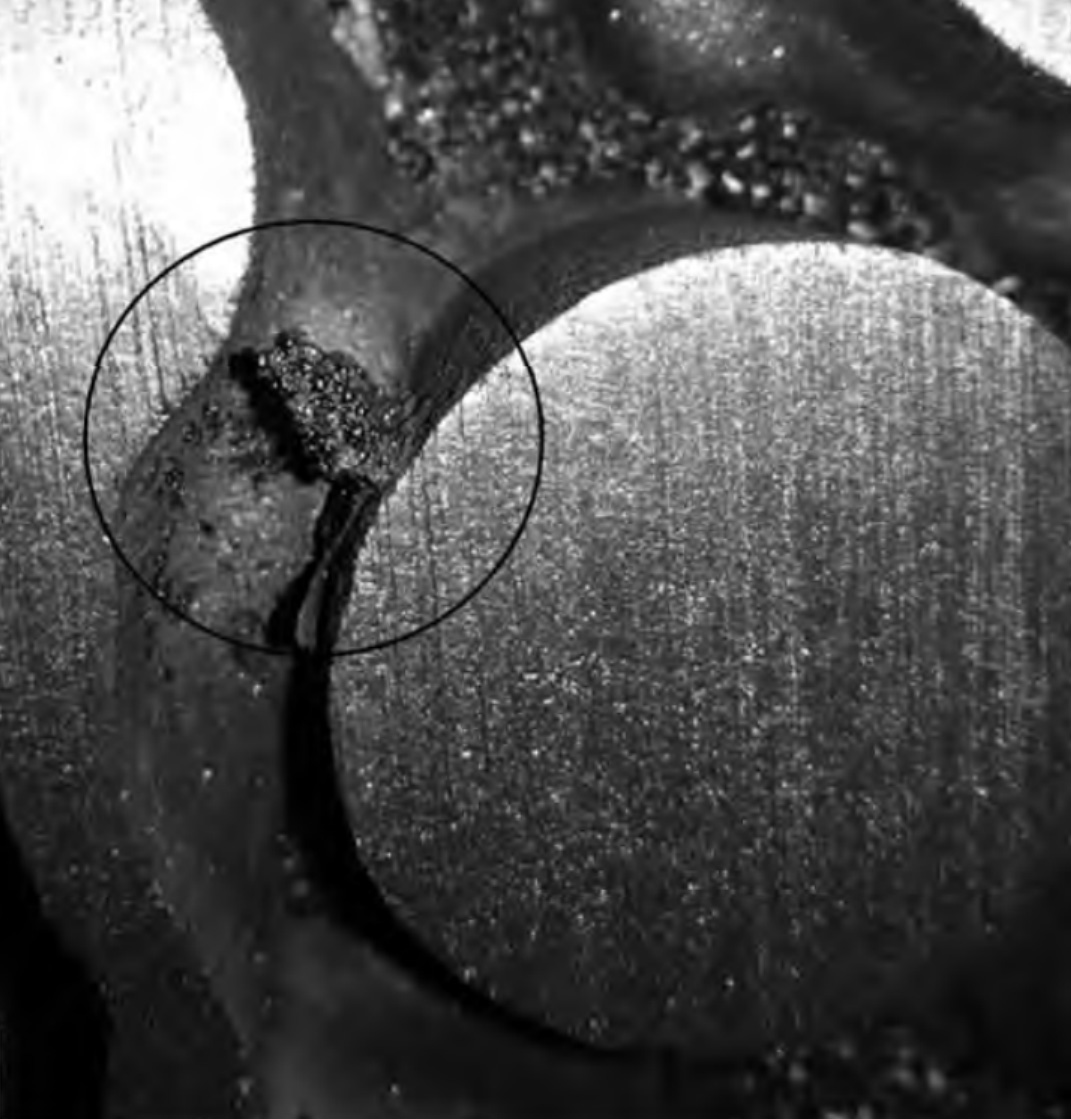
The injector core with bushing structure is a very important exhaust process hole in the casting process, while the non bushing structure will lead to the limited layout of the exhaust system and the risk of pore defects; In addition, the fuel injector is solid, which is the hot spot of the casting. If the material strength requirements are high, it is also prone to shrinkage and other defects.
3.Analysis and suggestions
Combined with the advantages and disadvantages of the two structures, as well as the actual production and application, it is suggested that the liner structure should be considered at the initial stage of cylinder head design, which can avoid the batch quality problems caused by the problems of sand sticking in the inner cavity.