The main failure mode of connecting rod is fatigue fracture. In order to keep the crankshaft in balance at high speed, the connecting rod quality tolerance is also required to be limited within a certain range. At the same time, the connecting rod body cannot be machined after die forging, otherwise it will cut off the fiber formed by metal flow during die forging, resulting in fiber outcrop and affecting the fatigue performance, which puts forward high requirements for the die forging process of connecting rod, especially the connecting rod body. Therefore, the material and die forging process of connecting rod is one of the keys of its manufacturing technology.
In order to ensure the mechanical properties and machining accuracy of the connecting rod, it is necessary to put forward strict requirements for the blank. This includes the macro structure of the metal. The fiber direction should be along the center line of the connecting rod and consistent with the shape of the connecting rod. Vortex and interruption are not allowed. The porosity, bubble, delamination, crack and inclusion after forging are strictly controlled. The microstructure shall have a uniform sorbite fine grain structure. The ferrite is only allowed to exist in the form of small inclusions. There are certain finishing requirements for the non machined surface. If necessary, special surface strengthening treatment shall be carried out. The cracks and other defects inside the blank shall be inspected by magnetic flaw detection, and the tolerance of blank weight shall be inspected according to the requirements of specific products.
See Table 1 for quality inspection of common carbon steel and alloy structural steel connecting rods.
Inspection items | Inspection method | Inspection requirements |
Surface quality | Observation | No cracks, hairlines, folds, overburning, oxidation pits, slippage, and the metal is not full |
Fiber orientation | Show macro organization | The direction of the metal fiber shall be along the center line of the connecting rod and consistent with the shape, without disorder and discontinuity, as per the requirements of the product drawing |
Hardness | Check according to the position shown in the figure | Check according to the position shown in the figure |
Microstructure | Rating after sampling and sampling inspection according to the parts shown in the figure | Uniform and fine sorbite can be rated according to the standard. Grade 1-4 is qualified, Grade 5-6 must be shot peened before loading, and grade 7-8 must be re tempered |
Flaw detection | Magnetic flaw detection | Those with cracks shall be scrapped |
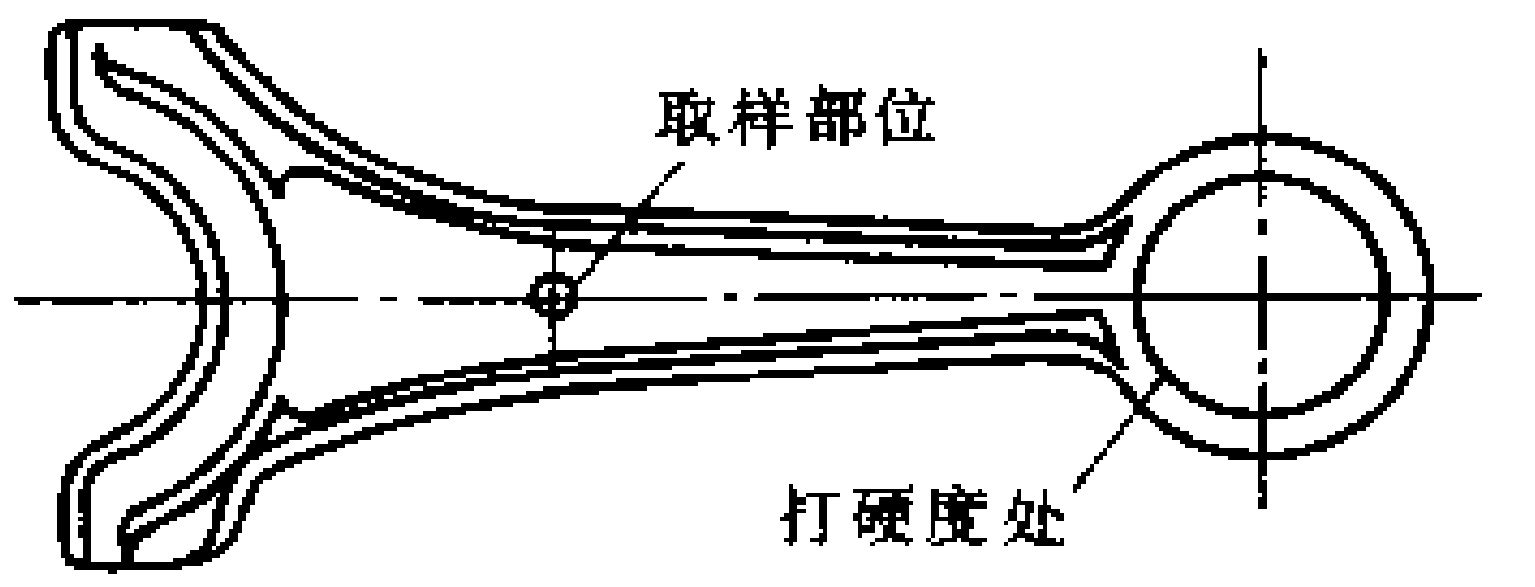
See Table 2 for common defects and preventive and remedial measures of connecting rod heat treatment.
Defect name | Cause of formation | Preventive and remedial measures |
Bulk inclusion | Poor smelting | Strengthen incoming inspection of raw materials |
Fold | Poor forging | Strengthening surface quality inspection of forgings |
Decarburization | 1) Forging heating time under high temperature is too long 2) improper heat treatment operation | Control heating time or pass protective atmosphere to prevent decarburization of connecting rod during forging and heat treatment |
Low hardness | Low heating temperature or slow quenching cooling speed | Re quenching |
Quenching crack | Quenching and cooling is too fast, and the material composition is incorrect | Pay attention to material composition and select cooling conditions |
Uneven tissue | Improper quenching operation and slow cooling speed | Strictly implement the quenching process and strengthen sampling inspection so as to find out in time |
In the production of connecting rod, 100% hardness and crack inspection is required, and the residual magnetic field detection device can also be used for automatic hardness sorting.
Most of the pickling treatment of connecting rod has been replaced by shot peening, which makes it difficult for magnetic particle inspection after shot peening, so only fluorescent inspection can be used, so that the fluorescent magnetic particles gathered at the defective parts of connecting rod can excite yellow and green light under the UV light. Foreign countries have used photoelectric conversion elements to replace visual automatic sorting devices, and the detection sensitivity of this automatic detection device is 4 × 0.5 (mm), and the detection speed is 50 pieces /h.