The changing trend of the influence of pouring temperature on the average mold filling speed of molten metal in lost foam casting shows that the thermal decomposition characteristics of pattern materials significantly affect the mold filling speed of molten metal. Generally speaking, the gas generation rate depends on the width of the air gap layer. The wider the air gap layer, the lower the gas generation rate. However, within the casting temperature range of cast iron, the size of the air gap layer does not significantly affect the gas generation rate, because the heat transfer of the decomposed pattern is mainly through thermal radiation. The diffusion of gas depends on the diffusion surface area, which in turn depends on the width of the air gap layer. Therefore, there is a dynamic balance between gas generation, gas escape, liquid metal filling velocity and the size of the air gap layer. The actual filling velocity is determined by the dynamic balance between the static head and the back pressure.
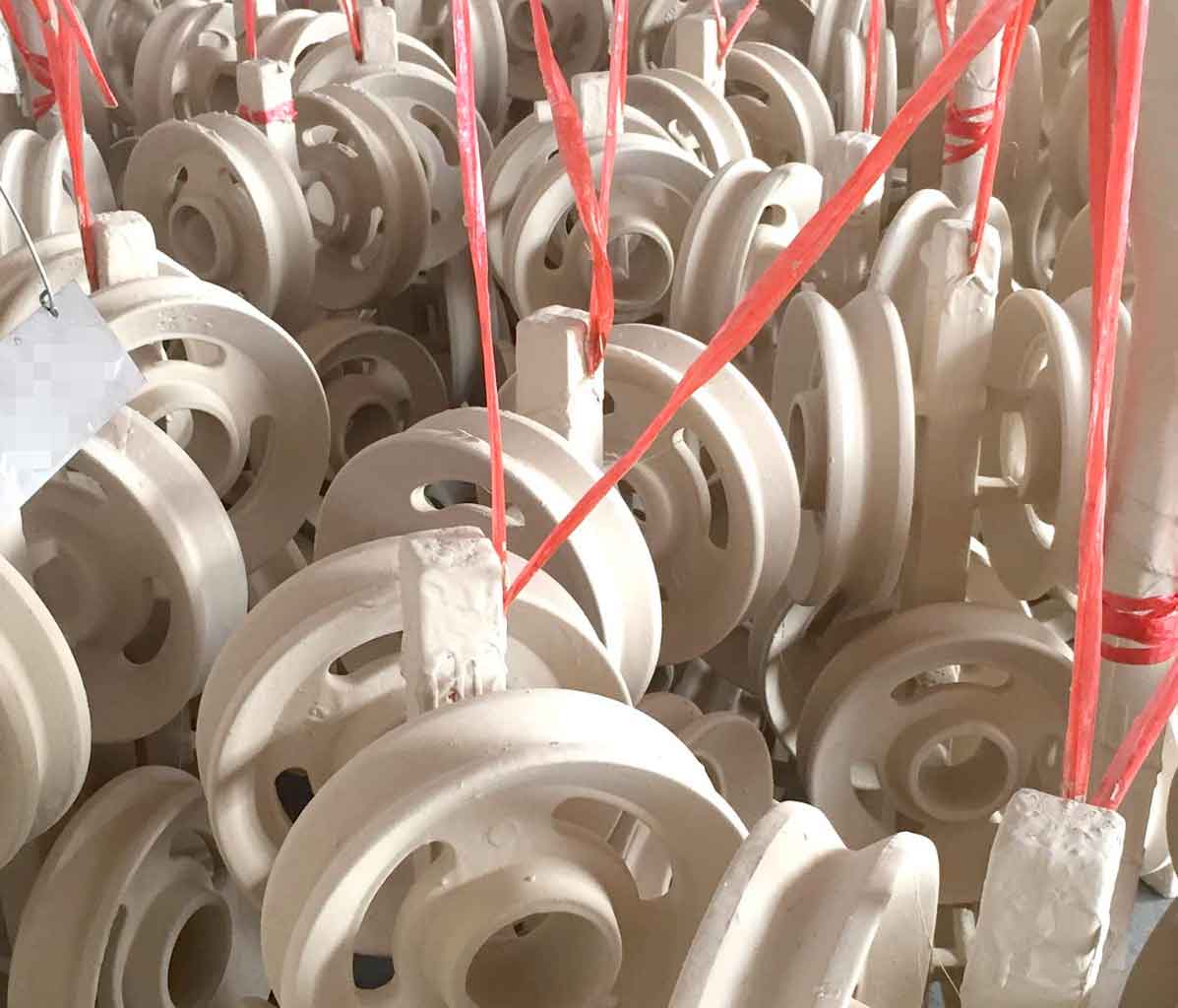
The research under equilibrium conditions shows that the decomposition rate and decomposition mechanism of pattern materials in lost foam casting play a key role. LEPs and GEPs are not thermodynamic phases, and there is no clear transition temperature. The formation of these products depends on time. Below 340 ℃, with the increase of heating temperature, the molecular weight of nonvolatile residues decreases sharply, and the polymer depolymerizes. With the increase of heating temperature, only a small amount of volatile gases are produced, such as polymer cracking and low molecular weight gases, mainly styrene monomers. Between 400 ℃ and 660 ℃, the gasification rate reaches the maximum (about 660 ℃), and between 660 ℃ and 900 ℃, The volume of gas produced by the decomposition of EPS per unit mass changes little with temperature, which is 205 ± 25cm3/g (STP). In the hotter region (above 1000 ℃), styrene will reach the pyrolysis point and begin to decompose, and styrene monomer will be transformed into gas products with smaller molecular weight: acetylene, toluene, benzene, hydrogen, oxygen, ethylene, etc. the generation of low molecular weight gas reflects the change of set gasification mechanism.
Under the non-equilibrium condition of gray iron lost foam casting, the formation process of gas decomposition products and the outward diffusion process of gas decomposition products through the coating are carried out at the same time, which is a dynamic process. The volume of gas generated by EPS decomposition per unit mass is 760 ± 25cm3/g (STP), and the gas pressure in the air gap layer acts against the hydrostatic pressure. The gasification and decomposition rate of pattern material determines the gas pressure in the air gap layer, Thus, the filling speed of molten metal is affected. Between 1340 ℃ and 1370 ℃, with the increase of lost foam casting pouring temperature, the rate of decomposition products escaping from the mold is higher than that of pattern material gasification decomposition, the back pressure in the air gap layer decreases, and the average mold filling speed of molten metal increases with the increase of lost foam casting pouring temperature. Above 1370 ℃, with the increase of lost foam casting pouring temperature, the gasification decomposition rate of pattern material accelerates, which is higher than the escape rate of gasification decomposition products from the mold, the gas back pressure in the air gap layer increases, and the average mold filling rate of molten metal decreases with the increase of lost foam casting pouring temperature. At higher temperatures, the gasification decomposition rate of model material and the escape rate of decomposition products from the mold tend to balance, The average filling speed of molten metal has little change with the pouring temperature of lost foam casting, reaching a relatively constant filling speed. In a word, within a certain pouring temperature range, the pouring temperature of lost foam casting increases, the filling time is shortened, and the filling speed is accelerated. Under the high pouring temperature of lost foam casting, the gasification and decomposition speed of pattern materials is accelerated, the gas generation is increased, and the filling speed is slow.